A few months after start-up, our facility needed to add an alternative purge medium for a process vessel. Along with a flow loop, we needed a couple trios of new double-block-and-bleed actuated valves in a spot about 90 feet from grade. So did we need to run nine twisted pairs (or more—up to 20 for conventional on-off valves) all the way down to grade? We found we could just extend an existing fieldbus segment from an instrument at that level—so maybe 25 feet of light conduit on a platform were needed instead of 100 feet of 2-in. down the side of a structure.
Why hadn't we done this from the start? Our original "chicken foot" network was grafting eight toes on one of its toes.
In recent issues, we've explored how bus technologies create new challenges for end users' Engineer, Procure, Construct (EPC) consultants and systems integrators. Bus technologies provide a standardized infrastructure, allowing smart devices to integrate happily with the host DCS and one another. End users want this because they see a path to improved control, process availability and risk/asset management. But for the EPCs, it's disruptive.
Bus topology—the ability of multiple devices to share the same two conductors on a network or "segment"—is one of the disruptive forces. We have deployed networks elsewhere, so why would fieldbus cause consternation?
The challenge is this: process plants have hundreds or thousands of devices distributed to scores or hundreds (or more) segments. In the point-to-point world, there is a one-to-one relationship between device, single-pair cable, multi-pair cable "pair," field JB terminals, marshalling terminals, scatter wire, all the way to the I/O processor terminations, so much so that the whole process can be largely automated. Designers and engineers work from a database, whose fields then populate loop drawing templates, junction box drawings and termination schedules.
With fieldbus, all the one-to-one relations of the old world are scrambled: devices can have multiple roles; home-run cables can serve as few as two devices or as many as 32; and the rules for grouping devices are anything but random and can be crucial to a successful project. Tools do exist, such as Intergraph's SmartPlant INTools CAD products, but they require a new level of training and effort that was previously unimportant or automated. So have some compassion for your EPC and simplify.
For your first fieldbus job, consider a simple "chicken foot" or "star" topology. By standardizing on six segments (~72 devices) per field junction box, your install will look and feel close to conventional, but you'll be running some bigger conduits and raceways. It will look just like conventional point-to-point from the JB to the field. If a certain device needs to move from segment "A" to segment "B" late in the job, there's an increased chance they'll be in the same JB. While less optimal for the project in the CAPEX phase, the strategy lends itself well to future expansion. In this scenario, the client can still add to the installed "chicken foot" as every fieldbus node can become an "expansion point" for future additions.
Users with great confidence in their segment loading and their team's fieldbus savvy may choose what many consider an "optimum" topology, what I call the "mutant" chicken foot. Spurs—"toes" if you will—grow on the trunk wherever needed. The trunk strings these clusters together as a single pair, so conduit size is minimized. If local codes allow, using "basket trays" can be more forgiving for late changes and future modifications. Physical layer suppliers such as Pepperl+Fuchs, Relcom, Turck and Phoenix Contact have some nice modular hardware to accommodate these multi-drop hybrid schemes. Every project will have its unique mix of experience and confidence on both the client and consultant sides. Making discrete topology choices in light of your team's strengths and challenges can help ensure a smoother and less stressful journey.
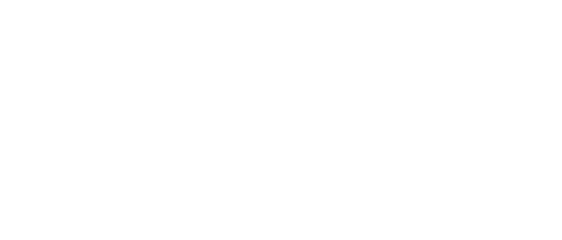
Leaders relevant to this article: