This is a terrible horrible no good very bad day at HUG. Why? Because there is too much to do. I hate concurrent sessions. Luckily for those of you who are receiving the
"electronic show daily" we're producing for HUG, there are more of us here than just me to cover this extremely information dense day. Control columnist, and Putman vice president of content, Keith Larson is here, along with Mark Rosenzweig and Paul Thomas from our sister publications Chemical Processing and Pharmaceutical Manufacturing respectively, and so we can cover multiple sessions from the User Group and Advisory Board Award Breakfast to the Refinery of the Future (as told by Mike Sarli of Exxon/Mobil) to the Experion Theater to...well you get the point.
There are concurrent sessions for HydroCarbon Processing; Metals, Mining and Minerals; Pulp, Paper, Printing and Continuous Web Solutions; Power Generation and Industrial Energy; Chemicals; Oil and Gas; Life Sciences and Consumer Goods; a fantastic pair of Lunch and Learns from Motiva and Cisco, and a whole afternoon full of Customer Interest Sessions.
This morning, I sat in on Mike Sarli's session, entitled, "A Refinery of the Future; the Role of Plant Automation." As usual, with a good paper, I took about 10 pages of notes, which I will provide a story from in this evening's electronic show daily edition of ControlGlobal eNews.
If you missed the show daily last night, you can catch it on the home page at ControlGlobal.com.
Sarli started by looking at the past, showing pictures of control systems from the 50s and later, and up to the 90s and this decade. Pointing to an old controller panel with painted on flow diagram, he noted, "That's why they called them 'panelmen' instead of operators."
He provided Exxon/Mobil's definition of the domain of plant automation: "All the hardware and software below the 'secure gateway' separating the plant from the business system, including:
--smart field devices
--DCS
--Advanced process control systems and optimization and modeling
software and systems
--Operator tools (the ASM stuff)
--Wireless worker tools."
"Everybody starts from a different place," he noted. Some plants still have pneumatic controls, analog controls, analog with digital enhancements, some are entirely fieldbus enabled, and some even have some wireless systems.
"The key word is 'remote,'" he said. "All of the productivity gains from these new systems are in the ability of an operator to work remotely to do calibration, diagnostics, loop checks, and so forth."
"I read somewhere," Sarli mused, "that one of the most valuable features of Foundation fieldbus is that a plant can be started up as much as five days faster with fieldbus. And we all know what five days' worth of output of a cat cracker is worth."
And we're going to be inundated with data from all these new data sources. "We have to understand what to do with all that data."
Sarli described the progression ExxonMobil has made from early "lump" models of APC through the development of MVCC (multivariable constraint control) models, to the much higher fidelity models of today, used for realtime optimization, with much wider scope, and which provide much better definition of the financial optimization of any process variable.
And on to the future...
"Refining is a commodity business. It just isn't possible to differentiate products anymore," Sarli said. "We are seeing strong cost pressure."
"We'll be making approximately the same products in 2020 we are making now, considering the lifecycle of the automobile. There will be lots of 2006 cars running strong in 2020, and we'll have to make gas for them just as now," Sarli said, "although there will be some shifting fuel slates."
There will be further environmental mandates.
There won't be as much new refinery construction as you'd think, he noted, because of the phenomenon he called "capacity creep." Refiners keep on getting more out of the refinery they have...sometimes as much as 100% more than rated capacity!
Workforce issues will not go away, Sarli said. "Half of the refinery managers I talk to say that the operators of the future will all be degreed chemical engineers with PhDs, and the other half think that operators of the future will look about like, and have the same skills as they do now." Demographics clearly indicate that there will be fewer operators to man existing posts.
Technology drivers include process technology drivers, and the accellerating pace of change in automation. Another big driver is the ability to use COTS (commercial off the shelf) hardware and software, "and that will drive the rate at which we deploy automation systems," he noted.
The real technology challenge is knowing what is coming...and above all, when. Sarli told the story of the Hubble telescope, which went into space so deeply flawed it could not be used, and while they were trying to figure out a hardware fix, the new developments in software and electronic imaging technology rescued the project, and even made the telescope better than its original specifications.
"We'd like to have modeling platforms with unlimited numbers of components, and computer speeds that enable us to take advantage of higher and higher precision models," Sarli dreamed. "We'd like to have operator tools that enhance the operator's ability to be vigilant and control the unit. These tools should give precise, contextual and vigorous advice...not half hour tutorials...and that provide model based advice for all time ranges (seconds, minutes, hours, shift, days, etc.)"
"What we are aiming for," he said, "is Continuous Constraint Busting. Refinery availability is in the low 90s. If you operate 'perfectly' you can perhaps reach another percent or two of increased availability. What we want to do is to give the operator a clear picture of the constraints he's operating under. We distill all the data we have down into what we call an 'operating window' and we tell the operator to do what he needs to do to keep the plant operating inside that window. We need to do more to empower and enable them to increase the operating window and increase the profitability of the plant shift on shift."
So where is ExxonMobil?
Sarli said ExxonMobil has deployed global security standards, global lifecycle management systems, global system life expectancy management ("We don't get rid of something just because it is old!"), global remote access down to the PLC level. We have a global MVCC deployment plan, and we've instituted global data visualization ("any engineer, any data, any time, any plant, anywhere-- as long as he has a laptop.").
Sarli said that Exxon/Mobil is in the process of deploying global applications engineering, standards and tools; global consistent product models; global RTO planning and scheduling tools; the next generation of operator tools; global monitoring at the console level; global wireless for automating operator rounds, and a next generation console.
"So here are Sarli's Simple Questions," he said.
--How do I make money with wireless and fieldbus? You gotta know what you want to with with it...make a business case. You can't sell technology to your boss.
--What's the next killer app, and how will I find it?
...and more importantly, how will I know when I do find it?
--How "open" is open? How "plug and play" is plug and play? Are we still the systems integrator?
--Does everybody know how to make money with automation? "Have I said 'make money' often enough?"
--How do I stay ahead of YOU?
And now for Sarli's Big Questions:
--do you have a vision for what your plant is going to become?
--can you define success?
--do you have a plan to design work processes and integrate enabling technology accordingly?
--what ARE we going to do with all that data?? Who sees it? Who shouldn't see it? How much data can send an operator into overload?
What do you want your shift teams doing? Should they be doing optimization, reduce variability, concentrate on equipement care, maintenance, or business issues? "Here's a hint," Sarli said, "all of the above is not the correct answer."
What does YOUR future look like? Everybody has a different starting point. It is not technology that drives the future but a valid business model. You need to have a vision, one that puts business first, and that is robust in dealing with the uncertainties of the future. You have to decompose that vision into action items, and carry them out, year after year. So you have to have intermediate milestones.
Sarli closed with, "Above all, don't fall into the technology trap!"
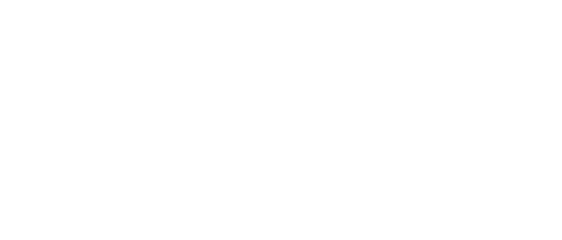
Leaders relevant to this article: