Adoption strategies for Ethernet-APL will be very much intertwined with the value proposition it represents relative to current technologies. The grassroots unit or production facility is one extreme, where, given a clean design sheet and a critical mass of available Ethernet-APL devices, the simplicity and advantages of a unified high-speed network architecture that extends from field instruments to the cloud—yet preserves existing workforce familiarity with HART—is quite compelling.
But that greenfield plant design is still a ways off, given the lead time for instrumentation and system developers to bring the necessary solutions to market, not to mention the testing, trials and tire-kicking that end-user organizations will demand before betting a new plant on any new technology.
At 3M, for example, initial laboratory tests will be followed by pilot-plant implementations plus assurance testing that the technology passes the company’s rigorous internal standards for intrinsically safe operation before Ethernet-APL will be approved for a production environment or for widespread use, according to Robert Sentz, senior engineering specialist.
Bottom line, while the ultimate value proposition of Ethernet-APL will be in a greenfield facility, progressive end-user organizations will meanwhile be looking for more isolated use cases at brownfield facilities to test out and prove the new technology’s worth. Testing is appropriate, but for Ethernet-APL to win on its own merits in a brownfield environment, “It’s got to be a pretty specific use case that really needs that higher bandwidth or will benefit from the greater amount of power that can be delivered over APL,” notes Peter Zornio, CTO Automation Solutions, Emerson. “It’s a very simple rule: if you’re not putting in new instruments, you’re not going to broadly deploy APL,” he adds.
The need for speed
Many of the most apparent use cases for HART-IP over Ethernet-APL derive from the increased availability of data that higher bandwidth affords. In a brownfield context, this is most relevant when adding complex new instruments that generate more data of diagnostic significance.
Real-time access to valve signature data from a valve controller, for example, can be used to diagnose a range of issues before they lead to unscheduled process downtime. The same can be said for Coriolis meters, magnetic flowmeters and radar level gauges (see sidebar). Process analyzers in particular will benefit from the order of magnitude increase in power made available to instruments by Ethernet-APL relative to 4-20mA, representing a less expensive installation than the power supply plus four-wire Ethernet connections that otherwise might have been needed.
But the larger context of increased secondary data bandwidth is the ability to collaborate more effectively, and to send that more nuanced secondary data more easily to the individuals—and applications—that can make effective use of it. Think of a diagnostic application that pulls some data from the instrument, some from the computerized maintenance management system (CMMS), some from a condition monitoring system and some from the distributed control system (DCS). A beleaguered engineer might spend all day manually pulling that data into a spreadsheet before even beginning to analyze its meaning. Or think of the roaming technician who can quickly access real-time HART device data through a tablet wirelessly connected to the plant’s WiFi infrastructure—access that was previously available only back in the control room, didn’t reflect real-time conditions, and even then, was accessible to the technician only via walkie-talkie or a physically connected, low-bandwidth handheld.
Transitional architectures
For most end users—especially in the US, where few greenfield facilities are expected to be built in the near term—their first experiences of Ethernet-APL will be in hybrid environments that also include 4-20mA HART devices. On the positive side, with the debut of fully configurable input/output (I/O) systems some 10 years ago, industry already is on its way to moving I/O from control room environments out into field junction boxes.
Configurable I/O has delivered substantial benefits of its own, helping to decouple hardware design from system software development and taking instrumentation and control system design off the critical path of project execution. It’s also reduced costs and system footprint, eliminating traditional marshalling cabinets in many newer facilities. Like fieldbus before it, Ethernet-APL effectively distributes I/O even further, relocating the transition between analog sensor signals and the digital world of ones and zeroes into the field devices themselves.
Today’s HART-based control architecture relies on devices using the 4-20mA (grey connections) or WirelessHART (dotted red connections) physical layers. Often, the WirelessHART gateway connects to the control network with HART-IP over 4-wire standard Ethernet. Additionally, multiplexers and remote I/O may use RS 485 and Modbus to communicate data back to the area control network. As Ethernet-APL instruments become available, they can be connected to the area control network via HART-IP (orange connections) though a simple APL field switch. And as confidence grows, an APL power switch can be added to bring power and communications to multiple field switches that power many instruments, including new instrument types like video cameras or thermal imaging systems.
From a practical perspective, this means that the remote junction box is where 4-20mA HART and Ethernet-APL are most likely to converge. That remote junction box could relatively easily include both configurable I/O as well as an Ethernet-APL switch—both of which speak HART-IP over Ethernet up into the control system architecture. Further, a potential mix of Ethernet-APL with traditional 4-20mA HART devices will likely entail a range of network infrastructure devices designed to accommodate the transitional hybrid architectures required.
While dual devices sharing an Ethernet connection in the same box are easy to imagine, hybrid approaches are also likely. Analog Devices, one of the suppliers of chipsets for Ethernet-APL as well as the multiplexers that extract HART data from 4-20mA loops, has envisioned a device with hybrid functionality. And for suppliers like Emerson, which uses a physical module to characterize its remote I/O channels (rather than software), a new Ethernet-APL module under development will allow these new digital channels to coexist side-by-side with their 4-20mA HART counterparts.
In all three of these scenarios, a shared commitment to the HART ecosystem and data model will ease the industry’s ultimate transition to Ethernet-APL as the standard physical layer for field instrument communications
Greenfield benefits await
In the not-too-distant future, a greenfield facility or new production unit offers the most fertile ground for Ethernet-APL technology, since the baseline will involve comparing proven Ethernet-APL plus HART-IP technologies with the 4-20mA plus HART status quo. A greenfield design need not weigh sunk costs against new benefits. Rather, a clean-sheet design will allow end users to realize the full benefits of a secure, unified digital infrastructure that reaches from field devices to enterprise systems and the cloud.
Having a critical mass of instrument types available that support Ethernet-APL will be critical for greenfield designs to succeed, believes Robert Resendez, control systems supervisor for the oil, gas and chemicals division of Bechtel. “I remember finding all the instruments we needed being a challenge in the early days of fieldbus,” he says. “We try to give our customers one standard protocol throughout the plant design, and HART is pervasive. Everybody has HART—even some of the smaller PLC (programmable logic controller) manufacturers.”
From an architecture perspective, tomorrow’s Ethernet-APL systems won’t look all that different from the remote, configurable I/O systems that Bechtel advocates today, Resendez adds. Indeed, replacing remote enclosures filled with configurable I/O with remote enclosures filled with Ethernet-APL switches may even allow system designers more flexibility when it comes to how many devices can be connected through a remote enclosure of given dimensions.
In any case, the transition to Ethernet-APL spurs (out to individual instruments) should be a relatively straightforward adjustment from a design perspective. The addition of the APL trunk concept will allow for new distribution models in areas lacking infrastructure for power and communications. And when it comes to installing and commissioning this new breed of devices in a greenfield facility, users will really begin to benefit from the dramatic improvements in communications speed that the move to Ethernet-APL represents.
Dow has used “smart” instruments ever since they were first available, but only relatively lately begun to rely on continuous monitoring of its instruments’ HART data for predictive diagnostics applications, says Jeff Konrad, technical solutions team leader in the realm of automation interfaces. “So, with Ethernet-APL, the first thing is faster data,” he says. “My first questions are during commissioning and startup. We know sometimes it’s hard to communicate via traditional HART—sometimes it’s slow, sometimes we have interruptions. So, if it helps during startup and commissioning there will be a real advantage.”
Jason Urso, chief technology officer for Honeywell Process Solutions, cautions that we as an industry really need to focus a bit less on how great it will be to get more data faster and instead figure out just what we’ll do with even more data once it arrives. “I’m a big advocate of APL,” he says, “and I think we’ve got to continue moving in that direction. But let’s also figure out what we’re going to do with all that data now that we’re collecting it.”
Urso also agrees that standardizing on HART-IP over Ethernet-APL will help instrument and system suppliers get to market more quickly with the product offerings that end users need to take advantage of this new field networking technology. “HART’s well known to us in part because it’s used extensively used by our customers,” he says. “They have the knowledge. They have the competence, the expertise and the track record. And I believe true benefits tend to be sustained for a longer period when you have that ecosystem of knowledge and existing tools that are proven in use.”
Latest from Industrial Networks
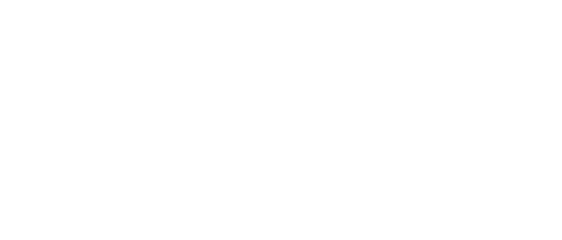
Leaders relevant to this article: