By Andrew Bond, Industrial Automation Insider
Latest version of LabVIEW promises to simplify transition to new generation of multicore processors
A National Instruments press conference at the Institution of Engineering and Technology to announce a new release of LabVIEW has become as regular a feature of the English summer as Wimbledon, Cowes or catastrophic flooding. This summer has been no exception, so last month software marketing director John Pasquarette, for whom this is also becoming a regular fixture, was back for another outing of his double act with U.K. and Ireland marketing manager Ian Bell.
Last year they were celebrating the 30th birthday of the company and the 20th of the product and were able to spice up their performance by incorporating into their act the newly introduced Lego Mindstorms NXT robot whose software is based on LabVIEW. This year they were faced with rather more of a challenge, given that the principal feature of LabVIEW 8.5, now routinely described as neither a programming language nor a measurement tool, but a “graphical system design platform,” is its support of automatic multithreading on desktop PCs and of real-time control on multicore systems.
The challenge, therefore, was first to explain the issues raised by the emergence of a new generation of multicore processors, second to explain how the new release copes with them and, third and most important, why, with the one exception of the guy in the front row whose mission in life was to demonstrate that he knew more about the subject than Pasquarette, the assembled hacks should be interested.
Dual cores ubiquitous
As Pasquarette explained patiently and in words of no more than one syllable to the rest of us, dual-core processors are now almost ubiquitous in new desktops and laptops. Moreover quad cores will reach the market later this year, and Intel is promising processors with up to 80 cores within five years.
Driving this trend is, as ever, the endless pursuit of higher performance which, with raw processing speed having virtually reached its limit, is now being sought through increased parallelism.
That however brings its own problems. Whereas traditionally software developers have been able to reckon on faster processors improving the performance of their software, these more recent developments “do not take most current applications along for their customary free ride,” as Microsoft software architect Herb Sutter put it in his article, “The Free Lunch Is Over” in the March 2005 issue of Dr Dobb’s Journal. Instead applications must be broken up into parallel paths or “threads” that can be executed simultaneously. That means, using conventional development tools, learning new functions to create, destroy, communicate between, synchronize and debug across threads.
Multithreading
Not if you’re a LabVIEW user however. LabVIEW has, in fact, supported multithreading since 1998 and has the capability automatically to divide applications into multiple execution threads. As a result, in contrast to conventional applications, existing LabVIEW applications already run of the order of 1.6 times faster on dual-core processors. Now, the latest release allows execution threads to be scaled automatically to the total available number of cores and adds improved thread scheduling for LabVIEW timed loops, as well as delivering enhanced “thread-safe drivers” and libraries. As a result, users such as Germany’s Max Planck Institute and AmFax Ltd in the U.K. are experiencing performance improvements of between five and 20 times.
As well as providing support for multithreading on desktop systems, the new release also offers significant advantages when implementing real-time control on embedded multicore systems. Symmetric multiprocessing (SMP) with the LabVIEW Real-Time environment allows automatic load balancing of tasks across multiple cores while maintaining determinism. Additionally, users can manually assign portions of code to specific processor cores to fine-tune real-time systems or isolate time-critical sections of code on a dedicated core. And the new Real-Time Execution Trace Toolkit 2.0 visually displays timing relationships between sections of code and the individual threads and processing cores where the code is executing. The same inherent parallelism is also claimed to make LabVIEW ideal for developing FPGA (Field Programmable Gate Array) applications, with an FPGA Project Wizard automating I/O configuration, IP development and overall setup for common I/O, counter/timer and encoder applications.
Statecharts
The other major innovation in LabVIEW 8.5 is the introduction of a new Statechart module which allows the design and simulation of event-based systems including, for example, safety-critical applications, based on the UML (Unified Modelling Language) standard. Also specifically aimed at industrial applications are a range of I/O, measurement and display enhancements for building PAC (Programmable Automation Controller)-based systems, including a new library of OPC drivers that nearly doubles the number of compatible PLCs and industrial devices supported. In addition, a new multivariable editor makes it easy for users to quickly and easily configure or edit hundreds of I/O tags in high-channel-count systems using a simple spreadsheet interface.
Also new are a set of flexible pipe display tools to simplify the building of more realistic industrial user interfaces and an interactive drag-and-drop approach to tying I/O tags directly to displays running on Windows CE-based industrial touch panels and handheld PDAs. Control design and simulation enhancements include Model Predictive Control (MPC) and analytical PID controller design.
As always with National Instruments presentations, admiration for the ever-increasing range of capabilities is tempered by the seeming arrogance of proposing solutions for applications in specific industries which wholly ignore the standards of those industries. Thus, although the specific example of an industrial application cited by Ian Bell was a simple, almost archetypal, batch control application, the question “Why would one use LabVIEW for this rather than a development environment which complied with the increasingly widely accepted IEC 61131-3 standard?” evinced no very convincing explanation other than that conventional PLC-based systems could not meet the requirements of all industrial applications.
Well, true. But it’s still difficult to see how LabVIEW or NI can achieve anything beyond niche market status in industrial applications if they persist in regarding compliance with the relevant IEC standard as somehow beneath them.
Vendors seek security behind Berlin firewall
Ever since the issue first came to wider public attention in the wake of 9/11, discussion of industrial cyber security has been largely dominated by North American voices, notably those of Industrial Defender, formerly Verano, president and CEO Brian Ahern and Eric Byres, late of the British Columbia Institute of Technology and, more recently, partner with MTL in the development of its Tofino offering. But while Ahern, Byres and others have done a great job in raising awareness of the potential threat, it’s less well-known that Europe has been making its own contribution to producing workable solutions. Indeed the Berlin-based start up Innominate Security
Technologies has been developing a range of industrial solutions since 2001 and deploying them since 2003.
Invisible and undetectable
Given the nature of its technology and its chosen route to market, it is perhaps not surprising that the Innominate name is not as widely known as it should be. A fundamental principle of the patented “stealth-mode” technology on which its mGuard range of products and solutions is based is that they should be “invisible, undetectable and invulnerable” while it goes to market principally through partners and OEMs including Hirschmann, Phoenix Contact, Siemens and SAGEM, who either embed the technology in their own products or rebrand the Innominate products under their own names. “We have a field proven technology that is installed 10,000 times in the field. It’s absolutely reliable technology,” explained CEO Joachim Fietz, who nevertheless acknowledges that, to date, “What we have missed is in sales and marketing.”
Innominate has based its approach from the outset on a recognition that plant-floor security needs are radically different from those of conventional IT, and that there is, therefore, as Fietz puts it “a specific market of industrial security.”
Vendors of practical security solutions must be able to cope with heterogeneous collections of hardware and software, obsolete operating systems lacking any kind of security support, system life cycles of between 10 and 20 years, sales cycles of 24 months or more, and an almost total lack of security expertise at the plant level, says Fietz. Above all they must recognize that, for most industrial users, irrespective of how seriously they take the cyber security threat, the golden rule is “Never touch a running system.”
Auto configuration
Moreover, says Fietz, it’s all too easy for industrial cyber security to fall down the gap between corporate IT, which doesn’t wish to get involved with plant-level systems, and production personnel who lack IT security expertise. It’s that recognition which led to the development of the other key characteristic of Innominate’s offering, Auto Configuration. The “Plug &Protect” solutions are designed to be entirely compatible with all operating systems, entirely transparent to and in no way to interfere with the systems being protected, and to require no changes to existing networks. Most important of all they don’t require any IT security expertise for their installation and implementation.
The mGuard firmware, now in its fifth release since its original introduction in 2003, has three primary functions: VPN (Virtual Private Network) for secure data transmission in remote service applications; configurable firewall; and, optionally, integrated virus protection. Transparency and invisibility are achieved by mGuard itself having no IP address, but sharing the address of the device which it is protecting, thus ensuring that it cannot itself be attacked. The complementary hardware is based on a special network processor running embedded Linux and comes in a number of configurations which can be incorporated into the protected device at the network cable, integrated as a PCI card or deployed in a top-hat rail mounting version. In addition the mGuard bladePack provides for the protection of up to 12 devices simultaneously or six in hot standby mode. Common to all configurations is the fact that the protected system does not have to be reconfigured, nor driver units or other software loaded. Moreover, the company claims that the operating system never has to be updated again with security patches.
mGuard effectively allows the appropriate level of protection to be applied to each individual device but the potential administrative burden created by such an approach is mitigated by a rule-based Configuration Manager which, using a graphic network model, allows multiple mGuard systems to be configured. Firewall rules, VPN configurations and NAT settings are then loaded directly on to all devices and activated, and VPN connections both between mGuard devices and with other vendors’ gateways set up and managed.
Blue chip clients
Joachim Fietz is careful not to make direct comparisons with other vendors’ offerings although he did ask somewhat pointedly whether and where INSIDER had actually seen an installed Tofino, as well as acknowledging that the company had yet to get its hands on a Honeywell Control Firewall. What is clear is that mGuard has persuaded vendors such as Hirschmann and Phoenix Contact, and through them even bigger names, including Emerson Process Management who, we understand, are using the technology with DeltaV, of the futility of developing its own industrial cyber security technology when such a comprehensive solution is already available. With such blue- chip names being added to the customer and partner base, its seems unlikely that Innominate will much longer remain in that peculiarly European category of “best kept secret”—nor that it will be much longer before its European and U.S.-based venture capital backers receive an offer that they find it impossible to refuse.
MTL makes it three in three months
MTL Instruments Group has announced its third acquisition in as many months, paying £3.0m in cash for Sutton, U.K.-based specialist SCADA supplier Ocean Technical Systems (OTS). In May MTL announced the acquisition of Australian wireless solutions developer Elpro International, and in June it bought a 90% stake in Knaresborough, U.K.-based process alarm specialist RTK Instruments. The OTS deal brings the total amount expended by MTL on acquisitions in the last three months to £18.7m.
Project capability
OTS is an international provider of SCADA solutions for the automation of the berthing, loading and unloading of oil tankers and of oil production vessels, floating production units (FPSOs), unmanned wellhead production platforms and oil and gas pipelines. As an original equipment manufacturer, it has a complete project support capability covering project management, procurement, manufacturing and documentation and is ISO
9001- and TICKIT-accredited. Its particular specialty is the provision of remote monitoring and control systems for use on unmanned structures, such as SPM buoys and satellite platforms, in the form of remote wellhead control. The company also claims large scale SCADA and DCS system integration capabilities to provide FPSO-integrated control systems, pipeline monitoring systems and metering systems and offers an innovative real-time metering database.
With the majority of its equipment designed to operate in hazardous and potentially flammable environments, OTS is seen by MTL as a natural fit with its own range of hazardous-area control and instrumentation equipment. As with other recent acquisitions, the aim is to extend OTS’ international customer base by leveraging MTL’s sales channels and OEM relationships, while at the same time improving its competitiveness by exploiting MTL’s purchasing power and electronic circuit board manufacturing capability. The company says that it expects the acquisition to be earnings-enhancing in the first full year of ownership.
“Ocean Technical Systems is another excellent acquisition for MTL,” said CEO Graeme Philp, who is becoming something of a dab hand at making these statements. “Over the last few years it has developed an innovative and highly competitive range of SCADA and navigation products for the automation of the berthing and loading of oil tankers and oil production vessels and the monitoring of oil and gas pipelines. By giving OTS access to its international sales team, MTL will help to accelerate the expansion of its international reach.”
Despite Philp’s enthusiasm, however, there may be some who will wonder how the acquisition of a specialist SCADA system vendor fits with his previously declared strategy of becoming the leading supplier of building blocks for process automation systems, and whether there is not a danger of transforming a previously tightly focused group into an increasingly diverse conglomerate of loosely related businesses.
Citect takes control of Yorkshire’s electricity
Citect has supplied a 50,000-point CitectSCADA system to Yorkshire Electrical Distribution Limited (YEDL) to provide remote control and monitoring of hundreds of remote electricity sub-stations in the West and South Yorkshire area of the U.K. YEDL, which serves the cities of Leeds, Bradford, Sheffield and Hull and the surrounding area, has implemented the £40,000 distribution control system as part of the Information Incentive Project initiated by U.K. energy regulator OFGEM to improve the quality of supply to users through superior control and monitoring of the distribution network.
The Citect system, which was developed and installed by ABB working with the support of Citect professional services, uses remote RTUs communicating to two central servers using the DNP3 (Distributed Network Protocol) driver, which comes as part of CitectSCADA, and has been specially expanded by Citect to accommodate around 1,000 remote sites.
“CitectSCADA came highly recommended,” said YEDL technical engineer Graeme Melia. “We liked the fact that it is a very expandable system and extremely easy to use. Using the software we have just five templates covering all aspects of the distribution control system; if we want to add a new site, we just add a line and tell the SCADA system which template to use, then it’s job done.”
Benefits
Principal benefits of the new system are the ability to switch networks around to restore supply after faults have occurred; the ability to set up protection remotely on pole-mounted auto reclosers to enable safe working on the system, sometimes on live conductors; and the reduction in travel time resulting from being able remotely to control equipment scattered across the supply area. “We decided to use our existing private mobile radio (PMR) as our transmission medium because the technology already exists at many of our sites,” said Melia, who pointed out that PMR is mature, well proven and offers a blanket coverage totally independent of the electricity distribution network.
The PMR/DNP3 network currently covers 1,000 sites and is linked to a central control room housing two 50,000 point servers, one of which is configured as a cold standby, and four display clients which are manned 24/7. All events are recorded and archived to an external log, providing a transparent operating record.
Iconics gets Vista certification
Iconics is the latest automation software vendor to announce Windows Vista certification. The Iconics certification is for its GraphWorX32 package, which is used to create animated graphics in the Genesis32/Genesis64 HMI/SCADA, and BizViz Manufacturing Intelligence/Business Visualization suites. “Manufacturers are drawn to Windows Vista due to its increase in performance,” said Iconics president and CEO Russ Agrusa, “as well as to the powerful improvements in visualization. With Windows Vista, we can now give our customers a 360-degree view of their entire enterprise.”
Perhaps surprisingly, Iconics makes no mention in its announcement of the enhanced security offered with Vista, which was the principal reason for achieving certification cited by the first SCADA vendor to do so, Copa-Data.
ISASecure regime moves a step closer
Following repeated calls for an independent body to establish standards and a compliance regime for industrial cyber security, ISA has announced plans to establish a Security Compliance Institute. The move follows a meeting between the ISA-sponsored Automation Standards Compliance Institute (ASCI) and an ad hoc group of influential asset owners and suppliers of industrial automation technology and services in May of this year which set out a program aimed at facilitating independent testing and certification of control system products to a defined set of control system security standards.
The program would use existing control system security industry standards where they were available, develop or facilitate the development of interim standards where they aren’t, and adopt new standards as they become available. To that end it would aim to accelerate the development of industry standards that can be used to certify that control systems products meet a common set of security requirements.
An important aim of the program is to allow control systems products to be integrated securely with the ultimate goal of pushing conformance testing into the product development life cycle so that the products are more intrinsically secure. A well-designed and managed product security certification process would reduce the cost and time expended by asset owners in product selection and deployment and reduce time to market and development and integration costs for vendors and integrators.
Key differentiator
Standards bodies and government agencies would also benefit from better, field-tested standards that were clearly being followed by industry. “The ISASecure designation that is expected to arise from the effort will identify and promote security standards conformant products and systems,” said ASCI managing director Andre Ristaino. “Certification provides the formal recognition of a product’s conformance to an industry standard security specification, creating a key differentiator for the product.”
ISA is currently circulating a membership prospectus summarizing the scope of the program, member benefits and member commitments. It specifically solicits Founding Strategic Members to provide strategic direction and funding. Membership applications must be submitted by September 1. The 21-month launch plan envisages conformance certifications starting in June 2009.
ABB claims first with fully integrated PAT solution
Industrial IT for Process Analytical Technology (IIT for PAT) is ABB’s response to the U.S. Food and Drug Administration (FDA)’s draft version of its “PAT—A Framework for Innovative Pharmaceutical Manufacturing and Quality Assurance” guidance first issued in 2003. The FDA and industry groups have been promoting PAT with the aim of moving pharmaceutical manufacturing from low- to high-efficiency; from high- to low-cost; and from quality by testing to quality by design. “The aim is to focus on the process rather than the end product,” explained Thomas Buijs of ABB’s pharmaceutical center of excellence.
PAT would also lead to improved automation and operator safety, reduced product rework and waste, real-time release of product and continuous improvement. However, adoption of the concept by the life-science industries has been frustrated by a lack of technology which will consistently integrate the different analytical techniques used in pharmaceutical manufacture with automation systems.
IIT for PAT provides a single configurable and scalable system that will collect data from any vendor’s analytical instruments and analyze the data to determine the actual condition of the process. It then passes the resulting information to the control system, which adjusts its outputs to improve or optimize the process. Because the solution is scalable, life-science companies can apply it within a development environment and then scale up to the production plant. Similarly, it can be applied to a single process unit, such as a dryer, or scale up to the full production facility.
Consultancy
ABB is also providing consultative services and engineering expertise to help users to interpret the FDA initiative and to identify the benefits of using PAT, validation and business expertise to aid the cooperation between the different departments, such as quality control, validation, automation and chemistry. It claims that IIT for PAT can reduce cycle times by up to 40%, cut production costs by as much as 30%, increase right-first-time production levels from 90 to 99.9% and reduce by half the non-value-added time and costs involved in laboratory testing and paperwork. In addition, it claims improved production consistency, reduced inventory and lower costs and regulatory issues in upsizing from laboratory to full-scale production and the ability to change purely batch processes into continuous manufacturing processes.
ARC’s Maurice Wilkins describes IIT for PAT as “the world’s first fully integrated PAT solution,” adding that its flexibility and architecture “allows customers to easily integrate it into new or existing processes to achieve the benefits that have been promised by PAT,” while ABB’s Thomas Buijs claims that it will “enable customers to change the way pharmaceuticals are made.”
Emerson’s order book emphasizes Asian impact
The degree to which China and the Far East are coming to dominate process automation vendors’ order books is emphasized by the latest clutch of announcements from Emerson Process Management. Top of the list is the company’s selection to automate digitally what is claimed to be the largest integrated refining and petrochemicals project ever undertaken in China, the Fujian Refining and Ethylene Joint Venture Project in Quanzhou City, Fujian Province, which is scheduled for start-up by 2009.
Emerson’s involvement follows its completion last September of front-end engineering and design and includes project management, engineering, integration, testing, commissioning and other site services, all handled out of its Pudong, Shanghai, facility. It will also act as Main Instrument and Controls Contractor (MICC).
The project is a joint venture between Fujian Petrochemical Company Limited, itself a 50/50 venture between Sinopec and Fujian Province, ExxonMobil China Petroleum and Petrochemical and Saudi Aramco Sino, with Fujian’s involvement 50% and each of other two 25%. It will expand existing refining capacity from 80,000 to 240,000 barrels per day and add new petrochemical facilities including an 800,000-tons-per-year ethylene steam cracker, an 800,000-tons-per-year polyethylene unit, a 400,000-tons-per-year polypropylene unit and an aromatics complex to produce 700,000 tons per year of paraxylene together with a 300,000-tons crude berth and associated utilities.
DeltaV x 8
Emerson’s PlantWeb installation will include eight DeltaV systems, AMS Suite: Intelligent Device Manager software, SIS, fire and gas systems, Rosemount pressure and temperature transmitters and Fisher digital valve controllers.
Meanwhile in Zhuhai, China, Emerson has been selected as main instrument vendor for BP’s Purified Terephthalic Acid (PTA) plant expansion and will again handle the project from its Pudong, Shanghai, Chemical Centre of Excellence. The PlantWeb installation will include Rosemount measurement and analytical instrumentation, Micro Motion Coriolis flow and density meters, Fisher control valves with FieldVUE digital valve controllers and DeltaV, the last running Emerson’s Advanced Control Suite comprising DeltaV Insight, Inspect, Tune, Fuzzy, Neural and Predict Pro. DeltaV SIS will be installed on an independent network, with diagnostics communication to the process systems.
And still in the Far East, Emerson has been selected as main instrumentation vendor for Lucite International’s methyl methacrylate (MMA) plant currently under construction in Singapore and scheduled to begin operation in 2008. The plant will be the first to utilize Lucite’s patented Alpha technology which is set to end the MMA industry’s historical dependence on scarce acetone, HCN and isobutylene, instead using readily available ethylene, methanol and carbon monoxide. The Singapore plant is the first in a series of Alpha-based production facilities which Lucite plans to build around the world. Emerson’s contribution will include SIS and plant and laboratory information management systems.
Latest from SCADA
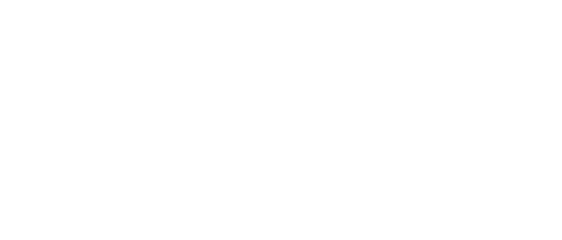
Leaders relevant to this article: