Finding ways to do more with less has transformed energy efficiency from a “green business” luxury to an operational necessity. All operations seek ways to increase energy and cost savings without hurting productivity.
Enclosures, housing the sophisticated, sensitive electronics and drives, protect them from the rugged environments and ambient conditions they are deployed in. It is imperative that these enclosures be cooled to ensure proper performance and avoid heat-related downtime.
Creating effective and energy-efficient climate control solutions for industrial applications consists of three key phases—design, installation, and operation.
The design phase
Does this application require cooling, and if so, how much? It is important to determine the correct amount of cooling to prevent energy from being wasted by cooling components to lower-than-needed temperatures or even by cooling components that might not need it at all. The necessary climate control solution for any application begins with three questions: how big is the enclosure? How much heat will be created by the installed equipment, and finally, where is the enclosure going to be located?
Selecting the right climate control solution
If the ambient temperature is less than the enclosure temperature, will NEMA 12 protection be required? If no, a louvered grill or roof vent may suffice. A filter fan or air-air heat exchanger should be installed if NEMA 12 protection is needed.
If the ambient temperature is higher than the enclosure temperature, more robust cooling methods may be employed. If chilled water is available at the site, an air-water heat exchanger will cool the components. Without chilled water, an air conditioning system and/or a chiller system plus an air-water heat exchanger should be considered. The following flowchart illustrates what products may be applicable to a given situation.
[sidebar id =1]
Determining the surface area of the enclosure
The surface area of the enclosure is where the heat will move into the enclosure or be dissipated. Since heat moves from hot to cold, the surface area determines the heat flow. Although you could determine the area using high school geometry, a formula takes into account the positioning of the enclosure, whether it is against a wall, free standing or among a suite of enclosures.
[sidebar id =2]
Calculate “Contained Heat”
With the surface area determined, you can calculate “contained heat.” For an existing, completed system, the temperature difference can be gauged by using the difference between the interior of the enclosure (Ti) and the surrounding exterior environment (Ta). When configuring a new system, those values can be found by totaling the heat loss from all installed components utilizing the information found on each data sheet.
Heat Calculation for a Previously Completed System
Qe = Qv – A × k × ΔT
Where:
- Qv is the amount of heat from the components inside the enclosure
- A is the effective surface area from the calculation above
- k is 5.5 w/m2 Celsius (sheet steel, different numbers for different materials)
- ΔT is the temperature difference Ta-Ti in Celsius
[javascriptSnippet]
After this calculation is completed and Qe, the amount of heat contained inside of the enclosure is determined, now the selection of the climate control solution can begin. Among the common solutions: filter fans, air-to-water heat exchangers, air conditioners or air-to-air heat exchangers, each has benefits and strengths based on its application. From an energy efficient standpoint, filter fans and air-to-air heat exchangers will use less energy, but require an ambient temperature below that of the desired internal temperature to be effective. If cooling to temperatures below the ambient air is needed, an air conditioner or air-to-water heat exchanger must be used.
The design phase, including the proper selection of a climate control device, maximizes the energy efficiency of an application. Correct installation and operation complete the steps for using less energy.
{pb}
The installation phase
When mounting components, including climate control, on or inside enclosures, adequate space for effective performance is critical.
In the course of plant operations, cables, spare parts, books or other objects left within the enclosure can block the airflow to the components. Improper climate regulation can cause a shortened lifespan of components or heat-related failures.
Installed components should be spaced no less than 8” away from the air generated by the climate control products. The fans on the components should not face the climate control fans, the blowing and battling air may cause a short circuit.
Climate control units outside the enclosure should have a clearance of 8-16” from possible air blocking obstructions. Enclosures and cooling units should be placed away from any heat sources which could cause excessive heating or possible damage.
When a climate control solution has been selected, correct installation on the enclosure is imperative for proper operation. It is normally recommended that filter fans be placed at the bottom of the enclosure with the corresponding exhaust filter installed at the top of the opposite side. Air conditioners and heat exchangers can be mounted either on the walls or roof of an enclosure. Unless otherwise required by the demands of an application, best results are achieved by installing the cooling system per manufacturer’s instructions.
[sidebar id =3]
With your climate control selections installed and your enclosure components installed, the ongoing process of assured efficiency is just beginning.
Operation phase
Maintaining the selected units over the course of their service life will keep performance levels up and energy usage down. Each climate control solution will provide maximum efficiency by following maintenance guidelines.
Filter fans and air conditioners
The filter media for fans is relatively simple to maintain, because it is usually possible with a visual inspection to determine if they are clean, dirty or need replacing. Although a simple maintenance step, it will add to heat stress and component inefficiency if not routinely performed.
Air conditioners require slightly more maintenance. A rudimentary understanding of how air conditioners operate illustrates their maintenance checkpoints.
Air conditioners have a hot and cold side, the cold side facing the internal area to be cooled. Both sides are lined with copper coils, the condenser coil externally and the evaporator coil internally. Refrigerant passes through these coils and transfers the head from the inside of the enclosure to the outside. Fans circulate the air treated by the coils dispersing the air to its needed direction. If these coils become blocked or clogged with contaminants, the airflow is reduced, lowering the unit’s efficiency, making it work harder, using more energy and reducing the cooling output.
To prevent the condenser coil from becoming clogged, the coil can be treated with a protective substance like Rittal’s RiNano coating, to prevent oil, dirt and other contaminants from adhering. Filters are designed to prevent particulates from reaching the coils. If a filter is used, it should be designed for the environment: metal filters for oily atmospheres, lint filters for fiber filled air or foam filters, effective for exceptionally dusty environs. Appropriate cleaning ad replacement frequency will depend on the conditions at the installation.
Both fans and air conditioners will produce consistently high levels of performance and efficiency with general required maintenance.
Air-to-water heat exchangers
Air-to-water heat exchangers can be used in harsher environments than filter fans and can cool components inside an enclosure to temperatures below ambient conditions, like air conditioners. They operate with a chilled water supply which runs through a coil in the heat exchanger. An internal fan blows air across the coil. Heat is transferred from the inside of the enclosure o the water, which absorbs it and then carries it to the chiller, where the water is cooled and recirculated.
Air-to-water heat exchangers require very little energy to operate and are a low-maintenance and highly efficient climate control solution. They do require a chilled water supply, which may be readily available in some industrial factories. Industrial chiller systems are generally large in scale and vital to plant operations. The piping system the chiller itself should be insulated and not exposed to excessive heat.
The three-step solution to efficient energy cooling control
Attaining effective and energy-efficient climate control solutions for industrial applications covers three fundamental steps: design, installation, and operation.
In the design period, the overall panel layout, heat calculations, and climate control selection should be completed. Determining the amount of cooling needed and the type of environment in which the enclosure will be deployed will be crucial factors in selecting the type and size of cooling solution that will deliver both performance and efficiency. Recommended checkpoint: Ensure adequate airflow within the enclosure without obstructions when laying out the panel.
The design phase will dictate much of the installation plan. Attention to detail and proper installation of the climate control system and the components in accordance with the design plan and manufacturer’s recommendations will improve the effectiveness. Recommended checkpoint: Check for proper enclosure seals and other potential trouble spots to eliminate leakage in the system.
Once operational, climate control devices and other components should be monitored for performance and a regular maintenance schedule performed. Recommended checkpoint: Establish a day-one efficiency level log for a baseline gauge of energy consumption and to note any changes in desired operating levels.
Pursuing savings and efficiency in cooling can reduce one of the largest expenditures in many installations. Whether a new system is being configured, or an existing system is being evaluated, following the steps to the highest level of enclosure, climate control energy efficiency will improve your bottom line.
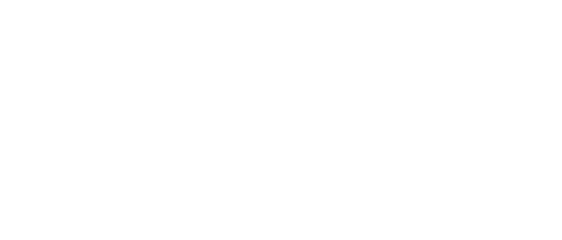
Leaders relevant to this article: