Why Go Online?
Process plants have been analyzing liquids and gasses and even solids for a long time, but much of this analysis has been performed in on-site labs. Since most process plants know how to analyze offline, why should major changes be made to go online?
“Real-time viscosity measurement improves our timing, therefore, we end up with less variation,” says Danny Cox, corporate process control supervisor at polyester resin maker AOC, Collierville, Tenn. Moving online and measuring viscosity at the reactors allowed technicians to cool the reactor and stop the reactions immediately once they hit a desired viscosity.
Dare County Water of Dare County, N.C., installed online free chlorine residual analyzers at remote pumping stations. “Unlike our prior offline analysis, we now have continuous monitoring of chlorine levels, alarming if chlorination equipment malfunctions and trending capabilities to monitor the effects of dosage changes,” reports Dare County Water utilities director Ken Flatt.
Moving analysis online yields real-time measurements and ultimately faster cycle times. “In real-time applications faster cycle times are essential to permit detection of small process deviations,” according to Steve Miller, the chief technology officer at Scott’s Specialty Gases, Plumsteadville, Pa.
Scott’s application is the low-level analysis of moisture in corrosive gases for the electronics industry. The company is evaluating a Tiger Optics analyzer configured specifically for this application. “Our objectives are to determine that the instrument is able to make an accurate, repeatable and traceable measurement of moisture at and below 1 part per million in a corrosive gas matrix. Once it is proven that the measurements meet our quality standards, we will move on to investigate the potential of the analyzer as online unit,” says Miller, adding, “For five months the analyzer has survived a steady diet of corrosive gases with no noticeable detrimental effects. The main benefit that we have observed in our testing thus far is that the wet-up (response to moisture with sample or cal gas)/dry-down (with dry purge gas) cycle times are three to five times faster than with other analyzer types. We attribute this benefit to the low wetted surface area of the analyzer afforded by the compact design of the cavity ring-down spectroscopy cell.
Online Measurements Versus Lab Measurements
|
Challenges of Going Online
“Pressure, level, flow and temperature are physical properties where accurate measurements are considered less difficult to achieve than the process measurements made by analyzers, which must determine the molecular composition of a process stream,” says Doug Simmers, worldwide combustion product line manager for the Rosemount Analytical Gas division of Emerson Process Management. “The chemical sensor of a process analyzer is often in direct contact with the process stream to provide accurate molecular composition readings, leaving the sensor unprotected from degradation. Process analyzers also tend to drift more in their readings than physical measurement transmitters because they provide measurements in the miniscule ppm range.”
Jason Kuzmiak, the BioTector product manager at Ohmart/VEGA, adds, “Analyzers must take samples that are often corrosive, volatile, oily and/or fatty into their sensing chamber. Their complexity often relates to pre-treating the samples to make them measurable within the sensing chamber. This complexity is even more pronounced when dealing with gas analysis.”
Another significant challenge is converting the analyzer’s output signal to a format recognizable by the control system. “When we moved our reactor viscosity measurement online, we had to covert the serial output from the analyzer to an OPC format in order to tie it to the control system,” says AOC’s Cox.
For some end users, the challenges are so great that they are forced to verify online measurements in the lab continually. “For dissolved oxygen analyzers, we have experience with every type of technology, and we have not found any satisfactory for reliability and accuracy,” says Philip Daniels, engineering supervisor at the King County Wastewater Treatment Division, Seattle.
“The dissolved oxygen process is not easy to monitor on a continuing basis without a lot of maintenance and continuous equipment attention,” he adds. “We make grab samples for the lab several times a day to verify the accuracy of the meters. We then basically use the online analyzers for relative control without real concern for the accuracy, only the short-term repeatability.”
The Scott’s Specialty Gases application for low-level analysis of moisture in corrosive gases for the electronics industry shows the difficulty of delivering samples for measurement. “Delivery of a representative sample of corrosive gas to the analyzer unit remains a challenge. We also need to provide independent verification of the moisture concentration reported by the analyzer in corrosive gas matrices,” reports Miller. “Our vendor, Tiger Optics, has worked closely with metrology institutes around the world so that the moisture concentration determined by their analyzers in an inert gas matrix seems to have been properly validated. But no such independent confirmation is available for pure corrosive gases, so validation must be done experimentally. The basic scientific principles of cavity ring-down spectroscopy are helpful in this regard in that moisture/matrix gas spectroscopic interactions appear to be less complicated,” he adds.
Online Analysis Challenges
|
How to Go Online
The first “must-do” when going online is to make sure that the analyzer can survive in the process stream. There are two areas of concern—the instrument itself and the probe. Make sure that the instrument is field-ready. The analyzer probe itself must be able to stand up long-term in your process stream.
This can be done in one of two ways. Either install a single analyzer and monitor its operation or speak with others who have successfully installed analyzers in similar applications.
Your instrument technicians will probably need to be trained by the supplier. The cost of this training should be factored into purchase decisions.
Analyzers typically need more maintenance than standard plant instruments. The analyzer should be equipped with an easy method of adding calibration gasses or liquids. Even the best probes will fail, so replacing probes should be straightforward and should not require an undue amount of time.
Buy analyzers that can be integrated into your existing control system without a lot of custom programming.
The interfaces most used in the lab are not the same as the ones used by process control systems, and problems can result. Converting an RS-232 serial output to a format recognizable by your control system can be an expensive proposition requiring custom software development, a situation best avoided if possible.
Finally, make sure that the online and real-time data delivered by the analyzer is used to improve control of your process. Moving a measurement online from the lab should yield more than just savings in lab costs. It should also deliver measurable improvements in process efficiency, up-time, and cycle time.
Best Practices for Going Online
|
Online Analysis Reaps Benefits
lanbia ingredients, Ballyragget, Ireland, manufactures a wide range of dairy products including whey, casein, cream and cheese. Waste from the individual plants feeds to an in-house wastewater treatment plant. Organics, nitrates and phosphates are removed, and clean water is discharged to the local river. The entire plant previously relied on grab samples and laboratory measurements to determine the level of waste from each of the process plants, the total loading to the bio-tower treatment plant and the success or failure of the treatment facility.
According to Eamon Ryan, the assistant manager services/environmental at Glanbia, the company installed seven online BioTector total organic carbon analyzers. They monitor the amount of waste product discharged from each of the process plants in order to facilitate the implementation of a waste minimization program. The analyzers also measure total organic loading to the treatment plant to ensure the plant operates within its designed specification and regulatory requirements for discharged water to the river.
CLICK HERE |
Using online analysis has reaped multiple benefits for Glanbia. “We saw a dramatic reduction in the amount of waste product discharged from each of the process plants, with some plants showing a reduction of up to 40% and a payback of less than three months,” reports Ryan. “We also saw a reduction in the loading to the treatment plant, thus ensuring the plant operated at its optimum level. This yielded reduced running costs and the total elimination of an odor problem which had been an issue for more than 17 years. By controlling the waste load to the treatment plant and operating within specifications, the final discharge regulatory requirements were easily achieved. There was also a reduction in CO2 emissions from the treatment plant in excess of 40%. Installation of the analyzers contributed to our ISO 14001 Award for environmental excellence.”
Glanbia had to overcome a general skepticism in the dairy industry that process analyzers could survive in an environment with high levels of fats and calcium, known to render ineffective even simpler devices such as flow meters.
Ryan concludes, “The food processing industry does not have the internal maintenance support structure of analyzer technicians more commonly available in heavier industries such as refineries and chemical plants. This was overcome because the analyzers operate without requiring regular and frequent internal maintenance support. We just have the analyzers serviced on a contract basis every six months by an outside supplier, and this is sufficient to yield an uptime of better than 99%.”
More Durable PH Sensors Save Millions
Rob Pastushak, senior technical/operational supervisor at Gilead Sciences’ Alberta, Canada, facility inspects a pH sensor.
Gilead Sciences is an international biopharmaceutical company headquartered in Foster City, Calif., that discovers, develops and commercializes innovative therapeutics. “The compounds we produce are used in various human applications from cancer treatments to anti-virals,” says Rob Pastushak, senior technical/operational supervisor at Gilead Sciences’ Alberta, Canada, facility.
To assure consistent product quality and maximize batch yields, the Alberta facility needed to improve pH measurement. “Our pH sensors could not hold up under the aggressive chemicals that we use such as hydrobromic acid. The organic solvent constituent caused the probe’s O-rings to degrade during the most critical point of the process. In many cases, three $600 probes would fail during just one batch,” says Pastushak.
Once the O-ring degraded, the pH probes no longer provided accurate readings, which presented another problem for Gilead. The process calls for two phases of crystallization, each of which requires pH measurement with tight tolerances. “Crystallization is critical, and pH is king. When the chemical composition of a drug falls outside of the correct pH range, quality and yield suffer because maximum crystallization fails to occur,” explains Pastushak.
Because of the unreliability of these devices, Gilead was forced to confirm pH measurements on a bench-top meter in the lab. “When you process 3,000 to 5,000 liters and add 5 to 10 kilos of caustic solution at a time, it might take 20 to 40 lab tests to ensure the pH is right,” continues Pastushak. “Going to the lab so often to confirm pH just killed production efficiency.”
To resolve the pH measurement issue, Pastushak researched several probes and decided to test a Foxboro 871PH sensor from the measurements and instruments division of Invensys Process Systems. “We found many vendors that offered quality sensors, but the Foxboro sensor’s polymer plastic construction was the only one that could stand up to all the reagents and solvents in our solutions. Foxboro also modified the sensors to include O-rings made out of Kalrez, a big factor in us choosing them over their competitors,” says Pastushak.
“We can now complete a pH adjustment in three hours rather than the 18 to 24 hours,” says Pastushak. “And we no longer have to take 40 samples to the lab to confirm accuracy—just one as a matter of quality-assurance protocol. Every time we grabbed a lab sample, we had to put the process on hold until we got the results back. This is significant when you consider not only the yield impact, but the cost of a process hour,” according to Pastushak. Reducing the number of confirmation measurements also improved personnel safety because technicians need to open the line to manually obtain samples.
Eliminating 40 grab samples allows Gilead to produce more batches in the same period of time. Online analysis has helped reduce manufacturing cycles by up to 20%. “Overall, yields have increased and cycle times have been shortened. When you add in the increase in quality, the improved pH readings by one sensor can be worth hundreds of thousands of dollars per year,” concludes Pastushak.
CLICK HERE to open an Excel Spreadsheet that illustrates the Glanbia Process Flow Representation.
Latest from Home
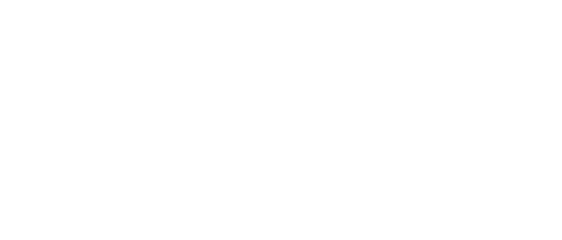
Leaders relevant to this article: