If your process plant is like most, the reliability focus is misplaced. Many process plants spend lots of time and money making sure that their HMIs, controllers and I/O are reliable and often redundant. The networks connecting these components are often also redundant, and many are constantly monitored to forestall failures.Ā However, most automation system hardware failures don't take place in the control room or remote field-installed I/O points, but rather in field devices, namely valves and instruments.
"Our data shows that equipment failure is the number one contributor to downtime," says Laura Briggs, product manager at Emerson Process Management. "Thirty to fifty percent of downtime is attributable to equipment problems, while the other 50-70% is due to operator error, process upsets, natural hazards and unknown causes" adds Briggs.
From an automation professional's point of view, the process equipment contributing most to downtime are instruments and valves. It follows that more time and money should be spent on improving their reliability as opposed to relatively dependable control room components such as HMIs, controllers and I/O.
It used to be much easier to monitor the health of control room components than field devices. Field devices were much harder to monitor as most were connected to the control room via discrete and/or analog hardwired connections. Without a digital link to field devices, remote monitoring wasn't possible, and these devices were therefore often neglected.
Hence, easily monitored control room components with relatively low failure rates were closely watched, while much less reliable field devices were overlooked. But, smart valves and instruments linked to the control room via high-speed digital networks mean it's possible to closely monitor their health.
For many plants, the first step has already been taken, namely upgrading to smart field devices and fieldbus networks.
However, this first step doesn't deliver maximum benefit until it's coupled with an asset management system (AMS) that can continuously monitor the health of selected field devices. Deploying the right AMS in a well-engineered installation allows plants to predict field device failures and take steps to forestall problems that can lead to downtime.
"In general, about 70% percent of instruments and valves and 50% of mechanical equipment should be monitored online. By following these guidelines, plants can predict how long critical equipment may be operated before repair or replacement is necessary. Operating experience shows these types of predictive maintenance programs workāimproving quality, throughput and availabilityāwhile reducing costs," notes Briggs.
"One of our customers had an alert that exposed a drive gain issue on a critical mass flowmeter measuring catalyst slurry," adds Briggs. "The alert was investigated using the AMS, and the diagnostics indicated a partial plug of a sensor tube. The problem was corrected by having production operators back flush the flowmeter sensor tubes to clear the blockage. This type of problem, if it hadn't been discovered by the AMS, could have led to a $25,000/hour process disruption."
Another Emerson customer achieved 99% availability of field devices, in part due to the predictive diagnostics provided by the AMS. "Our customer has been alerted to torn actuator membranes and to incorrect calibration of their mass flowmeters. These data alerts have allowed the plant to correct these and other problems in a proactive manner and prevent downtime," concludes Briggs.
Proven hardware and AMS software are readily available to constantly monitor the health of your valves and instruments. Refocusing reliability efforts on these field assets will yield higher relative returns than dollars spent on improving the reliability of control room components.
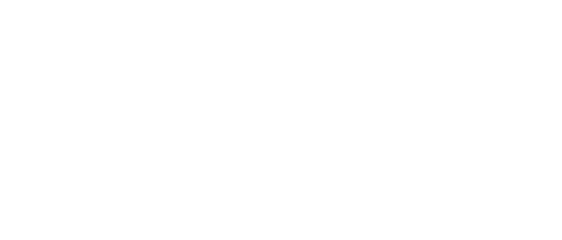
Leaders relevant to this article: