In the search for the most appropriate control valve, gain and stability are as crucial as any other selection characteristics. The gain of any device is its output divided by its input. The characteristic range and gain of control valves are interrelated. The gain of a linear valve is constant. This gain (Gv) is the maximum flow divided by the valve stroke in percentage (Fmax/100 %).
Most control loops are tuned for quarter-amplitude damping. This amount of damping (reduction in the amplitude of succeeding peaks of the oscillation of the controlled variable) is obtained by adjusting the controller gain (Gc = 100/%PB) until the total loop gain (the product of the gains of all the control loop components) reaches 0.5 (see Figure 1 below).
RELATED ARTICLES
>>How to select control valves, Part 1
>>How to select control valves, Part 2
The gains of a linear controller (Gv = plain proportional) and a linear transmitter (if it is a temperature transmitter, its gain is Gs = 100%/°F) are both constant. Therefore, if the process gain (Gp = °F/GPM) is also constant, a linear valve is needed to maintain the total loop gain at 0.5 (Gv = 0.5/GvGcGs = constant, meaning linear).
If the transmitter is nonlinear, such as in the case of a d/p cell (sensor gain increases with flow), one can correct for that nonlinearity by using a nonlinear valve whose gain drops with flow increases (quick opening). In case of heat transfer over a fixed area, the efficiency of heat transfer (process gain Gp) drops as the amount of heat to be transferred rises. To compensate for this nonlinearity (drop in process gain = Gp), the valve gain (Gv) must increase with load. Therefore, an equal-percentage valve should be selected for all heat-transfer temperature control applications.
FIGURE 1: WELL-TUNED LOOPS
In a properly tuned loop, the decay ratio of the oscillation amplitude is constant at 0.25. Such decay ratio (¼) is obtained if the product of the component gains (the total loop gain) is constant at 0.5.
In case of flow control, one effective way of keeping the valve gain (Gv) perfectly constant is to replace the control valve with a linear cascade slave flow control loop. The limitation of this cascade configuration (in addition to its higher cost) is that if the controlled process is faster than the flow loop, cycling will occur. This is because the slave in any cascade system must be faster than its master. The only way to overcome this cycling is to slow down (detune) the master by lowering its gain (increasing its proportional band), which in turn degrades its control quality. Therefore, this approach should only be considered on slow or secondary temperature control loops.
Positioning Positioners
A valve positioner is a high-gain (0.5% to 10% proportional band), sensitive, proportional-only, valve-stroke position controller. Its set point is the control signal from the controller. The main purpose of having a positioner is to guarantee that the valve does in fact move to the position that corresponds to the value of the controller output.
The addition of a positioner can correct for such maintenance related effects as variations in packing friction due to dirt buildup, corrosion or lack of lubrication; variations in the dynamic forces of the process; or nonlinearity in the valve actuator. In addition, the positioner can allow for split-ranging the controller signal between valves, or can increase the actuator speed or actuator thrust by increasing the pressure and/or volume of the actuator air signal. In addition, it can modify the valve characteristics by the use of cams or function generators.
A positioner will improve performance on most slow loops, such as the control of analytical properties, temperature, liquid level, blending, and large-volume gas flow. A controlled process can be considered “slow” if its period of oscillation is three or more times the period of oscillation of the positioned valve.
Positioners also are useful to overcome the “dead band” of the valve, which can be caused by valve-stem friction. The result of this friction is that whenever the direction of the control signal is reversed, the stem remains in its last position until the dead band is exceeded. Positioners will eliminate this limit cycle by closing a loop around the valve actuator. Integrating processes, such as liquid level, volume (as in digital blending), weight (not weight-rate), and gas-pressure control loops are prone to limit cycling and will usually benefit from the use of positioners.
In the case of fast loops (fast flow, liquid pressure, small-volume gas pressure), positioners are likely to degrade loop response and cause limit cycling, because the positioner (a cascade slave) is not faster than the speed at which its set point (the control signal) can change. A controlled process is considered “fast” if its period of oscillation is less than three times that of the positioned valve.
Split ranging of control valves does not necessarily require the use of positioners, because one can also split-range the valves through the use of different spring ranges in the valve actuators.
If the need is only to increase the speed or the thrust of the actuator, it is sufficient to install an air volume booster or a pressure amplifier relay, instead of using a positioner. If the goal is to modify the valve characteristics on fast processes, this should not be done by the use of positioners, but by installing dividing or multiplying relays in the controller output.
Smarter Smart Valves
Much improvement has occurred and more is expected in the design of intelligent and self-diagnosing positioners and control valves. The detection and correction for the wearing of the trim, hysteresis caused by packing friction, air leakage in the actuator, and changes in valve characteristics can all be automated. If the proper intelligence is provided, the valve can compare its own behavior with its past performance and when the same conditions result in different valve openings, it can conclude, for example, that its packing is not properly lubricated, or the valve port is getting plugged. In such cases, the valve can automatically request and schedule its own maintenance.
A traditional valve positioner serves only the purpose of keeping the valve at the opening that corresponds to the control signal. Digital positioners can also collect and analyze valve-position data, valve operating characteristicsand performance trends and can enable diagnostics of the entire valve assembly. The control signals into smart positioners can be analog (4-20 mA) or digital (via bus systems). The advantages of digital positioners relative to their analog counterparts include increased accuracy (0.1% to 1% versus 0.3%-2% for analog), improved stability (about 0.1% compared to 0.175%), and wider range (up to 50:1 compared to 10:1).
Smart valves should also be able to measure their own inlet, outlet and vena contracta pressures, flowing temperature, valve opening (stem position) and actuator air pressure. Valve performance monitoring includes the detection of “zero” position and span of travel, actuator air pressure versus stem travel, and the ability to compare these against their values when the valve was new. Major deviations from the “desired” characteristic can be an indication of the valve stuffing box being too tight, a corroded valve stem or a damaged actuator spring.
Additional features offered by smart valves include the monitoring of packing box or bellows leakage by “sniffing” (using miniaturized chemical detectors), checking seat leakage by measuring the generated sound frequency, or by comparing the controller output signal at “low flow” with the output when the valve was new. Another important feature of digital positioners is their ability to alter the inherent characteristics of the valve.
Valves Serve as FlowmetersA control valve can also be viewed as variable area flow meter. Therefore, smart valves can measure their own flow by solving their valve-sizing equation. For example, in case of turbulent liquid flow applications, where the valve capacity coefficient Cv can be calculated as
PICKING THE RIGHT CONTROL VALVE
When it comes to selecting and sizing control valves, this unique and completely non-commercial valve selection chart not only helps you pick the right control valve for the job, but also serves as a fantastic reference tool you can download!
CLICK HERE to open an enlarged pdf version for easy viewing chart, or click the Download Now button at the end of this article to save the chart for future reference.
About the Author |
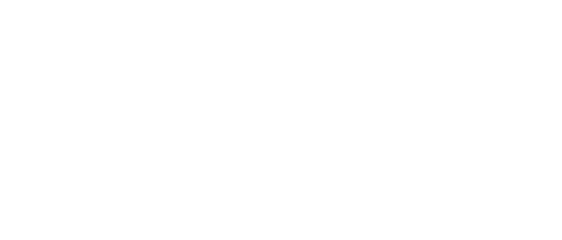
Leaders relevant to this article: