Measuring Two-Phase Flows
Advances in Coriolis flowmeter technology now enable the meters to handle two-phase flows, such as a mixture of gas and liquids. These devices are also much faster to respond to changes in flow, thanks to newer digital techniques that let them respond in milliseconds.
Also Read: Flow and Level Instrumentation
At Chemtura Corp.'s Great Lakes Chemical facility in Manchester, U.K., technicians were having problems with a batch line that makes a variety of water treatment chemicals for heating systems and desalination applications. This process combines three feeds into a tank, blends and pH-balances the batch, and pumps it into a storage tank using a traditional Coriolis meter to measure flow. Sometimes the product needs filtering when it's pumped from the tank, which reduces the flow.
"We had large discrepancies between the metered inputs and output, and it was clear that the traditional Coriolis meters were not ‘seeing' the entire product passing through," says Roger Marsden, director of Westmeade Services Ltd., which provides technical support to Chemtura. "Depending on the flow rate, up to 200 kg of product was ‘missing.' When the product was filtered, as much as 1,000 kg went unmetered."
The company tried using a digital Coriolis meter to see if this would solve the problem. To test the meter, technicians installed a Foxboro CFT50 meter from Schneider Electric in series with the existing meter on the outlet to compare their performance. At the onset of flow, both meters had a zero reading, while the density reading indicated they were "wet and empty." Once the flow began, the CFT50 started to measure immediately, but the traditional meter took 16 seconds to register the flow, thereby allowing about 4 kg of material to pass through unmetered. At full flow, the two meters had the same readings. However, when the flow tubes drained, the existing meter stalled, failing to register the final blow-through of product. "We removed the old meter based on the CFT50's good performance," says Great Lakes instrumentation and evaluation manager Mark Wilkinson.
According to Wade Mattar, flow product manager, field devices for Schneider Electric, "Newer digital techniques have let the devices' use expand into different applications such as that of loading and unloading milk trucks [Figure 1]." When a truck comes from a dairy to a processing plant and is emptied, a small amount of milk inevitably remains in the lines. If the milk sits too long, it will sour, so it's necessary to completely clean the lines and tubing. "The changing flow conditions from full to empty typically mean gas gets mixed in with the liquid in the line. Older instruments would have shut down for several seconds trying to figure out how to deal with the gas, meaning the facility is missing lots of flow measurements, but digital Coriolis meters can easily handle these upsets," continues Mattar.
Figure 1: Newer digital technology enables Coriolis meters to better read both mass flow and density, which is useful in applications such as loading and unloading milk trucks.
Schneider Electric
Over the years, Mattar has seen a continual shift from the importance of just repeatability to accuracy for process control. "For example, due to a lack of accuracy, dairy processing plants in the past were losing 5-10% of the milk delivered from the truck, which they still had to pay for. More accurately metering the milk puts more money in the processor's pocket," he says.
Better Material Compatibility, Signal Analysis Techniques
"The most popular and advancing technologies today center around Coriolis mass flow, electromagnetic magmeters, vortex technology, thermal mass and ultrasonic flowmeters," says Jerry Stevens, product management team lead, flow products, Endress+Hauser. "While vortex, ultrasonic and electromagnetic technologies are inherently volumetric by their nature, thermal mass and Coriolis meters are considered traditional direct mass flow measurement devices. However, some of the volumetric devices do have the capability to generate a compensated output, maybe with the addition of temperature or pressure, or even fixed values, to output in mass engineering units."
When it comes to recent enhancements to the performance in the flowmeter itself, Stevens says, "The best way to understand this is to look at the sensor, as well as the transmitter function and technology. The advent of new microprocessors and signal processing speeds have allowed better signal analysis techniques, which has improved all types of flow devices in general." In addition, devices with diameters as small as 40 microns and up to 108 inches are demonstrating improved accuracy and stability with today's digital signal processing.
Standards for better material compatibility for certain processes have also become a big factor for sensors. Examples include NACE-compliant materials for the chemical industry and NORSOK-compliant materials for the oil and gas industry, where super duplex stainless steel, a form of austenitic stainless steel, is now being used. Exotic high-nickel alloys as well as materials such as zirconium and tantalum, suitable for highly corrosive applications have also come into play. Current sensors can handle higher process pressures. "In fact, it's not surprising to find flowmeters with the capability to match class 1500/2500 pressure ranges for many of the most commonly used flow technologies," says Stevens.
The operating temperature range of sensors has also increased. "Industry demands for external ambient temperatures for most instrumentation used today in the highest percentage of applications is around -40 to 140 °F, but it's not uncommon for process temperature requirements to mandate that the sensor technology must function from -328 to 842 °F," says Stevens.
Improved vortex technology has increased the meters' suitability for measuring steam as compared to meters using traditional volumetric technologies such as differential pressure. "Additional measurement and input capabilities mean the device can eliminate the need for flow computers and directly output mass flow rates and calculated energy values to cover a wider range of process operating conditions, and refine end users' process capabilities," he says.
He gave an example of how vortex wet steam technology can even make better beer. Typically, a brewer heats a combination of milled grain and water with steam. Poor steam quality can impact the amount of heat or energy imparted in the process and the resulting produced wort. "Pressure changes from pipe reductions, as well as constricted flow through valves, tees and elbows, changes the steam type, superheating steam." This causes inaccurate monitoring of the used energy.
According to Stevens, using state-of-the-art vortex meters now solves the problem. "The meters ‘know' the flow rate of steam regardless of changes in steam types because they can integrate temperature, pressure and, with innovative signal processing, obtain steam quality. This can ensure an accurate value of energy that's being used to control the process. This allowed a user to pinpoint inefficient areas in their plant operation, leading to process efficiency gains of over 20%," he says.
Flowmeters Help Measure Flare-Off
A recent trend in thermal dispersion flowmeters is the customer need for in-situ calibration checking and verification to meet environmental and safety regulations. "By that, I mean the capability to verify the flowmeter is still within calibration tolerances without physically removing it from the process stream," says marketing director Randy Brown of Fluid Components International (FCI). "In-situ calibration verification is an advantage because it's very expensive to remove flowmeters from the process, transport them to a lab, and wait for the lab to check their calibration, only to be told the meters are fine."
According to Brown, thermal dispersion meters operate by measuring the energy being shed by the sensors to molecules of the process fluid. "Our meter design features two thermowells. One is held at a constant temperature, and the other one is active and changing temperature with the flow. The differential temperature between the two thermowells is proportional to the direct mass flow rate. Thermal dispersion is therefore inherently dual-function, measuring both flow and temperature," he says.
Thermal flowmeters come in both inline and insertion configurations. The insertion style is more popular because it can be inserted with a single tap point, and the sensors are immersed directly into the flow stream. They can measure almost any kind of gas, including mixed-composition, moist and dirty gases.
With no moving parts to foul, break or wear, thermal dispersion meters are suitable for rugged, harsh applications. "We have a SIL-rated meter and global agency approvals on the entire instrument, from the sensor through the electronics and enclosure, for Class I, Div. 1, Zone 1 type explosive atmospheres, as well as NEMA 4X and IP67 ratings on the enclosures. Depending on the specific model, they include a local readout, multiple 4-20 mA analog outputs,and digital bus communications, including HART, Foundation fieldbus, Profibus and Modbus to communicate with operators and their control systems," says Brown.
While FCI's air/gas thermal flowmeters are found in a wide variety of industrial process and plant settings, including on-shore and off-shore flaring applications, they have recently become a good choice for flare gas monitoring applications at hydraulic fracturing sites.
Brown explains, "At fracking sites, it is natural gas that is being flared off, and the U.S. EPA and other regulators require measurement and reporting of the flared natural gas to determine if routine flaring can be continued or not. In the U.S., regulations stipulate that sites flaring off more than a certain amount of gas must instead recover it or pay fines equal to purchasing/consuming the gas."
Eliminate Long Straight Runs
Also agreeing that accuracy is increasingly important, in this case for differential pressure (DP) meters, is Nick Voss, product manager of flow instrumentation designer and manufacturer McCrometer Inc. "DP meters are more accurate because of improved DP transmitters. For a long time, DP transmitters were the weak point in the measurement system because although they were accurate at the middle to high range of their full span, their low-range measurements were inaccurate. Over time, DP transmitter manufacturers have done a lot to improve the sensitivity of their equipment."
For measuring fluid flow in closed conduits, the American Gas Association (AGA) or ISO 5167 require certain lengths of straight upstream piping to meter accurately, depending on the upstream disturbance. For instance, an orifice plate downstream of a double elbow in a 10-in. line needs 440 inches of upstream run. Even a Venturi meter needs about 220 inches for a 10-in. line, meaning that a lot of straight upstream run is required for an accurate measurement.
Figure 2: As the flow approaches the cone inside a V-Cone meter, the flow profile "flattens" into a well-developed profile. When the flow passes the cone, the cone shape causes short vortices to form. They create a low-amplitude, high-frequency, stable signal.
McCrometer
"In contrast, consider our V-Cone, a differential pressure-type meter similar to a Venturi or an orifice plate, but without the disadvantages," says Voss. As the flow approaches the cone inside the device, the flow profile "flattens" into a well-developed profile, even in extreme flow conditions. When the flow passes the cone, the cone shape causes short vortices to form. The vortices create a low-amplitude, high-frequency and stable signal (Figure 2). "The design lets users, for instance, bolt the device to a double elbow, requiring zero upstream run," says Voss. "The V-Cone basically conditions out flow disturbances leading to the meter, thereby eliminating the need to use a conditioning plate."
Ultimately, regardless of the type of flowmeter, there is usually one element to be wary of, warns Voss. "In choosing a flowmeter, users must assess the environment it will work in. For instance, because Coriolis meters operate on vibration, they can be susceptible to vibration in the line. Most ultrasonic meters have to be specially designed to handle high-temperature steam and low-temperature cryogenic service. DP meters require ensuring the DP transmitters can withstand the temperature of the process fluid. And mag meters can be susceptible to electrical signal noise."
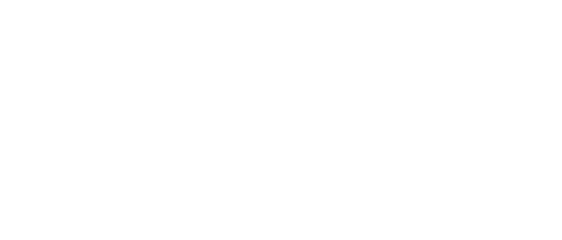
Leaders relevant to this article: