The challenges of global competition, higher production costs and increasingly stringent environmental standards need to be met by companies in the life-sciences industry. That means streamlining manufacturing processes while minimizing water, energy and material costs.
Challenges for life-sciences companies include managing patent expiration, reducing time-to-market, managing the high level of attrition in the R&D pipeline, reducing cost and productivity within the constraints of compliance, creating sustainable manufacturing processes and addressing the issues created by consolidations driven by mergers and acquisitions.
"Very often a product can fail after $900 million has been spent on it, so there's a huge risk," warned Paul Greene, business manager, global solutions, at Rockwell Automation. "From a cost and pipeline perspective, you're seeing a lot of consolidation. It's creating an enormously diverse manufacturing network. In the pharmaceutical industry, there are potentially harmful byproducts, so we're also seeing a lot more focus on end-of-line treatment."
Three companies shared how they optimized their production and the consequential improvements they realized at this week's Life Sciences Industry Forum at Rockwell Automation Fair 2009 in Anaheim, Calif.
Track-and-Trace at Bosch Packaging Services
Drug counterfeiting has become a major issue for pharmaceutical companies and governments around the world. The threat to patient safety and the economic impact of drug counterfeiting has made this a top priority.
"Just looking at a product doesn't tell you if it's an original or it's a counterfeit," said Sandro Gisler, manager, marketing and product development at Bosch Packaging Services, who related his company's story of creating a track-and-trace solution with mass serialization capabilities in a regulated production environment. "Track-and-trace is the tracking and tracing of products through the supply chain from manufacturing to the end customer. It's used for high-quality requirements, when there's an impact on consumer health and safety, when there's a threat of counterfeits and in case of the need for a full product history."
According to Gisler, three levels of functionality must be implemented for track-and-trace. Systematic Printing and verifying numbers on each package. Unique serial numbers are required for mass serialization. And the information has to be entered and maintained in a database.
Bosch has 17 manufacturing and packaging plants around the world with in-depth knowledge of pharmaceutical processing and packaging, as well as longstanding experience in the automotive industry, which has used track-and-trace for years.
Bosch's scalable carton-printing system can be used for print-and-verify mass serialization and product traceability. The Bosch modular concept of printing and control systems can be integrated into new or existing packaging lines or complete production plants of all manufacturers.
The machine that was developed, the CPS High End, is a stand-alone unit to make it easier to validate the component. "The throughput is 400 cartons per minute, and it has a relatively small footprint," said Gisler. "The CPS High End receives cartons from the outfeed belts of the upstream machine. Cartons are then transported through the printing module via a belt system. Once in the infeed zone, the carton is guided between the upper and lower belts. In this area, the carton is printed and print quality is verified."
The serialized solution includes a central FactoryTalk Pharma Suite server and site database, which interfaces to third-party enterprise systems, along with FactoryTalk Pharma Suite clients for rework scanning and high-speed device management on an Ethernet network. The operator must see what happens on the machine, so the HMI was developed with all components, from the camera to the printer, in mind.
MES at F. Hoffmann-La Roche
A Swiss-based pharmaceutical company that's more than 100 years old with 80,000 employees on all continents, F. Hoffmann-La Roche (Roche) chose a global approach to its manufacturing execution system (MES) governance and implementation. "We try to standardize our processes," said Robert Fretz, global head of process automation and MES at Roche, where the global MES program is centrally managed to support local implementations. It includes a global competency center and implementation of standardized supply chain processes. A common, standard MES core application is rolled out at local sites, and the implementation is driven by business objectives.
"We start with a standard vendor system and we add limited customizations to it," said Fretz. "A little more than 10% of the system is customized. We start with a common system specification, and then we hand it over to Rockwell. If there are customizations, they will build them, and then it's handed back to us for testing and acceptance."
MES functionality evolves in incremental steps at Roche, but careful steps are in order, as the MES ultimately will be the only source for all batch review of related GMP data.
"As far as the system architecture is concerned, each machine typically has older controls, or it is a little more process-oriented," explained Fretz. "We connect this to our corporate network through a firewall, which provides functionality for data and drives the MES clients, which are connected to the MES. Around MES, we have a collection of OPC and web servers and a data historian. This is collected to ERP. We also have LIMS, but we do not talk directly to the LIMS."
Data is interchanged between the ERP and the MES. Data from the MES clients are sent to the data historian, always attaching a batch context. "Then we can acquire it in the MES from the data historian, which allows us to do the batch report, where all data ends and we do the review," explained Fretz. "There is no paper, and all data is in one place for review."
After three years, compared to previous paper-based operation, Roche has seen a 95% reduction in errors related to the location of material and an 80% reduction of deviations related to incorrect material identification. "We expect, after we've rolled out the total solution, we'll reduce 90% of document errors caused by manual entry, and we would like to prevent actual errors before they happen by giving real-time quality alerts," said Fretz. "We also have performance improvements. We improved the way material moves from the warehouse to the shop floor."
Twenty percent of labor time was saved in the dispensing operations, and 50% of labor time was saved when compared to manual dispensing. "There also was an 80% reduction in the time required to review the dispensing documentation, and we expect a 50% reduction of production review time and an 80% reduction of QA review time," said Fretz. "We expect that, overall, two-thirds of the review time can be eliminated with the new solution."
Success with MES requires more than just a system, warned Fretz. "You need a technical setup and an organizational setup," he said.
The technical setup includes a prerequisite of electronic batch records and review of data acquisition from the shop floor. "Expect considerable effort to connect a diverse collection of already installed equipment," he cautioned. "Make sure the required product or site-specific changes are handled by configuration, not by program changes. And the way you create your procedure is important. Carefully design the structure of your procedure steps and expect significant effort to create and maintain them."
In the organizational setup, MES success is based on a thorough knowledge of production and business process knowledge. "Don't leave MES to the ‘techies,'" said Fretz. "Training and change management efforts are significant. Users will learn a lot about their own businesses. Have an MES champion on every site and in management."
OEE at Teva Parenteral Medicines
"There's always the pressure to do more or to do the same with less," said Duane W. Hiveley, manager, controls engineering, at Teva Parenteral Medicines. "Management is asking whether we really need new equipment or if different equipment can be used. There are many approaches to the idea of cost containment. The main thing is to make sure you have a simple approach on which to base performance."
Hiveley, who led the implementation of an overall equipment effectiveness (OEE) system at Teva, recommended asking yourself how well you really know your manufacturing line performance. How does downtime affect your profits? "It measurably affects your downtime in wasted labor and materials, lost production, reduced customer service and interruptions to other processes," he explained. "What can be done to unify common goals? You can't improve what you can't see, and you can't control what you can't measure."
OEE can be measured by looking at availability, performance and quality. "OEE is the simplest key performance indicator (KPI)," he said. "It measures how much is made that can be sold, vs. what could have been made. OEE software is not an HMI or SCADA application. It's good for general guidance and excellent for summarization, but it's not real-time data collection."
Implementing software that monitors manufacturing line equipment and provides an OEE and process reliability visualization tool is worth the investment, Hiveley said. Improving operational efficiencies targets line effectiveness and addresses the growing efforts to reduce costs and make a positive impact on the bottom line.
The implementation of line monitoring software is relatively simple. The biggest hurdles are the commitment to create manufacturing visibility and gaining the buy-in of the line operators. The collection of data and the translation of data into knowledge to make lasting process improvements is what OEE is about.
"We specified an OEE system, the Rockwell Automation FactoryTalk Metrics solution, in 2009 on a packaging line with high visibility and high utilization," explained Hiveley. "We needed the solution to be bolt-on, and we didn't want to add PLC code to get the data. We wanted it to be connected to the company intranet, and the HMI location was very important to us. There are limited operators on the line, and we wanted them to easily access the system so they would use it."
Teva chose FactoryTalk Metrics Server, PanelView, CompactLogix and two web-based PCs that were put on the line to create a high-profile implementation and to demonstrate how the OEE system could work throughout the company. "This took us one day to install, and it was very non-invasive," he said.
Latest from Home
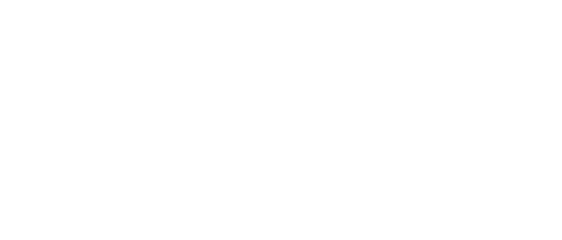
Leaders relevant to this article: