Factoring life cycle variables helps make intelligent motor-drive purchases
Early electric motors were operated at one speed, guided by available current and voltage and often drive belt and pulley systems that mechanically controlled system speed and power. As motors evolved, efficiency improved, mostly by changing output control from mechanical to electrical and eventually leading to the creation of modern adjustable speed drives (AC drives).
Today, the largest potential for electric motor energy savings lies in system- and process-level optimization. Many different measures can be taken to improve the performance of processes and systems, but AC drives have the most important role to play. System-level optimization is possible thanks to several key elements in AC drive technology:
- Motor independence: Drives that are independent from control systems and motor type provide options when selecting the motor technology (induction, permanent magnet or high-efficiency synchronous reluctance) and motor manufacturer that best suits an application to ensure peak performance and optimized energy consumption.
- The open availability of efficiency data (also in part-load conditions) is also key. This data can be used to optimize system design. Tools to calculate energy efficiency are continuously being developed.
- The use of energy-optimized motor control is essential to harvest the efficiency potential of electric motors and to ensure the drive is always perfectly adapted to the attached motor and changing loads.
Fans and pumps are key targets for efficiency improvements.
Energy efficiency is often embraced as a way to save resources and save money. It could be thought of as a “first fuel.” Energy efficiency savings throughout the system are realized by a decrease in energy or fuel at the system input. An important aspect of motor-control systems or AC drives is the power consumption required to perform a given task. Energy has an assigned cost and reduction in energy use or increased efficiency can result in operational savings.Though traditional return on investment analysis may evaluate these systems, other approaches such as total cost of operation (TCO) looks at expenses across the life of the system including energy, downtime, maintenance and repair, wear and replacement and disposal costs. There are often technological low-hanging fruit, such as the installation of AC drives, but purchase decisions still warrant a cost benefit analysis that factors total life cycle costs. All relevant factors should be evaluated including negative collateral effects that stack up against advantages.
When discussing efficiency, it is important to remember that a drive should be used to optimize the performance of a motor. Any drive can control the speed of a motor, but not all drives can get the best efficiency out of a motor.
For higher efficiency the focus should be on advanced drive control. By accessing key operating parameters, such as maximum torque per ampere, advanced drive controls reduce power consumption and improve performance of the system.
- Hardware features built into the drive (such as DC chokes) result in a more efficient system. This built-in functionality also reduces costs and eliminates the installation space required for external components.
- Intelligent heat management is another target of system-level optimization. Features such as back-channel cooling and availability of liquid-cooled drives result in significantly reduced heat loads in switchrooms. This enables the use of small air conditioning systems to optimize space requirements, improve efficiency and drive down costs.
It is important to distinguish between motor, controllers and drives. A motor is the mechanical or electrical device that generates the rotational or linear force used to power a machine. It converts electrical energy to mechanical energy. There are mainly three types of electric motor:
- DC motors are historically the first type of widely used motor. System (motor and drive) initial costs tend to be less.
- AC synchronous: The rotation of the rotor is synchronized with the frequency of the supply current and is ideal for driving equipment at a constant speed and for use in high precision positioning.
- AC induction (asynchronous): The most common type of AC motor in industry, which uses electromagnetic induction to generate torque.
Cranes used worldwide can benefit from high-efficiency control systems and motor independence.
Motor-drive system selection often reaches a critical juncture when deciding between relying on prepackaged motor-drive systems or creating a custom solution that fine-tunes the motor, drive, controller and feedback components to fit a specific application. While prepackaged motor-drive combinations provide a single point of purchase, be aware that in the long term they can become costly in breakdown and retrofit situations.All motor-drive combinations have advantages and drawbacks. Initial cost, power consumption, serviceability and life cycle costs are some factors to consider. Motor independence means you can select any combination of suppliers to achieve maximum motor performance. Drives that can adapt to different motors yield positive factors that influence TCO. These factors include:
- Flexible logistics: The ability to accommodate changing customer specifications and new technological trends over the entire lifetime of the application.
- Quick changeover: A change to an alternative supplier or alternative motor technology is often the best solution.
- Freedom from supplier dependency: Over the lifetime of a motor-driven application, special and non-standard motor dimensions can limit maintenance efficiency. When faced with multiple installations there is an advantage to having the same motor-independent drives installed throughout the entire plant. There is a lessened spare parts inventory, simplified staff training and more straightforward maintenance.
- A future-proof solution: Using automatic motor adaptation, motor-independent drives can deliver optimal performance of any motor both now and throughout the lifetime of the application. Motor-independent drive suppliers continually test new motor technologies in order to develop new algorithms for compatibility. Independently optimized components adapt completely to a variety of applications. OEMs, for example, can therefore design the highest-performance drive and motor system for a niche application.
Choosing the right motor and drive combination doesn’t have to be a complicated, stressful task. Once the ideal motor for an application has been sourced from a trusted supplier, there’s no reason to make any changes to that scenario. However, some changes are possible, changes that will provide more options, reduce potential downtime, simplify maintenance and lower life cycle costs, simply by choosing a motor-independent AC drive.
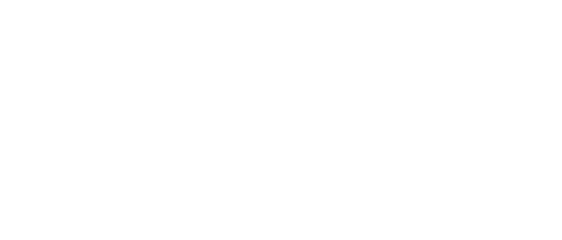
Leaders relevant to this article: