This column is moderated by Béla Lipták, automation and safety consultant and editor of the Instrument and Automation Engineers' Handbook (IAEH). If you have an automation-related question for this column, write to [email protected].
Q: I am interested to find out whether direct-sealing, weir-type diaphragm flow control valves for drinking water distribution can control the flow in a better way. Specifically, my questions include: 1) What are the advantages or disadvantages of a direct-sealing, weir-type diaphragm valve over a conventional globe-type valve with seat and stem? 2) Which body-type diaphragm valve (weir or globe body) has more linear characteristics? In short, which body has the best flow characteristics and why?
Niraj Taparia
Darling Muesco India Pvt., Ltd.
[email protected]
A1: The direct-sealing, weir-type diaphragm flow control valve, often referred to as the Saunders valve (a brand of the Crane product family), is typically used on low-pressure, corrosive or slurry services, where some leakage is acceptable. The diaphragm requires periodic replacement, but if the process allows periodic shutdowns that's OK, since the replacement itself is easy and quick. The characteristics aren’t ideal for control and they change with age, but Saunders valves are typically quick-opening.
On water service, rotary valves (ball, plug, butterfly) are often used, but usually only as shutoff valves. You're right that good linear characteristics can only be provided by globe valves. Also, in water distribution systems, where the supply to each user is under flow control, you can save about one-third of the pumping energy if you use a variable speed pump. With speed-controlled by a valve position controller, this approach keeps opening all user valves until the most open is nearly fully open.
Béla Lipták
[email protected]
A2: Diaphragm valves operate on the basis that to avoid corrosion or abrasion of the valve internals, you insert a diaphragm to pinch the flow. The pros of such a valve are that the material that wears out is an elastic membrane that's fairly easy to replace or repair, and your process doesn't contact the valve internals. The cons are that these valves generally don't provide hermetical shutdown, allowing for some leakage across the valve. Also, these valves will have a lower operating pressure to avoid damage to the membrane. Finally, control of these valves is also not as precise as with other valves.
Globe valves have better shutoff (less leakage across the valve) and handle higher pressures. Plus, they can be configured for very good control sensitivity.
For your application with drinking water, you can use bronze (although there may be pressure limitations) or stainless-steel valves to guarantee that no corrosion affects the water. In any case, you'll need to define the leakage allowable across the valve, which is what may make it more expensive than others.
Most diaphragm valves that I know don't have any specific flow characteristics, since any deformation of the elastomer will cause the flow characteristic to be anything but linear. If control is extremely important as well as zero leakage, you may look at ball valves with elastomer seats.
For potable water, and not knowing your specific requirements, a globe or plug valve should cover most of your needs.
Alex (Alejandro) Varga
[email protected]
A3: Saunders diaphragm valves are well suited for slurry applications (especially feed to cyclones). However, for drinking water applications, where the solids content is almost non-existent, the Saunders valve will be very costly to install and maintain. Globe valves have excellent controllability and have large capacities for smaller valve sizes.
If your line sizes are larger, then a butterfly valve will be a better option.
Raj Binney
[email protected]
Q: Is it possible to use a "voting" system between switches and transmitters simultaneously? For example, is it possible to vote two out of three (2oo3) with one on-off signal and two analog signals, such as one pressure switch and two flowmeter transmitters? By asking this question, I mean, is it possible to combine transmitter threshold outputs (that are DO signals) with a switch output? We're using voting selection between three digital signals. I understand that median selection isn't disparate from voting, but I haven't found any articles limiting median selection to analog signals.
Mehrdad Boakeaian
[email protected]
A1: Before answering your question, let me make some points about safety in this new age of AI-operated robots, drones, driverless cars, cyber-terrorism and studies that indicate that some 91% of industrial accidents are triggered by human action or error. Under these conditions the question is: "Who should have the last word—the machine or the operator (pilot, driver, etc)?"
This is the wrong question. The right question is: "Which person should have the last word?" Should it be the person who is right there at that moment (even if unqualified, drunk or otherwise incapacitated) or should the needed action be determined by the judgment of a team that spent months (in case of self-driving cars, years) to identify all potential “what if” conditions and their potential consequences before deciding on the emergency actions to be triggered when these conditions arise?
This is a very complex topic that is covered in my Instrument and Automation Engineer's Handbook (5th edition, Volume 1) or in IEC 61508 and IEC 61511. All I can say here is that in modern systems, we do have an overrule safety control (OSC) layer of control, which has been developed by a hazard and operability study (HAZOP). This goes way beyond the issues of sensor diagnostics, backup, median selection or voting systems.
Now coming back to your question of "How many sensors can vote, and can both on-off and continuous devices participate in that vote?" The answer is yes to both questions, but one should note that transmitter signals have a higher level of information content because their signal is "alive" (continuously changing) if they're functioning, while on-off devices, such as switches, are not. Beyond this, using transmitters also provides the ability to easily change the alarm or trip values, while a switch can fail without indicating that it did. On the other hand, their simple design makes them more reliable than transmitters.
Comparing median selection (in which any transmitter value that deviates substantially from the other two is disregarded) and voting systems, if you have two transmitters and one switch, median selection is better than voting. This is because the condition when only one is registering an unsafe condition would be ignored by this voting configuration, and therefore two transmitters and one switch is not a true 2oo3 redundancy system.
Béla Lipták
[email protected]
A2: This is not only possible, but potentially more reliable due to using disparate devices in the voting sequence, hence a lower chance of common-cause failure. I've used this before today in improving an existing safety system with a high spurious trip rate (without buying any more sensors!) from 1oo1 to 2oo3.
Ian H.Gibson
CPChem, RPEQ, FIICA, AFIChemE, FS Eng (TUV Rheinland)
[email protected]
A3: Convenience and reliability are not the same thing. In terms of safety evaluation; the former should be given a lower priority for consideration. A transmitter, because of its dependency on external power supply and internal electronics, is far less reliable than a simple mechanical switch that provides a pair of dry contacts in playing its role of tripping.
One needs to consider the basic operating principles of the two different instruments to evaluate overall safety and reliability. In my limited experience in instrumentation at minus 40 °C, none of the LCD displays of the transmitters work, causing a sense of insecurity to the field operators. I'd tend to request that the instrument technicians check the switches in the field more often, and not rely on an asset management system to infer overall plant safety.
Switches can't be replaced by transmitters, no matter how convenient it is to check the functionality of a transmitter. Health of an instrument system is not how fast nor how convenient it is to obtain a signal alone. Such health should also include the environment in which the instruments are installed, which governs the overall safety of a process plant. Often, as process plants get bigger, it becomes more convenient to infer safety from transmitters. However, the size and the price of accidents in process plants also become bigger as time goes by.
Gerald Liu, P. Eng.
[email protected]
A4. While this could be done, I'd be reluctant to call such an arrangement "median select." (A true median select requires three analog signals.) How are you going to handle or vote the two analog signals? 1oo2 or 2oo2? The result of those two transmitters would then be combined with the discrete signal (switch), again using either a 1oo2 or 2oo2 arrangement. So it's not exactly 2oo3.
Paul Gruhn
Former ISA president
[email protected]
Continue Reading
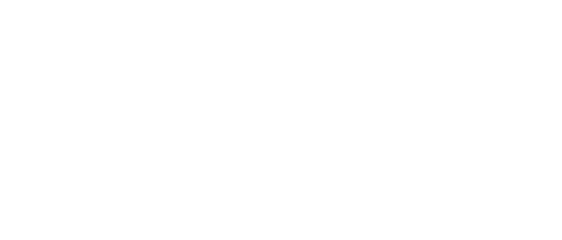
Leaders relevant to this article: