Also, listen to Walt Boyes talking to the 2008 inductees to the Process Automation Hall of Fame.
Trevathan Speaks His Mind
I see six primary trends in the future of automation:
- Technology advances. Automation technology is advancing at a faster rate today than in the past: digital communications in the control room and in the field; wireless; better control algorithms and the computing capability to implement them; better transmitters for more and more types of variables; batch management; alarm management; better process models and the computing power to implement them even in real time; safety requirements; security; better operator interfaces; better operator training; improved maintenance tools and practices; information integration with business systems, and many more. There is no one area that stands out to me, but the sum of all this is very powerful force for getting more benefits from automation.
- Focus on project benefits. There is increasing focus on getting real benefits from projects. Or stated another way, there is better analysis of the opportunities in the operation for improved benefits from controland the coupling of those opportunities to new control functions. That is not to say that without this strong a focus in the past we have implemented a lot of control projects that did not have benefits; my experience is that most control projects do have benefits, though without careful planning maybe not as many and not where you expect. However, as the project focuses more on the benefits, engineers are much more likely to design the project to deliver the greatest benefits; and the benefits you get will be much greater.
- Improved emphasis on project management tools and training. The state of project management capability has advanced significantly due to efforts of the Independent Project Analysis (IPA) Institute, the Construction Industry Institute (CII), and the Project Management Institute (PMI). The primary theme of these efforts is the concept of doing a thorough conceptual design before beginning detail designand then not changing any morethat is, a design freeze. In automation, the shift from work from being led by end users with contractors working on a cost-plus basis to lump sum work led by contractors with tight cost parameters is bringing more attention to the need for good project management and delivering better, lower-cost projects.
- Convergence of IT and automation. In general this trend is good, because it brings together the knowledge of the process and how to control it with the information, communication and presentation tools of IT. However, this IT focus can cause us to think of automation as just another programming task. Automation is not just about computer programming, and if the automation professional does not understand the process, control, information and operator needs and the technologies for dealing with them, we will solve the wrong problem.
- Increasing shortages of well-trained people entering the automation field. We know about the shortage of engineers in general, but the shortage of people entering automation is even more severe. In the U.S., making this better is critical to manufacturing competitiveness. This has been identified as a major focus area for ISA.
The need is to educate the thousands of new B.S. engineers needed each year in automation. While one or two good courses in control help, a new graduate entering automation really needs a number of automation courses replacing selected courses in conventional electrical or chemical engineering curricula.
That is to say, we need a real automation engineering curriculum. This would include courses that cover the critical areas of the full automation body of knowledge: instrumentation, control loop design, advanced control, discrete control, safety, visualization, industrial communications, security, database management, business system integration, and more. Controller tuning, the subject often emphasized in process control courses, is actually less important and detracts from coverage of more important material. - Increasing gap between the knowledge level of automation professionals and the technology. My observation is that most automation professionals are not keeping up with the advances in technology and in project tools. Most of us do not read the magazines we receive, do not listen to web seminars, do not read standards, and do not attend technical presentations. We get serious about training only for the devices we are assigned to program and do not understand the control task as well as we should. We take little responsibility for our own development; rather we want to leave it up to the company to educate us. We seem satisfied that thousands attend formal courses, become certified, attend technical meetings and participate in online discussion groups; but we forget about the tens of thousands who do very little of these things and who are struggling to do automation work without the necessary knowledge.
Automation is a great field for anyone interested in a technical career. Automation offers an unbeatable opportunity to grow and advance as fast as you are motivated to do so, to work for companies ranging from very small to very largeeven to start your own company, to move easily from theoretical to application work, hardware to software, office to plant, working mostly alone to working closely with a team, and from being a working technical engineer to working in project/personnel management. And the financial reward for good performers is very good. However, since it is still so difficult to learn much about automation in engineering schools and since most companies no longer offer extensive internal training like Monsanto did in the 1960s, it is a challenge to become well-trained. And you cant be good unless you are well-educated. In this environment, an automation professional needs to be a really good self-starter to master what he/she needs to know.
We need to be doing much more to show both high school and grade school students that engineering is a good career. In colleges, we need to make those already focused on engineering see automation as a choice of engineering profession. The best way to do this would be for schools to teach automation as a stand-alone engineering discipline; or at a minimum a defined option in electrical, chemical and mechanical engineering. There are more people needed in automation than in fiber, paper, optical and ceramic engineeringeach of which has an ABET- approved engineering program at one or more U.S. universities. A number of universities outside the U.S. teach automation engineering. Why so little emphasis in the U.S.? Lack of research funding and attention from industry is the usual answer. Schools lose money on each student and need research funding to offer new programs.
Of course, manufacturing in generalmaintenance, operations, as well as engineeringneeds a big boost as a career choice. In the U.S., two-year college programs in automation maintenance for both process and hybrid manufacturing cannot attract enough students to fill industrys needs. In many schools, the average age of entering students in over 25, meaning that the students have tried different jobs, including possibly getting a B.A. degree, before they decide to go into manufacturing, where the starting salary is often over $60k.
Dale Seborg Reminisces
How I got involved with Process Automation
When I was an undergraduate at the University of Wisconsin, I took an elective course in Fortran programming, one of few ChE students to do so during the early 1960s. I learned the joys and frustrations of having computer printout available only once per day, at the Athletic Departments indoor practice stadium where the campus computer was located. But this early experience whetted my appetite for computer applications.
In 1964 I wrote a computer program to analyze data from a new process control experiment at Wisconsin that concerned an identification method called pulse testing. To my great surprise, a modification of my software was still being using for this process control experiment, 30 years later! This experience and the required process control course at Wisconsin convinced me that I wanted to obtain a PhD working in the area of process control. Leon Lapidus new textbook, [ital] Digital Computation for Chemical Engineers, [ital] and faculty recommendations motivated me to apply to Princeton. I very much enjoyed the Princeton PhD program and began a long friendship with another graduate student, Tom Edgar (U. of Texas at Austin). Tom and I have co-authored a widely used process control textbook (with Duncan Mellichamp) and have presented related short courses in the U.S. and abroad. Tom was deservedly elected to the Automation Hall of Fame in 2007.
After graduating from Princeton in 1969, I accepted a faculty position at the University of Alberta. I had been planning on an industrial career, but the opportunity to actually apply advanced control techniques to pilot plants (that were interfaced to an IBM 1800 computer) was too tempting to pass up. Another key factor in my decision was that Alberta had two faculty members in process control, and was interested in hiring a third. It was, and still is, very unusual for an academic ChE department to have three faculty members in the area of process automation. My Alberta colleagues, Grant Fisher and Reg Wood, were excellent mentors,
especially concerning the practical aspects of process control and automation.
How I see my career in automation
I was very fortunate to receive my university education and start my professional career when the widespread use of computers and computer control was just getting started. Since the late 1960s, exciting and important developments have occurred in both process automation and control theory; it is evident that they have had a marked impact on industrial practice. Veteran readers of this magazine may recall that first generation of process control computers, as exemplified by the IBM 1800 and its TSX operating system. It had 32 KB RAM, a 1 MB hard drive with a random access time of 1 second. The RAM had two partitions, one for real-time applications and the other for background computations such as dynamic simulations. Clearly, the state-of-the-art in process automation has significantly advanced during the past 40 years!
Throughout my career, a key research objective has been to help bridge the acclaimed gap between control theory and industrial practice. In particular, I require my PhD students to do some experimental work as part of their PhD program. For most of my career, this experimental component has consisted of well-documented experimental applications of new automation techniques in academic settings. In recent years, the experimental studies have been conducted at industrial sites or at clinical medical facilities (e.g., glucose control strategies for type I diabetes).
By being involved with actual experimental and industrial applications, PhD students gain a better appreciation of the practical limitations and rewards of advanced control methods.
These types of research activities also tend to build character.
The most significant trends in process automation
Dramatic developments in information technology and the internet continue to spawn related developments in process automation. New opportunities will continue to be generated in so-called frontier areas of chemical engineering (e.g., biotechnology, nanotechnology, the environment, and especially energy) In the U.S., the increased emphasis on product development, as opposed to process development, will result in challenging process control and automation problems.
While the potential for improved process automation is very high, a key issue is who are the people who will develop and use them? The ranks of automation and process control specialists has been reduced by two key factors: the retirements of the large number of specialists who were hired in the 1960s, and the downsizing of engineering personnel in U.S. plants and the outsourcing of development effort to foreign countries. The net result has been a reduction of engineers in the process industries who are able to develop, or even apply, new automation strategies. Thus, it is becoming more imperative that new automation products be both bullet proof and capable of being readily used by non-specialists.
Another key manpower issue is that the ChE curriculum has broadened in recent years to include more material in new areas such as materials and biotechnology. Consequently, many new ChE faculty members have been hired in recent years who are not engineers. As a result, traditional ChE areas such as process control are under pressure and tend to be viewed less favorably in academia than they were a decade or two earlier.
Entering the field of automation now
Definitely, process automation continues to be a challenging and rewarding field; but the limited financial support available for graduate work in this area is a key limitation. Because process control is not a favorite area for federal funding agencies, the financial support for academic research will largely be due to mission-oriented research in frontier areas, and to research projects sponsored by one or more companies.
Bill Hawkins: The Man with the knack
How I fell into process automation
I was born with the knack, as Scott Adams puts it, and developed electrical and mechanical skills. Father worked for Foxboro from 1950 to 1977. He asked me to help him with the HVAC drawings for a quote on a SAGE center. I thought that was interesting, but space ships were more interesting. Fortunately, I did not have the grades from MIT to be accepted by NASA in 1960, so my father asked the chief instrument engineer at Hercules if there were any openings. I started at a Hercules blasting cap plant in upstate New York designing test instrumentation for commercial and small military explosive devices. I loved being able to design equipment to requirements and see the process through to use of the design.
I was transferred to Covington, Va., in 1965 where the equipment was very large scale. Again, the work was fascinating, and it led me to lunch with General Curtis LeMay in 1968, as the vice president of an equipment vendor. But my wife was not enjoying life, so we transferred to Home Office Engineering in Wilmington, Del.. My first field trip was to a plant that had a 60,000 SCFM compressor for a nitric acid process that was surging on a process trip. First we found an expansion sleeve plugging the vent silencer, using a big crane to get it down. Then we found the cause of the trips in a junction box under the stairs that had no cover, so nitric acid that formed in moisture rotted the connector. I was hooked, and loved the work.
My boss retired, and the new guy didnt see any need for developing our own instruments. Hercules was looking at computer control systems in 1979 and happened to be courted by the Rosemount Diogenes sales rep. I asked if they had any openings, after being impressed by the system, and started work in Minneapolis in January of 1980 as system engineering manager. I wasnt happy managing, but the next generation system project was just beginning. I became the control architect, with my 20 years of user experience. The RS3 system meant more to me than any space ship. We had a good run until Emerson acquired Fisher Controls. Our control philosophies were poles apartonline distributed configuration versus all configuration in a single relational database. We could not merge, so RS3 went under.
I started HLQ in July 1999, when the RS3 plant was sold and its people scattered to the winds. Fourteen of 165 people accepted transfers to Texas. I wasnt one of them, because the frigid winters kill every form of cockroach (but not mosquitoes). I found work in fieldbus through friends, and made some satisfying contributions.
Looking back on my career
A person with a knack for engineering needs a way to build satisfying things, usually with other peoples money. I was disappointed to not be able to build space ships, but process control really stretched my talents for electrical, electronic and mechanical engineering.
I was beginning to see repetition in the work at Hercules when I went to Rosemount, but I soon saw the variety in tackling problems from many different plants in many different countries. I was looking forward to improving RS3 in 1988 when the pending Fisher merger dried up the money for development. Fortunately, there were greater opportunities in ISA standards committees SP-50 and SP-88, where I could apply my experience to create new designs. In hindsight, standards committees offer the opportunity to associate with intelligent and lively people, but there is not the freedom to innovate that there can be in a company. Many hours are spent educating people that havent caught up, and when they do, more hours are spent in compromise. It takes the occasional bonding dinner to heal some of the compromise wounds.
It looks like I am a late bloomer, or as the Pennsylvania Dutch say, Too soon old, too late smart. But I have gone from being a shy engineer much better with things than people to someone more comfortable with people (engineers, not politicians). Writing a book was hard, but got easier as it came together.
Overall, there are things in my life that Id change, but my career isnt one of them.
Trends I see for the future of automation
There are people better qualified for future trend watching than this old man. There are some important historical trends, though.
The rise of the businessman focused on the bottom line has swung the social pendulum from keeping process engineering skills and knowledge in-house as valid company assets to outsourcing. The businessmen will run their course, and the pendulum will swing back to smaller, more agile companies with proprietary knowledge and loyal employees, if it swings back in time to avoid collapse.
Kurt Vonnegut wrote [ital] Player Piano [ital] in 1951, which followed a young automation engineer as he worked himself out of a jobwhen its all automated, engineers are no longer required. This has not happened 57 years later. The technology underlying automation keeps improving, making older efforts obsolete. The computer has accelerated this process, although some say it has encumbered it with unnecessary complexity. No problemcomplexity is job security.
The growth of technology has made specialization necessary. Our three-pound brains cant hold it all, so we have the problems of coordinating specialists. Communications become essential so that nothing serious is overlooked in the course of managing a project. The risk becomes that a project will not have a specialist that it needs, because no one recognizes the need for that specialty.
Getting new people into automation
The efforts of Dean Kamens FIRST Robotics organization to connect budding engineers in high school with experienced engineers are impressive. At the beginning of each year, high school teams and their mentors receive the details of the years competition game. The teams have just six weeks to design and build a 120-pound robot that could win the game. Everything is done to give everyone an equal chance and to insure cooperation among the teams, so that it doesnt become the win at any cost scene at most commercial sporting events.
The value of teaming a young person with a mentor is beyond my capability to describe. Students need to work on real problems controlling significant energies. Unfortunately, most of the places where such experience could be gained are off limits either because they are secret or the safety risks are too high. Then again, I dont know of any high schools with process control labs. But I think that a suitable student exposed to process control could get hooked on the ability to control great power.
Also, listen to Walt Boyes talking to the 2008 inductees to the Process Automation Hall of Fame.
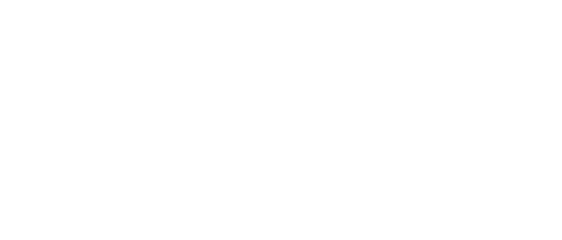
Leaders relevant to this article: