Q: I am a process engineer working for an engineering firm. I have a question about sizing for the body of a control valve. Is it mandatory that control valve body size shall be not less than the half of the upstream nominal line size? If yes, why?
The case I face is that the upstream line size is 3 in., and as per the control valve calculation, a pressure control valve of body size of 1 in. (full port) fullfills the requirements for proper Cv. Is this selection is correct, or do I have to go up to 1.5-in. control valve body size as a minimum?
Jussef Aly
[email protected]
A: From a control point of view there is no such requirement. If the pressure drop is high, the required valve size can be much smaller than the pipe. In this case, it can be 1 in. Do not oversize the valve just because the pipe is large! Naturally, if there are other, non-control considerations, such as the physical strength of the valve to stand up to pipe strain or the plugging nature of the process fluid, you have to consider them. In such cases, you can consider the use of reduced port sizes or low Cv valve designs.
If there are no such non-control considerations, and the pipe is well aligned and supported, the 1-in. valve is OK.
Béla Lipták
[email protected]
A: Go with the most accurate valve-sizing formula, regardless of the pipe size, as long as the pipe is larger than the valve. Valve sizing is critical to effective control. Oversizing of piping is common and principally affects the cost of the installation, but oversizing a valve may result in poor control, low rangeability and seat wear which leads eventually to complete loss of control.
Greg Shinskey
Process Control Consultant
North Sandwich, NH 03259
A: I know of no code reason that a control valve of one size may not be attached to a pipe of a much larger size, assuming they are of the same pipe schedule. Consider the case of a control valve being attached to the side of a tanka very large pipe indeed. This is something that is done frequently.
Attaching a small valve to a large pipe or tank, however, introduces a pressure change immediately past the change in flow cross-section. There is a flow head loss (and possibly a state change) associated with this that may need to be taken into consideration. Its effect will be to require a somewhat larger valve.
In the case at hand, one would question why the pipe feeding the control valve is so much larger than indicated by the size and flow through the control valve. Once one is satisfied that sound reasons underlie the situation, and no error has been made in the flow and valve calculations, including entry losses, any concerns about size mismatch may be dismissed.
Otto Muller-Girard, PE, FISA.
A: One very serious problem is around the strength of the small valve body. Unless special care is observed in the support and piping alignment of the piping, there is an increased probability of the 1-in. valve breaking. I would investigate the use of reduced trim for a larger valve body. My opinion is that this is one reason that the manufacturers make reduced trim available.
Cullen Langford,
Consultant
[email protected]
A: To my knowledge there is no regulation stating that the body size of a control valve shall not be equal or less than the line size, but the statement is a good rule of thumb. There are two cases to evaluate:
- Liquid stream
- Gas or steam stream.
Liquid streamIn case the body size is half the line size, the output velocity from the valve is four times the velocity in the pipe. In general, if the pipe is correctly sized, the resulting output velocity is in excess of what is generally accepted (say 6-7m/s). Hence, the standard way is to use a body size that causes the output velocity to be acceptable, and then to use a reduced trim to have the correct Cv. Another important aspect to consider is the possibility of cavitation or flashing that imposes a larger body size to reduce damages to the valve and maybe a different kind of trim, which could have a different Cv with the same nominal size.
Gas or steam streamThe considerations about liquid flow apply again, plus the fact that depressurization increases the volume of the downstream stream as compared to the upstream one. The effect is that the higher the pressure drop is compared to the absolute pressure, the higher becomes the volume and the velocity at downstream pressure. The overall effect is that the outlet velocity can be well over four times the inlet velocity.
When selecting a control valve, not only the Cv is to be taken into account, but also other parameters, like the outlet velocity from the control valve and the type of trim to be chosen.
All the above considerations do not take into account the noise problem. That has a contractual impact, but is also a parameter to be considered, as a noisy valve is a stressed valve that could have a short life unless used rarely.
Dr. Alberto Rohr,
Italy
Q: Thank you for your work on the ISAs Instrument Engineers Handbook (IEH)! Your work has undoubtedly increased the respectability of the I&C profession by establishing a basis for standardizationnot to mention transcending as a common reference for instrumentation and electrical engineers and designers.
With this in mind, a new phase in instrumentation has begun: the evolution governing the integration of digital networks and the dynamic, ever-blurring lines between the domains of instrumentation and controls vs. information technology. My personal experience has been in adopting a recent project which manages the design end of a boiler installation using fieldbus for the first time. One design question raised is whether to go Ethernet or Modbus in communicating to the H1\HSE-to-DCS link. The domain of Ethernet is viewed by IT professionals as their sole domain. Can you offer any opinion in your experience other than to read the business best seller, Who Moved My Cheese? (tongue-in-cheek of course). Second, does the H1 qualify as an instrument or FTA (Honeywell TDC3000)? FYI this is a DeltaV application.
Im sure the future will continue to blur lines of distinction between IT, EE and I&C. In part because of your work, IEH has made the understanding of a formerly complex and esoteric subject more available to professionals of similar disciplines.
R. Scott Krejci
[email protected]
A: Modbus TCP, if supported, might be an option or you might compromise on OPC. The third volume of my handbook deals with these issues, but because changes occur fast, and suppliers are striving for captive markets, it is hard to keep up with what is going on in print.
I think ISA could serve a role in giving guidance in such matters and in leading the way towards international standardization of digital communications in process control.
Below, you will find a couple of comments from experienced colleagues.
Béla Lipták
[email protected]
A: Modbus is a serial port device. [It is] very slow. If the problem is with IT department. your organization needs to solve that organizationally.
John Gerry
President, ExperTune Inc.
[email protected]
A: The question that needs to be answered is the speed of communications, and since this system has already settled on the DeltaV as the control platform, use of HSE has been ruled out, though H1 is supported. In addition, field devices do not communicate via HSEat least not yet. Therefore, the only solution available from these choices for this platform is Modbus as a third-party interface. The questioner did not mention OPC, though OPC is not yet well-suited for real-time, closed-loop control.
Peer-to-peer communication at the SCADA layer should be Ethernet-based for network bandwidth, so my suggestion is to see if Modbus TCP is supported.
Ian Verhappen
Director ICE-Pros Inc.
[email protected]
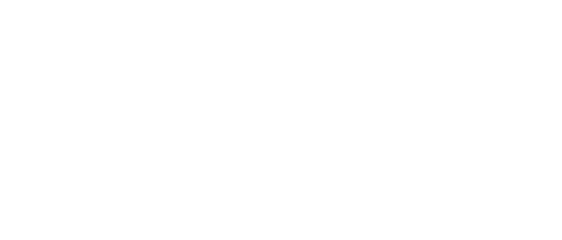
Leaders relevant to this article: