Corrosion in refineries often is caused by contaminants in produced hydrocarbons that, over time, lead to deterioration of pipe and vessel walls. Loss of equipment integrity can result in unplanned downtime and costly repairs or, in the worst case, a catastrophic event posing major risk to personnel, the environment and stakeholder value.
Exacerbating the problem, many refineries no longer process the specific type of oil, such as sweet crude, they originally were designed to handle. The changing nature of oil feedstock magnifies corrosion problems in aging refineries.
Refiners have two principal mitigation strategies against corrosion: upgrading the metallurgy of many or all the susceptible areas, often to expensive high-nickel alloys or titanium; or using chemical corrosion inhibition treatment.
Both strategies should include online corrosion monitoring at critical locations to verify the state of the metallurgy upgrade or the inhibitor distribution and effectiveness. Alternatively, online corrosion monitoring can validate that the existing mitigation strategy is performing adequately.
Refineries can turn to two methods to measure corrosion: probes and ultrasonic sensors.
Corrosion probes, which have been in use since the 1960s, rely on an intrusive element with a sacrificial tip that sits in the process fluid. As the sacrificial tip corrodes, its electrical resistivity changes. The corrosion of the sacrificial tip is used to infer the level of corrosion being experienced by the surrounding equipment.
While simple to use, corrosion probes suffer from two disadvantages:
- The center line measured corrosion at the tip may not match the corrosion rate at the pipe wall.
- The tip often corrodes away after two to three years while many refineries now operate five or more years between major turnarounds.
Traditional ultrasonic manual inspection techniques only provide a snapshot of equipment integrity. Typically, personnel take measurements every six months to five years. Such long intervals between measurements pose a significant safety risk because a serious event can happen in a matter of hours or days. These traditional methods can’t provide the accuracy, quality and frequency of data necessary to find problems, so mitigation can’t be optimized without interrupting operations.
Today, refiners instead can opt for permanently installed, wireless ultrasonic wall-thickness-monitoring sensors for corrosion monitoring. The units generate on a continuous basis the data required to make proper decisions and provide this information directly to plant personnel. These ultrasonic sensors, part of a WirelessHART network, are non-intrusive, so their installation cost is low, and can be mounted almost anywhere. Wireless data retrieval eliminates the need for cables, further decreasing installation and ongoing operating costs. Moreover, power packs should last until the next plant turnaround (typically, nine years’ service is achievable). The simplicity of installation and long power-pack life make ultrasonic sensors well suited for use in remote locations only accessible during turnarounds.
Giving plant personnel access to this kind of corrosion information enables them to make the right decisions at the right time about when and where to carry out critical maintenance to support safer and more-economic operations.
Installing non-intrusive corrosion sensors, a wireless network and PC-based software to process the data doesn’t require a multi-day project mandating asset shutdown. Actually, deploying a real-time wireless corrosion monitoring system at strategic locations on the outside of equipment only takes a matter of hours without any interruption to refinery operations.
For more information, please visit the HART Technology page on the FieldComm Group website.
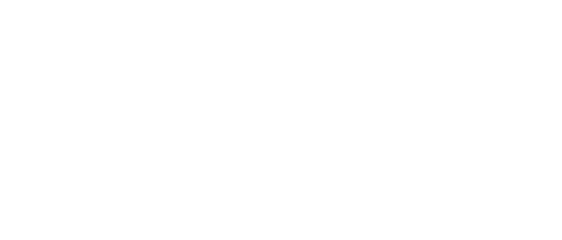
Leaders relevant to this article: