I AM to teach a course shortly in which I have been asked to include something on variable speed pump control. So I have been looking very carefully at IEH Vol 3, Section 8.23. If I can be so presumptious as to question the "old master," I have serious problems with the control scheme for two variable speed pumps serving multiple users, utilizing valve position control.
My problem originates with the fact that the pump-system curves at the top of Figure 8.23pp shows a single "system curve." Actually, I believe the system curve varies, depending upon the demand being made by the non-selected users.
Consider the "minimum system curve" to be when all users valves are at 90% -- this presents the minimum restriction to flow.
Consider the "maximum system curve" to be when the user with the smallest control valve has the valve at 90% open, and all control valves are closed. This presents the maximum restriction to flow.
A "typical operating system curve" lies between these two extremes, and varies, depending upon that the demands are of all the users. A typical operating system curve may not even span the capacity of one pump, therefore it would be impossible to switch back from two pumps to one pump at 90% of flow capacity of one pump. I believe that you can only switch number of pumps based upon speed. If one pump is in operation and you reach its maximum speed, then start the second pump. If two pumps are in operation and you reach an (arbitrary setting) minimum speed point, then stop the second pump.
In either case, you need a feedforward signal to avoid bumping the discharge pressure. Since the feedforward signal can be either positive or negative, depending upon whether you are going from one-to-two pumps, or from two-to-one pump, the circuitry has to be a bit more complex that is shown in your diagrams.
In the figures below I describe what I think is a workable control system. If you have time (I envision your spending every waking hour getting out IEH Vol 4), I would appreciate your comments, and corrections if any of my concepts are in error.
FIGURE 1: PUMP AND SYSTEM CURVES
True, the extremes that I mentioned would probably not be encountered in actual practice. But I still believe a typical system curve would lie somewhere in between these extremes.
It appears to me that the scheme for stopping a pump on flow control would provided the actual (typical operation) system curve is not too far from what I have defined as "minimum" system curve, but might fail if there is more variation. The scheme for both starting and stopping a pump based upon speed seems (on paper analysis) to be more tolerant of wider variations in the actual system curve.
I will be interested in reading Shinskey's article on external feedback. Foxboro (I/A series) and Honeywell (TDC 3000 and successor systems) do external reset differently, since Foxboro uses position algorithms and Honeywell uses velocity algorithms. My own research and simulation studies show that the Honeywell system can have problems under some circumstances, whereas the Foxboro system does not experience those problems.
By Harold L. Wade, Ph.D., Wade Associates
ANSWERS:
GOOD TO hear from you and thanks for the excellent question/comment, but calling me an old master gave me mixed feelings. You should see me racing the grandchildren (five of them) up the rope-ladder to the tree-house! By the way, I have all kinds of respect for todays parents for controlling the process of child upbringing, but fortunately, the topic we are talking about here (pump control) is much simpler: FIGURE 2: MULTIPLE PUMP, MULTIPLE USER CONTROL SYSTEMPart of the reason is that, while in my article (for illustration purposes) I have shown a 100% friction process, in fact, no such process exists, because all processes include some static head or elevation also. In fact, I have used the illustrated control scheme for decades, without problems. I believe, the reasons for my luck (in spite of being theoretically questionable) are the following:
First, cooling loads in most continuous processes tend to change slowly and properly sized control valves tend to move in the same direction with the ambient. The second reason is, that I never consider all the control valves when selecting the most open one for VPC measurements. This, from a practical point of view, is important, because you dont want a large pumping station to respond to the opening of an insignificant 1 valve. In other words, we select those valves for consideration, which are of similar (large) size and importance. Consequently, by this selection process, one makes sure that it is not possible for all valves to be closed, while a small one is 90% open. (In other words, this is not a totally democratic control scheme, the votes of only the critical valves are considered.)
You are absolutely correct, that when changing the number of pumps in operation, you have to feedforward the new speed (x or y), and select it right away, in order to avoid bumping the supply pressure to the process. This is the purpose of PY-03 in my figure, as we switch from one to two pump operation, because it is important not to temporarily overpressure the system. As to the transfer function you show to accomplish this same goal, in some applications it might be necessary to adjust Ts as a function of load.
When switching from 2 to 1 pump operation, if under-pressuring the system for a few seconds is acceptable, I have allowed the supply pressure to drop a bit, until PC-01 brings it back up. In that connection, you are absolutely right that if the process can not tolerate a short pressure dip either, a y signal is also needed.
The importance of the role of external reset in preventing reset windup in cascade loops was already explained by Greg Shinskey in connection with Q3, so I will not repeat it, but would recommend it that you add it to your control scheme.
My reason for showing start on speed, stop on flow is not very theoretical and it comes from George Matousek. He was this Czech engineer, who knew everything there was to know about pumps (and beer), but was not very talkative. So when I asked: Why George? His answer was: Because it works! Naturally, you are right that if the minimum system curve is as you have assumed, it would not, but I have not run into such case yet. On the other hand, if Murphy is right and anything that can happen will, than one day maybe I will.
Béla Lipták:
FROM MY own personal experience, I have found feed-forward schemes difficult to implement and tune. In the applications like the one described, I have had better success playing around with the maximum ramp rate adjustment in the VFD's and allowing the top level PID controller to compensate. If the VFD's are restricted in how fast they can ramp up, and the pressure control PID has enough gain and derivative action to stay ahead, the loop will take care of itself whenever a lag pump jumps in.In the ideal case, the VFD's are configured with a fast ramp rate, but the PID sends two seperate speed command signals to the VFDs. With both pumps running the signals to the two pumps are identical. When a lag pump is kicked on, the signal to the lag pump is immediately forced to zero percent at the beginning of the cycle. The signal to the lag pump then floats up to match the signal to the lead pump, but it is subject to a slow ramp rate restriction. This gives the pressure control PID time to adapt to the higher flow rate. After a few seconds, the ramp rate restriction to the lag VFD is turned off.
That's my opinion.
David Gardellin, Onyx Valve Co.
Need an Expert Opinion? |
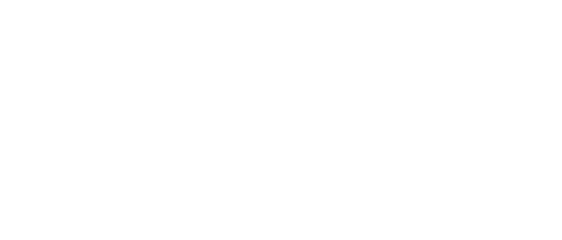
Leaders relevant to this article: