Its been more than 10 years since DCSs began to be forced from their proprietary shells by Microsoft-based software, other commercial off-the-shelf (COTS) computing technologies and emerging open-networking standards. However, even as many shunned the DCS labels connotation of big, old, slow, hardwired systems, developers responded buy making DCSs more flexible and scalable to smaller applications, just as IBM mainframes evolved into desktop PCs.
By seven or eight years ago, all the proprietary DCSs with their own hardware were dead, says Rick Pierro, president of Superior Controls Inc., a system integrator in Plaistow, N.H. Now, all the DCSs run on Dell PCs. Theyre set up like PLCs, and have dedicated controllers arranged on the backplane with I/O and network modules.
Evolution Revolution
From our perspective, the traditional DCS is a legacy technology thats been replaced by integrated digital automation architecture, which gives users improved project execution and timing, improves operational efficiency and up-time, helps them build safer plants, and enables smart plants with predictive technology, says Jane Lansing, marketing vice president for Emerson Process Management. Todays architecture is an open, interoperable, fully digital networking of intelligent components. The first-level computing platform is the field devices, which are digitally bussed with highly modular COTS-based automation systems, and the architecture features fully integrated asset health and management applications. Control and asset management integrated in the same architecture is the new world order.
In addition, after DCS control made so many of their applications safe, users began to ask how they could help optimize the processes they controlled. DCSs still provide essential functions for users whose processes must be available 24/7 for four or five years straight, they just run on PCs and laptops now. However, as long as gas can potentially blow up, users will need the high-availability control that only DCSs provide, says Tim Sweet, product marketing manager for Honeywells Experion Process Knowledge System (PKS) DCS platform. The big breakthrough for DCSs on PCs came in the mid-1990s when they started to ride Intels microprocessor power curve, and PCs really started to get data from the processes. Now, plant-floor and IT people are using the same gear, being made to work together, and learning to like each other to survive. IT guys now respect and trust that the plant-floor is segregated enough from business systems by the right firewalls. I dont get phone calls anymore from plant guys saying they cant work with IT.
Roy Tanner, product manager for ABBs 800xA (extended automation), adds that the scope of DCSs jobs descriptions have grown, and this has blurred their former boundaries. DCSs are using a lot more non-proprietary hardware and software, and this has allowed them to get into batch tracking, asset optimization, device management, and safety applications. 800xA even has pre-integrated software plug-ins, so our historian doesnt require users to redefine everything again when doing configurations.
Predictive diagnostics in Foundation fieldbus allow instruments to help improve maintenance efficiency via Asset Management System (AMS) Suite software at Shell Deer Park refinery.
Source: Emerson Process Management
To modernize and increase availability of its catalytic cracker (including a gas fractionization plant), selective hydrocracker, and other process units, Shell Deer Park refinery recently completed a five-year, $125-millon control renovation. This project included implementing Foundation fieldbus via Emersons PlantWeb digital plant architecture with DeltaV digital automation system to minimize production losses caused by unexpected equipment failures. After successfully testing DeltaV in 105 fieldbus instruments in its North Effluent Treater, Shell began implementing PlantWeb, DeltaV, and AMS Suite device manager software on 1,100 fieldbus devices in its cat cracker and gas fractionalizaton plants (See Figure 1).
AMS device manager receives diagnostic data from the control network, and makes it available for maintenance. The open architecture accepts any fieldbus-compliant devices, including our Rosemount pressure, flow, and temperature transmitters and Fieldvue digital valve positioners, says Roger Erfurdt, Shell Deer Parks control system manager. Process information is delivered to and from the controllers via the fieldbus communications protocol, while other systems are integrated by OPC, including the Triconex protective instrument/surge control system and vibration monitoring of 10 critical electric motors and steam turbines/expander turbines.
Using OPC to facilitate high-speed, two-way communications between the Triconex system and the control room is unique. Its never been done before, and it was accomplished here only after considerable effort. The OPC connection enables operators to view far more data from the Triconex protective system on the same monitors used for process control than in previous systems. The operators are also able to communicate with the Triconex system in case some action must be taken. This allows direct control over several large turbines and compressors through Triconex.
Erfurdt adds that Emersons personnel helped solve the OPC interface challenge by setting up a lab at their home facility to verify interoperability of the safety shutdown system, and identify issues that could affect system performance or operation. As a result, the refinerys modernization program is allowing Shell Deer park to operate its catalytic cracker at 100% of planned uptime or greater with no surprises and no unscheduled stoppages. The cracker now processes about 70,000 barrels of feedstock per day, and is expected to show an increase in utilization of at least 1%.
The availability of sound diagnostics from the field will enable our operators to have a better sense of whats going on in their processes, and make it easier for them to avoid upset conditions or at least minimize the effects of upsets, adds Erfurdt. If we can prevent the loss of three or four days of production in a year, this control modernization program will achieve its objective. We expect to be successful.
Mimics Go Mainstream
The long debate over whether combining other technologies can adequately recreate DCS capabilities is still going strong. Many developers and users claim that PLCs, HMI/SCADA software, a data historian, an OPC connection, and other components can be merged into systems that can do most if not all DCS jobs, and that traditional DCS functions are just a subset of these overall digital architectures. Weve installed more than 50 large-scale, high-end, batching systems with more than 500 I/O each over the past eight years. These were PLC and HMI based, and tied to relational databases to get directions, says Mark Hoffman, of Automation & Control Concepts Inc., a system integrator in St. Louis, Mo. None of these applications missed having DCSs at all.
However, other observers say these combined systems still arent integrated enough to provide true DCS availability. The real acid test is every year when you need to update your operating system (OS), add new functions, or remove software bugs, can you migrate your DCS from one to another version without shutting it down? If you truly need high availability, how can you add software patches and fix viruses? asks Sweet. Only a DCS can add a new OS and patches, and fix bugs without shutting down. High-availability has to be architected in. DCSs are built to add upgrades without going off process. Combined PLC/HMI-based displays typically start and stop every day or shift. Theyre still nibbling at DCS fringe, but it isnt happening.
New Regions, Greener Fields
DCSs also stay relevant because there are so many distributed geographic regions, such as India and China, where users are building plants that need high-availability controls. The big challenge there is how to deploy massive amounts of control in places where people are just learning the technology, says Sweet. We love working with engineering staffs in India because theyre inventive, aggressive, and they have the chance to make really big percentage gains in productivity, safety, and quality of life.
Solig Gas Powers new DCS system performs balance-of-plant control and links to a 126-megawatt GE PG9171E gas turbine.
Source: GE Energy
Networking and Wireless
The next big journey for DCSslike all other process-control devices and systemsis further into the Ethernet and wireless realms. This may be a familiar trip because DCSs and PLCs have long used fieldbuses to transmit I/O signals via twisted-pair wiring, and now use Ethernet to communicate to other devices and make graphics available via local area networks (LANs), virtual LANs (VLANS), and even wireless LANs (WLANs).
Just eight years ago, you needed an $18,000 proprietary gateway to make a Delta V DCS communicate with an Allen-Bradley PLC, but now you can do it with a $10 Ethernet gateway, says Superior Controls Pierro. Communication between different DCS and PLC packages and third-party devices also is simplified by OPC, which makes it easier to read register values for temperature, pressure and pH. Previously, we had to write costly and time-consuming I/O drivers. [See this months Industrial Networking cover story, "Multiple Choices," for Superiors implementation of a wireless-enabled DCS in a bioreactor application.]
Operators inaugurate the then-new central control room at Saudi Aramcos Shedgum Gas Plant in early 1998.
Source: Saudi Aramco
While the DCS industry as a whole has reached a degree of maturity, DCSs continue to evolve in some exciting and beneficial ways. These include greater field integration capabilities, increased functional distribution, and better integration with other plant- and enterprise-level systems, says Betty Naylor-McDevitt, Invensys systems marketing director. We believe that Invensys accelerated this trend with the recent introduction of the InFusion enterprise control system (ECS), which, while not itself a DCS, provides a common engineering, application, and information environment across all plant-level systems (DCS, PLC, ESD, CMMS, MES, etc.) regardless of vendor.
Honeywells Sweet adds that, It costs a lot to put a sensor into a plant of you have to drill holes, run wires, and do individual configurations. People are realizing that wireless doesnt just cost far less, but also allows them to put in many more sensors. This is like having a 10-bedroom house, and being able to have a thermostat in every room. For instance, though Honeywell recently announced a wireless version of Experion PKS, Sweet says it too will have to provide the same 24/7 availability and security that DCSs have always delivered. We just have to figure out in the lab how to make sure a wireless DCS never drops a critical message, and make sure that no one can hack it, adds Sweet. Then we have to adapt these methods for use in the field and get people comfortable using them there, though it may take a couple of years.
In short, while the d in DCS changed from meaning distributed to digital, it now covers both at a level of intelligence and networking capability undreamed of when DCSs were invented. You cant get much more distributed than making most of your process control decisions far out in the field itself.
DCS evolution is continuing on the path toward an integrated, open, interoperable infrastructure on which traditional DCS companies add value through their knowledge, support, and expertise. The reason for the slow progress is this change requires modifying DCS business models. So, its the business model, not the technology that is managing the transition to the next generation of open systems, says Ian Verhappen, industrial networks director for MTL Instrument Group. Once the hardware platform becomes based on industrial-grade, COTS technology with open standards, the added value of process knowledge/integration and long term support will be the differentiators and value adders. As hardware migrates to COTS, it also tends to become commoditized and a new category of supplier enters this area to concentrate on supplying the needs of the process control industry. For evidence of the open standards making this possible, you need look no further than the various communications organizations (Foundation fieldbus, Profibus, HART, OPC, etc.) and the ISA and IEC committees (ISA-50, 100, 99, 84 88, 95, 20, etc.).
The second trend is that DCS's are becoming more truly distributed by migrating more of the control capability to the field/fringes. An example of this is the preponderance of remote I/O (RIO). However, the point where DCS systems stop from a price/performance ratio, has been traditionally where the PLC has been selected to fill the void, adds Verhappen. Unfortunately, the PLC's heritage is that of factory automation and discrete control (Analog and PID algorithms are 10-15 years old) and they therefore have the paradigm entirely different from the DCS paradigm. Some suppliers have therefore been building hybrid control products to fill this gap.
In addition, DCSs also are useful for capturing the procedural expertise of soon-to or recently retired engineers. DCSs can formalize measurements, collected data based on them, and help provide consistent performance recommendations. This means users dont need to rely on tribal knowledge as much as they did in the past, adds Sweet. DCSs have evolved from using open-system technologies to working on PCs and onward to wireless. You cant call them dinosaurs.
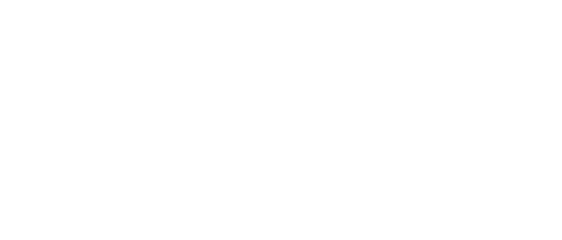
Leaders relevant to this article: