This article was printed in CONTROL's March 2009 edition.
Greg McMillan and Stan Weiner bring their wits and more than 66 years of process control experience to bear on your questions, comments, and problems. Write to them at [email protected].
Stan: What was with the flat glass craze of the 1990s?
Bob: The decrease in fouling and abrasion originally touted was actually due to the narrowing of the chamber of the specialty flow cell, which increased the velocity and turbulence past the sensor and the flush mounting of the sensor glass. When flat glass electrodes were installed without the special flow cell, the supposed advantage turned into a disadvantage in many cases because the flat glass is not as rugged and cannot handle extremes in operating conditions. The flat glass is prone to fractures and premature aging. Yet most glass manufacturers offer flat glass because of public perception. This is the placebo effect John mentioned last month, "The Secret Life of pH Electrodes–Part 1".
Greg: In defense of the customer. I haven’t seen any definitive studies on the effect of bulb shape and fluid velocity and viscosity on coating. In Monsanto and Solutia we used the rule of thumb of 5 fps to 7 fps to minimize coatings in monomer streams.
John: Even though the user can prevent coatings and abrasion with spherical or dome bulbs by fluid velocity and shroud design, most electrode suppliers offer a flat glass. If a competitor has it, you need to need to offer it to deal with the hype and appear to have a complete line.
Greg: A thin coating greatly slows down the electrode response by blocking the jump of hydrogen ions from the process into the glass. If the coating gets really thick, what are you measuring and how do you clean it?
Bob: If you take a pH electrode from a sample of peanut butter and stick it in jelly, you will be reading the pH of peanut butter. Whatever you would use to get peanut butter off your shirt is what you should use to clean the electrode. In other words, detergent and not extreme caustic, acid or exotic solvents are effective and not detrimental to electrode life.
Stan: What about the differential electrode first offered by Great Lakes Instruments (now Hach) where the internal reference was actually another glass measurement electrode? This eliminated the poisoning of the internal silver/silver chloride electrode in cyanide and sulfide streams, since it was now inside a glass electrode.
John: The real success of this electrode was the result of a prorated price of replacement electrodes based on the expected life left.
Greg: The reference was not completely immune from contamination problems in that the process could get into the buffer solution surrounding the internal glass electrode through the reference junction changing the pH and hence, the reference potential. The reference now had a high resistance path and equilibration time that would increase with both natural and premature aging from high temperature exposure or chemical attack. It was a good innovative solution for difficult wastewater applications.
Stan: In wastewater, the pH accuracy and control requirements are lax, since the pH control region is often 6 pH to 9 pH and in some cases 2pH to 12 pH (RCRA limits). For many chemical and all biopharmaceutical processes the error must be less than 0.02 pH.
Bob: Frequently customers ask me how tight their pH measurement is. I make an analogy: An electrode is like a golf ball. How close you get to the target depends upon the expertise of the golfer, the quality of his equipment and the environmental conditions. The same goes for pH measurements. Repeatability or precision matters more than accuracy for most processes, but ultimately depends on the operator and the process. There may be individual 0.01 repeatability errors from calibration techniques, reference junction potentials and glass asymmetry. You must be consistent in your calibration, installation and maintenance practices.
Greg: The control error for automatic control systems depends on the speed and size of the disturbances, mixing and injection delays, final element resolution (e.g., control valve stick-slip), electrode lag and the controller tuning. For bioreactors, the disturbances are so slow that the mixing and injection delays may not be consequential, so the primary emphasis is often on final element resolution, controller tuning and the precision and response of electrodes. The electrode lag is negligible for new and clean electrodes. Unfortunately, coatings or high temperature exposure and sterilization can cause huge electrode lags of an hour or more.
Stan: One of the ongoing concerns is glass breakage. We used glass bulb shroud designs and probe location to reduce this problem. We depended upon pump screens to trap welding rods, bolts and wrenches and never installed the electrodes during water batching. We also minimized the removal and handling of electrodes and in some cases, reduced the process fluid velocity.
Greg: For processes with abrasive particles or hydrofluoric acid, metal oxide electrodes were used, but my understanding is that these are also ORP electrodes in that the potential developed by the electrode would change in the presence of small amounts of oxidizing and reducing agents. Just 10 ppm chlorine or 100 ppm ascorbic acid can make the measurement go crazy.
Jim: In the old days antimony was used even though trace sulfides buildup put the sensor out of action in about four hours. Nonlinearity, heightened temperature effect and the 2-pH isopotential point required special calibrations, and operation below 2 pH was not recommended. Antimony is extremely poisonous, but it is used today in 95% of the pH measurements of the stomach because the sensor is so small, and there is no glass breakage concern.
Greg: The research department of a chemical company developed an iridium oxide electrode in the 1980s with a Nafion coating to eliminate the ORP response. Wishful thinking lent a blind eye to the fact that the Nafion coating only slowed down the ORP response and slowed down the pH too.
Stan: For food processes where there is a hyper concern about glass, what do customers do?
Jim: Users go to slip streams and automated sampling to keep the glass electrodes out of the main process streams. Some users also use ISFET though the silicon sensor is a ceramic that can break into jagged pieces. User reviews have been mixed because the sensor is attacked by caustic, and the integrity of seal of the silicon sensor is not rugged. The ISFET cannot be used for “clean-in-place” (CIP). On the plus side, the ISFET is extremely fast. It can make a good lab electrode if you avoid high pH samples.
Greg: Since the ISFET requires no conditioning you wonder if it would be helpful in the low-water or non-aqueous measurements that we run into for specialty chemical reaction control if you could solve the reference electrode problems.
Stan: The ultimate test would be to put a new electrode in the process alongside the old one and compare performance under actual conditions.
John: Users today don’t seem to have time to coordinate a test even with assistance by the electrode supplier or report on the results. In fact, even the most rudimentary process information these days about an application is rare. This makes it difficult to pick the best electrode.
The Top Ten Things Electrodes Would Say If Electrodes Could Talk
10 Are you listening to me?
9 Ouch that is hot!
8 Oops! Here comes another slug of caustic!
7 What happened to that cozy buffer?
6 Slimed again!
5 Is that a wrench headed my way?
4 I am the sensitive type!
3 Ouch! Would you handle your knick knacks like this?
2 I am slowing down. It must be old age.
1 I like to taste the jelly with my peanut butter.
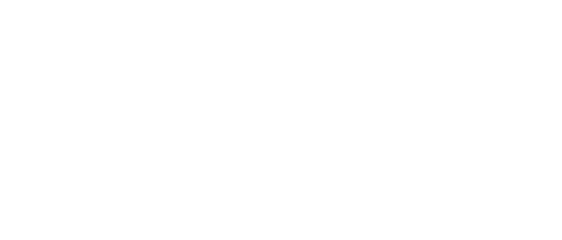
Leaders relevant to this article: