By Loren K. Jones, Contributing Writer“FASTER, FASTER, you fool, you fool!” Those immortal words from comedian Bill Cosby seem to have been the mantra for industry since the beginning of the industrial revolution, and nothing I’ve seen indicates that it is going to change any time soon. From Henry Ford’s first assembly lines to today’s advanced robotic arm, automation has been a drive for speed. After all, as the old saying goes, “Time is Money.”Industry is fighting for time, driving to get as much production per hour as it can. It’s simple economics. Plants cost money, so each plant needs to produce as much as it can. The people who run the machines cost money, so each person needs to produce as fast as he or she can. Running a plant at or above what the engineers say is the designed capacity can boost profits and save the cost of building a new facility. All of that boils down to the “Faster, Faster” desires of management.In the not so distant past, the only way to control the speed of manufacturing lines was mechanically. New gearboxes. Different sized pulleys and belts. Different sized drive rolls. The drawback of those methods was precision. The precise size of pulley required might not be available, so the closest available was used. Matching speeds on a high-speed manufacturing line can be as crucial as the speed itself. A speed mismatch can result in the process being slowed down or production lost due to damage from the machines. Unfortunately, these methods were just about the only way to do it. Across-the-line AC motor starters didn’t offer any speed control, and although the early DC motors and drives weren’t right for many applications, they were the only game in town.Early DC motor controls offered industry the ability to regulate the speed of manufacturing lines without retooling the plant. Manual rheostat controls gave operators the ability to tweak the process, but had the drawback that some rube could lean on them and mess everything up. The advent of computer controls, especially the development of the programmable logic controller (PLC), eliminated the rheostats.The PLC gave companies the ability to control their new drives with far more accuracy. The development of the gated SCR drive gave industry the needed ability to match, change, tune and fiddle with the speeds of their lines. Gone was the need for complex calculations on pulley size and gear ratio. If a roll was wearing and the speed was off a little, just boost the drive a bit. If timing was an issue, speed this one up and slow that one down and the bottleneck is just a memory. The problem was that the drives were big. Whole cabinets and even rooms full of cabinets were devoted to the drives. Of course, there was also the maintenance problem.Having been in the field for the last twenty years, I’ve worked on those big drives. The SCRs were subject to failures that cost hours a week to fix. The venerable Reliance MaxPack and CardPack drives were my introduction to this aspect of process control. I could probably still strip and replace all 12 SCRs in one of those drives in less than an hour.The brushes in the DC motors were also an issue. They had to be checked regularly, replaced often, and the list of things that could potentially damage the commutater, either directly or through chemical interaction with the copper and electricity, is too numerous to list.In the last ten to fifteen years, that has all changed. The emergence of variable frequency AC (VFAC) drives has resulted in changes throughout the industry. DC, the standard by which all others are measured, is rapidly becoming a thing of the past. VFAC drives (See Figure 1) offer the same benefits without many of the drawbacks that plagued DC. In DC, exceeding the motor’s rated speed was difficult, involving field weakening and a resultant loss of torque.
FIGURE 1: VFAC IN CHAINS
This Reliance model SP5005 hp VFAC controls a chain conveyor. Source: James Hardie Industries
Small AC drives can perform many tasks. This 5 hp Baldor VFAC drive controls a batching screw. Source: James Hardie Industries
Allen-Bradley Kinetix 1394 Digital Servo Controllers with SERCOS modules control servo-driven belt conveyors. Source: James Hardie Industries
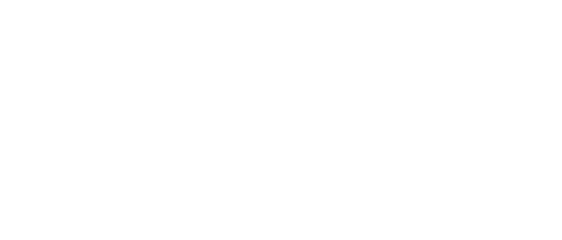
Leaders relevant to this article: