The concept of a remote operations center in process manufacturing was not a foreign idea at the beginning of 2020. Particularly in the oil and gas industry, many upstream companies had started developing remote hubs over the last decade to monitor offshore wells.
But now, supporting remote operations where the central operations team itself is distributed or working from home is easier than ever due to innovations in connectivity, mobile devices and technology. Distributed teams can smoothly transition to the new reality of remote work using innovative software and communications offerings to enable analytics and collaboration across the value chain.
Shifted reality
Over the past few months, many process industry teams were instantly thrust into distributed work due to coronavirus restrictions. This brought about multiple paradigm shifts, the first among them being the loss of in-person interactions.
Many plants started the morning with a meeting where engineering, management, maintenance and operations personnel got together to collectively plan their day. If there was a question from a team member after the meeting, he or she would have normally just swung by someone’s desk. These types of in-person interactions were no longer possible when working with distributed teams, so many companies rapidly deployed and learned how to use software tools to give their now remote meetings a similar feel.
Interactions over a coffee pot have now transitioned to text/instant message or video conference calls, a familiar situation at Seeq as our company was set up as a fully virtual organization from day one back in 2013. To ensure efficient operation, we’ve developed a list of best practices for working from home.
For example, video chat is used whenever possible because context can be lost when relying solely on the spoken or written word. Team leaders are tasked with setting clear guidance on the content to be covered in meetings. They must also ensure each participant knows expected key outcomes, and then track progress.
Using these guidelines, meetings have become a great time to reset expectations within a team, and ensure members are working on high value-add activities.
Technologies for collaboration
Once teams have settled in with distributed meetings, another key to success is choosing a technology solution to enable communication across organizations for decision support. Requirements include analytics tools, along with workflow enablement software to ensure everyone is on the same page with current operations, and with any changes.
Imagine an engineer finding a million-dollar opportunity using an advanced analytics application, but without a way to communicate this finding quickly and easily to the rest of the organization. This could delay implementation with consequent operational losses or, in a worst-case scenario, increased risk of a serious incident.
To facilitate these and other types of communications, there must be a central storage location for information critical to operations. If information is buried on someone’s computer or on a network drive, it will hinder monitoring of plant status, communication of changes and alignment across the organization.
Cloud-based solutions are a very popular and effective way to ensure the right data and information is always available to the entire team. To aid in these types of deployments, advanced analytics and other applications should be available as software as a service (SaaS) on leading cloud platforms such as AWS or Azure with an option for hosting on an end-user company’s private cloud.
No matter the application or cloud platform, all employees must have access wherever they're located. Applications and platforms built with a strong foundational architecture will ensure there will be no latency issues due to VPNs or firewalls, while providing effective security measures.
Advancing analytics
Assuming the organization has addressed the need for applications, data and information to be located in an accessible location, the next step is making sure everyone, no matter where they reside, has the right tools to perform their work.
In process manufacturing, there are many different types of software that can be useful to the different parts of the organization. These include advanced analytics for technical teams and tools for flawless shift handover, along with reporting capabilities to summarize operations.
The first thing to be considered is ease of use for updating and historizing events and reports. For example, the team will want to make sure the operator shift log can be easily updated by any technician with all copies accessible for future reference from any location.
As another example, engineers need to perform advanced analytics on their unit operations. Excel used to be the preferred tool for engineers, but it required them to spend hours doing data wrangling, only to be left with little time for in-depth analysis. Due to the inefficiencies of this approach, many are implementing advanced analytics solutions to take advantage of flexible trending, a suite of visualization options and the ability to execute complex calculations.
Management should be able to view key performance indicators locally or remotely from a dashboard, and they should be able to update these reports with the click of a button and comment on current plant status, while easily referencing prior day reports (Figure 1).
Figure 1: an example plant operations dashboard includes key performance indicators, inventories, safety and environmental information—and can be rolled up from sources such as operator shift handover and unit technical reports. Built using Seeq’s Organizer tool.
When selecting the best tools, it's important to investigate how each tool fits with the rest of the technology stack. For example, if an engineer is trying to perform advanced analytics on process data, the organization likely already uses a historian or a data lake in the cloud containing relevant data. Therefore, the advanced analytics software—or any other application requiring access—should be able to connect to process data already available in the historian, data lake or other systems.
The better these software applications can connect to each other and enable effective data-based decision-making, either in plant or from afar, the more quickly an organization will be able to add value to the bottom line.
Challenging the old normal
Eventually teams will return to the office and a more traditional workflow. When this happens, groups should be encouraged to spend time reflecting on their experience working as a remote team and identify places where efficiencies were gained. Managers should lead by example and adopt new normal best practices identified during this period.
Post-COVID, some teams may transition entirely to remote meetings because it saves travel time and money. Others might switch to regular remote working days to provide employees with an uninterrupted focus on the task at hand. If someone’s workload was trimmed because it wasn’t adding value, it shouldn’t be added back because “that’s the way it's always been,” but should instead be used as an opportunity to assign more important tasks to that person.
The end goal for all process manufacturing organizations is to maintain safe, reliable and optimized operations. With an effective communication structure and software solutions for advanced analytics and improved workflows, teams are empowered now more than ever to achieve this goal, even while distributed across the globe.
About the author
Latest from Home
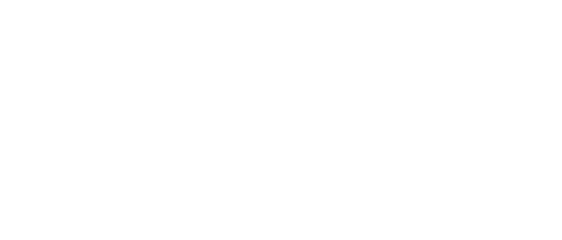
Leaders relevant to this article: