Now big-ticket items dont get much bigger than designing and building a new power plant. So any savings you can retain during a huge project such as this are no doubt more than welcome.
For instance, Duke Energy Corp. is in the process of building a new 800-mW plant in a rural section of south central North Carolina. To alleviate some of the new plants expenses, its been designed to include a whos who of fieldbus and Ethernet flavors. Even though this is a new facility, however, Dukes designers and engineers still had to a wrestle a bit with making the shift from designs relying on hardwiring to those making appropriate use of the new industrial networking methods.
Although fieldbuses and Ethernet have advantages over hardwiring, they require acceptance and a willingness to use them. Duke Energys Carl King discussed the cultural challenges involved in transitioning to unfamiliar technology.
Economically speaking, initial control system costs arent quite as much of a concern during new plant construction, but there are limits, and you much have desired capabilities, said King. So during installation, its important to reduce wiring and cabling needs and thereby lessen installation and checkout/startup labor requirements.
King reported that Dukes new plant requires networking that interfaces easily to other systems, provides high-level automation, has diagnostics capabilities, requires minimal operator interaction during normal operation, maintains situation-awareness during abnormal conditions, and provides operator warnings and appropriate, actionable options to return to normal operation when required control inputs are unavailable.
To start developing the new plants networking, King added that Dukes plant designers specified that all vendors and their sub-contractors use bus or Ethernet devices; created designs using these new methods; set up purchasing by forming alliances with suppliers that supported their goals; and developed installation and start-up procedures for their new network technologies.
Hardwired I/O is well understood, but it requires well-defined types and counts of I/O, needs segregation and system redundancy, is P&ID-based, has minimal diagnostics information, and is labor-intensive. Installing it requires lots of terminations, checkout and start-ups and higher material costs for cables, trays and other hardware, explained King. Now although fieldbuses and Ethernet have advantages over hardwiring, they require acceptance and a willingness to use them, a thorough understanding of their capabilities and limitations, and device counts and locations prior to implementation.
As a result, bus-based I/O points and devices demand more complex engineering due to fieldbuses electrical and communications limitations, such as devices per segment. They also require I/O segregation for system redundancy, as well as appropriate topology for the right spatial location of devices. Also, while less wiring, terminations and hardware with fieldbuses means less labor needed for installation, they still need more attention to network details prior to installation.
He continued, The good news is that fieldbuses and Ethernet give us more diagnostic information, but the bad news is that we need a way to make it useful. Unfortunately, some impediments to doing this have been separate engineering disciplines, ineffective interdisciplinary meetings and traditional construction and start-up groups. So we had specifications that werent fully developed for implementing buses, and also specifications for electrical, mechanical, and instrumentation and control that werent in sync with the overall design goal for buses.
In addition, during our department meetings, everybody said they didnt want to use a bus because their systems were critical. We had to confront them on why they didnt want to use fieldbus or Ethernet, and we found out that it was really because they just didnt understand them. Many people are still trying to do networking the old way, but they just cant anymore. So our approach now is to use bus technology or Ethernet where available and where it makes economic sense.
Dukes under-construction plant is implementing Foundation fieldbus, DeviceNet and Profibus. The Ethernet varieties being deployed include Modbus TCP/IP for most equipment interfaces and controls, EtherNet/IP for some small PLC packages, and DNP3 for its switchyard and switchgear interfaces and controls. King added that Dukes plant is even considering adding some wireless components, though hes found their response characteristics are slightly slower and battery life remains a concern. We might even use secure, handheld operator interfaces someday, said King.
Latest from Home
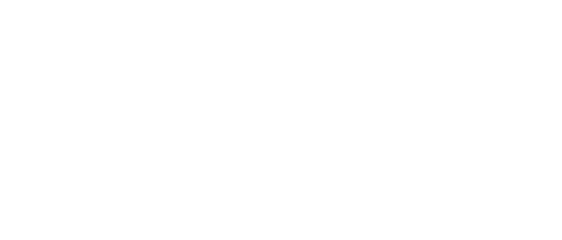
Leaders relevant to this article: