On display at ABB Automation World this week in Houston is a follow-on to the companys successful Navigator 600 silica analyzer product line: the new Navigator 600 phosphate analyzer. The analyzer provides accurate monitoring of a wide range of phosphate concentrations from 0-15 parts per million PO4 (0-5 ppm P) with a minimum range of 0-1 ppm PO4 (0-0.33 ppm P). The analyzer is available in single- or multistream configurations, enabling up to six process streams to be monitored sequentially. Chief markets for the instrument are expected to be the power generation industry and other large-scale steam- and water-dependent industrial applications where equilibrium phosphate treatment (EPT) or congruent phosphate treatment is used in conjunction with active pH measurement and treatment. EPT is a widely used water treatment method to reduce corrosion in high-pressure steam boiler tubes.
ABBs new Navigator 600 phosphate analyzer can measure up to six different process streams. Its compact design dramatically reduces reagent use as well.
Overfeeding of trisodium phosphate can lead to excess corrosion or boiler-tube failure, so it is critical to monitor this parameter, but previous analyzer generations have had issues with cost, complexity and maintenance.
The up-front cost issue is addressed by the analyzers capability to monitor up to six process streams simultaneously. In multistream operation, the analyzer can measure up to six independent flows, so a single six-stream analyzer can be used in place of six single-stream units, explained Steve Hammond, ABBs product manager for the Navigator series of analyzers.
Multiple streams can also be prioritized if desired. For example, the typical setup for a three-stream unit would be to measure in the order of 1,2,3,1,2,3. If stream 1 is a more critical stream, the monitor can be programmed to measure in the order 1,2,1,3,1,2,1,3, added Hammond.
A leading end-user concern with analyzers is the required maintenance, both in terms of cost and time. The analyzer uses one-fourth the reagents of units from other manufacturers, greatly reducing annual maintenance costs, Hammond said.
With the analyzers reduced demand for reagents, the yearly operating costs will be thousands of dollars less than with our older unit or with competitive units on the market, claimed Hammond. The analyzer also provides user-programmable continuous or sampled measurements, allowing a further reduction in reagent consumption in applications where phosphate concentrations are relatively constant.
Many analyzers require frequent hands-on attention from instrument techs, but not so the new ABB instrument. Our new analyzer features twice as many diagnostic messages as other units, including low-level reagent sensors, making it much easier to identify potential problems remotely, said Hammond.
An automatic cleaning function can clean the whole wet section periodically, preventing problems with drift due to fouled tubes. Remote monitoring and automatic cleaning allow the analyzer to operate for three months or more without manual intervention. Required annual maintenance to the pump tubing and capstan can be done in just two to three minutes, compared to 45 minutes required on some competing units, observed Hammond.
Another concern of analyzer users is the difficulty integrating analyzers into existing process automation systems, with non-standard interfaces being the chief culprit. ABB addresses this issue by providing the instrument with Ethernet communications via a standard RJ45 connector using the industry-standard protocols TCP/IP, FTP and HTTP.
The instrument is delivered with built-in web server capability. End users configure web pages and then connect the instrument to the Internet. Remote monitoring, configuration selection and data access can then be performed via any web browser.
ABB also claims ease of local operation as another key benefit. The instrument employs the new ABB Universal HMI with front-mounted push buttons that provide advanced, yet simple-to-navigate device interaction, Hammond said. Operation and commissioning is straightforward with menus presenting options for setting and fine-tuning parameters. Added support is provided by an extensive context-sensitive on-line help system.
The instrument has a choice of data display formats including chart, bar graph and digital indicator views. Historical logs provide operators with access to alarm, totalizer and audit trail data. Process data and historical logs are securely archived to a removable SD memory card with capacity of up to 2 GB.
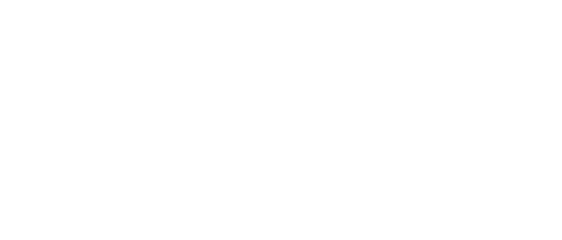
Leaders relevant to this article: