WE HAVE a tempered water system supplying cooling and heating to an exothermic reactor. We are using a Cascade/Split range control method. The Master controller is for the Reactor Temperature, the Slave is for the Tempered Water Temperature. The slave outputs goes to a splitter, which then controls the steam valve and water valve for the tempered water.
The diagram below is a typical split range control for example: a tempered water system. The water temperature is the PV for the PID. A typical splitter would be 0-49% for cooling, and 51-100% for heating (with steam). In some applications, another option is to shift the split point if the heating process gain is higher than that of cooling (different strengths in the valves). For example a 0-32% for cooling, 34-100% for heating split.
Is this an acceptable method of control? What is wrong with it?
David Rolfe
ANSWERS:
THE NORMAL configuration is to use an =%, fail closed steam valve with a positioner that operates it between 50-100% of the output signal from the reverse acting slave PID set at 10-20% proportional band and a little integral. The water valve is also =%, it fails open and it operates between 0-50% of the output signal from the reverse acting slave PID. In order to prevent reset windup in the master, we also provide the master TIC with external reset from the slave transmitter output.In your existing configuration, I do not see the need for the splitter, as the positioners fulfill that function. In the proposed new configuration, I dont see the need for inserting dead band at the PID (particularly not such large one as +- 5 degrees F), because the dead band can be provided by setting the positioner ranges 0-49% and 51-100%.
Because the gain, time constant and deadtime of the process is different during cooling from that which exist during heating, it is reasonable to modify the tuning constants when switching from cooling to heating, but 1) most of the integral and derivative changes have to be done in the Master and 2) I would not adjust the gain in two separate slave PIDs, but in the same one. This is because if you have integral in the positional algorithm of the slave controller, the internal reference would be lost at the time of switching.
I will also ask some other colleagues about your question.
I AGREE with your assessment of the proposed system. The dead zone inserted between the two slave controllers will cause cycling in the primary loop. Additionally, the bias introduced into the set points will cause offset if external reset feedback is applied.
There is usually no conflict in a batch reactor control system between PID settings for heating and cooling, because heating only brings the primary temperature up to set point, where cooling takes over. Therefore the cascade system should be tuned for cooling, and this usually gives acceptable results for heating.
Where this is not the case, separate PID settings can be scheduled into the slave controller, depending on which valve is open. This is easy to do with digital controllers, and is a standard feature in some controllers (e.g., Foxboro).
Greg Shinskey
I HAVE
seen dual PID controllers used for pH control where there was an acid and base reagent. Unfortunately the difference between the set points needed to keep the controllers from fighting and insuring both valve are not open at the same time is highly dependent upon the dynamics and tuning of each PID. So I prefer a single split ranged controller with its tuning scheduled per the valve throttled as you mentioned. So far as the split range point, operators expect 50% but a different point may help compensate for the difference in process and valve gains if the controller gain cannot be scheduled. Since the process dead time and time constant is also different for heating and cooling, the integral time will also be different but if mostly proportional action is used for the slave controller, it may not need to be scheduled.I favor the use of the splitter in the DCS configuration instead of split ranged analog positioners because it eliminates special positioner calibrations. This was particularly important in the days of pneumatic positioners. However, if the positioner is digital, smart, and has its calibration accessible from the control room, the accuracy and maintainability of split ranging in the field is no longer as much an issue. It is especially important that the valves do not have a deadband or stick-slip as the trim goes into and out of the seat that is greater than half of the split range gap. The deadband and stick-slip cited for many valves is at the ideal throttle position of 50% and does not show the effect of the extra friction from seats and seals at shutoff.
It is also important that each control valve not be oversized and that the master controller not get the slave controller unnecessarily traversing the split range point. For set point changes to the master controller and startup, I favor a feedforward signal of the set point change added to the master controller output and a head start initialization of the slave controller output to preposition the proper valve.
Greg McMillan
EXCESSIVE
complexity serves little purpose. Some years ago, I used to look after a bunch of PVC polymerizers, and spent too many sleepless nights trying to tweak the control system for maximum production. A highly exothermic reaction using a water-jacketed reactor and direct injection steam/cooling water. The aim was to bring the batch up to temperature as fast as possible, and then switch to cooling as the exotherm cut in, so that there was minimal (or no) overshoot detectable in the batch temperature.The best design I devised had P-I-Derivative on PV control on the primary, P-I on the secondary and an override P on the secondary (external feedback) to prevent the jacket temperature exceeding 95C and sending steam to the cooling-water return. Split range on the cooling-water and on the steam using the positioners, with a 5% deadband between them. This provided the balance between the two gains the batch ran at maximum steam until the jacket temperature reached 95-96C (a bare thermal element in the cooling-water outlet for speed of response), then the derivative response on the primary cut in about 5C below setpoint to drive the secondary to full cooling, and then recover as the batch reached setpoint. With an exothermic reaction, the system doesnt need heating again until the end of the reaction.
Ian H. Gibson, Process, Controls and Safety Consultant, Melbourne, Australia
OF COURSE
, it's not normal practice to put in 2 PID controllers. As such there is freedom to have both heating and cooling occurring at the same time, which is energy inefficient and does not improve control.The split block implementation is common in most DCS systems. That way, the output of the PID and the positioners can be set separately. The valve setup can set to fail open or fail close and be set to 0-100% as in any other application. Makes it easy for maintenance and reinstallation if necessary. The split allows conversion of the 0-50% of the PID to be converted to 0-100% for the one valve and 50-100% of the PID to 100-0% for the other valve (or vice versa). It also allows to gap or overlap the valve outputs if desired (overlap, again wasteful and gap doesn't often help but insets some additional deadtime. But certainly logic to change tuning constants is needed because of the different process characteristic between the zone..
Alternately, as he as stated, I have done 0-32% of the PID go to one valve and 32-100 to the other. What you are trying to do with that is linearize 2 separate valve characteristics into 1 heating region in order to have a single set of PID tuning constants. That is often tough to do as it is assumed that both cooling and heating are linear in their respective regions and that the valve positioner is also, which is often not the case.
The biggest problem in exothermic reactors is the large amount of heat needed to initiate the exotherm and then to immediately remove the heat when the reaction start to take place. Most PIDs can't keep up with the result of bad temp control.
Bruce Jensen, Yokogawa Corporation of America
I AGREE
with your and Greg answer about the use of a single controller, not dual to prevent fighting. I have used splitting in the DCS because I used I/P converter an pneumatic positioner (hot service, and decoupling in the installation activity of a new power station). This way there are two analogue outputs from the DCS and any tuning is carried out only at the DCS engineering workstation, without involving different people.The actual solution depends from the hardware available.
Alberto Rohr, Italy
Need an Expert Opinion? |
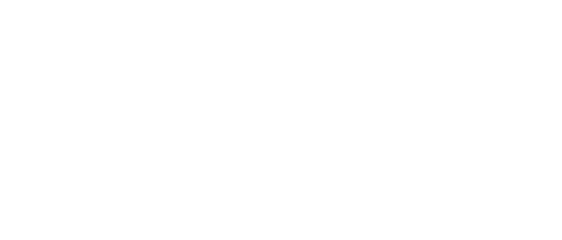
Leaders relevant to this article: