Automation enables a circular economy for plastic recycling
This problem is difficult to solve because there are few scalable methods for using plastic trash as a feedstock. Recycling should be an obvious solution since most people are willing to use the colored or divided bins we see everywhere. However, barely 10% of plastic trash is recycled. It’s constrained by the variety of plastics in use, and because most recycling approaches only work on a few types of plastics. For example, polypropylene doesn’t mix with polyethylene, so most recycling approaches require sorting trash to isolate individual types.
Still, recycling can play a major role on the road to decarbonization, and there are methods beginning to take hold on a small scale. The long-term solution is to create a circular economy around plastics, but what does this involve?
The accompanying diagram illustrates the linear lifecycle flow of single-use plastics and similar products. This chain is effective and even optimized to a large extent when looking at individual steps. But each step has its own energy input and its own waste stream, making a linear arrangement ultimately inefficient.
The green arrows on top illustrate the current role of recycling, which is beginning to make a significant contribution, but this methodology alone will never eliminate energy and waste because the entire linear supply chain must be rearranged to become circular. Recycling will continue to be a major element, but the total amount of energy-in and waste-out can be significantly reduced.
What is a circular economy?
When looking at the diagram, imagine taking the “dispose” end of the linear lifecycle flow, pulling it around, and grafting it to the line between “extract raw materials” and “design and manufacture.” This is the ultimate realization of recycling because energy can pass from one step to the next, with less overall waste compared to the linear approach.
The flow is circular when:
• Waste is reintegrated into new products;
• Energy is recovered and retained from one step to the next;
• Additional energy comes from renewable sources as needed; and
• Products are designed and manufactured to apply these concepts.
Waste takes many forms, but in this situation, we’re referring to the mountains of water bottles, plastic bags, take-home food containers and other plastics found in landfills. There’s also waste from manufacturing processes in the form of water, underutilized feedstocks and unrecovered energy, to name a few sources. Curbing waste requires acts of foresight. Operators must look for ways to reduce waste, rather than simply paying for it in the form of lower product yields, disposal fees and regulatory burdens. Processes must be redesigned to make incorporating recycled materials easier, with less energy-intensive processes.
Plastic waste recycling also takes many forms. The most obvious is mechanical recycling, where sorted waste is cleaned and melted for reuse for the same purposes. Advanced recycling approaches use depolymerization or dissolution, a solvent process starting with sorted waste, to accomplish something similar. Mixed plastics can be subjected to pyrolysis, driving them down to base hydrocarbons suitable for use as renewable fuels or feedstock for virgin plastic manufacturing. Therefore, multiple practical alternatives exist, and some can be used simultaneously.
Energy is wasted in many manufacturing facilities because it’s considered too costly to recover, but this view is shortsighted. If energy is lost in one phase of a process, it must be replaced and paid for in the next, increasing carbon emissions. When all these factors are considered, the cost of recovering lost energy and reducing carbon footprint may not be as expensive or impractical as originally thought.
Companies that adopt waste minimization strategies, and convert to renewable feedstocks and recycled materials, realize a true sustainability advantage in the form of economic, environmental and social benefits. Advantages include reductions in energy and water use, carbon emissions and waste.
But this is the real world
Some readers might respond, “All these new methods sound very noble, but they call for substantial changes.” Fortunately, many digitalization tools are available to make these steps possible and practical. They begin by making changes from the bottom up, beginning with instrumentation and control to providing the data necessary to close the gaps. For example, it isn’t possible to manage and optimize energy use if it isn’t measured with required levels of detail.
So, let’s apply these concepts to the circular plastic economy. Here’s how digitalization provides value through energy and other savings at steps through the plastics value chain:
Feedstock production—Optimize production of polymer feedstocks, including optimal blending of recyclate to minimize emissions and waste. Improve reliability to avoid unplanned incidents that waste energy and feedstock.
Polymer production—Optimize material and energy balances across unit operations, while improving internal recycling of material and heat to reduce waste.
Advanced recycling—Improve advanced recycling processes to maximize reuse of material, and to capture and track use of post-consumer resin to support certification.
Waste collection—Optimize the supply chain to improve the capture, processing and reintegration of post-consumer waste into production.
Recyclate upgrading—Optimize and assess the quality of post-treated recyclate to improve downstream use in feedstock or polymer production.
Throughout circularity—Mitigate project risk and improve safety management with improved data management and analysis.
It’s a long and challenging list, but it doesn’t all have to be done at once. It’s possible to make incremental advances, with each project resulting in measurable improvements. Achieving a true circular economy in any industry calls for a holistic view. Companies that undertake this approach find the further they move into the process, the more complex the choices become, but the positive effects are greater as synergies come into play.
Companies launching comprehensive waste-minimization programs experience measurable successes in market share, revenue growth and cost savings. With information available through digital platforms, they can speed up decision-making for process selection and upgrades based on rigorous technical and economic data. They can then allocate resources with better visibility. That’s what we need in the long term to create a true circular economy.
Don Fregelette is the vice-president of chemical industry marketing at Emerson, overseeing the company’s global chemical and sustainability business. His team develops and delivers solutions across the entire industry, with an emphasis on sustainability, digital transformation and safety. He holds a BS degree in Chemical Engineering from the University of Buffalo, and an MBA degree in Engineering/Industrial Management from the Rochester Institute of Technology.
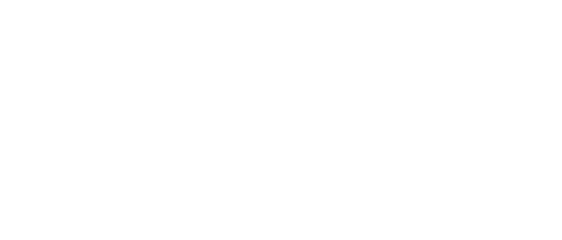
Leaders relevant to this article: