IN OUR JULYĀ 2005 issue, we noted that the servers are coming (āRemote Control,ā CONTROL, July 2005). Soon, you will be able to control remote plants, pipelines and offshore platforms from afar, and youāll be dealing with IT, condition monitoring, loop tuning, and process modeling software that runs in remote servers. In new systems, none of the enterprise-level software has to be in your plant. It can all reside on a server at your central engineering center, a vendorās support center, or at a specialty supplier.
And, for truly remote systems, you wonāt even need a local control room or an HMI/SCADA system. A portable laptop will suffice as an HMI when you or a tech has to visit the site.
All this requires segregating the real-time, field-based part of a process control system from the enterprise side, and making the real-time portion of the control system into a fortress thatās immune from attack by Internet creatures.
A Fisher control valve with Fieldvue is installed on a petroleum feedstock flow at a Texas oil refinery. It can control PID loops all by itself, thanks to fieldbus. If the fieldbus link to the host is lost, loop control continues. Source: Emerson Process Management
Steve Garbrecht, product manager at Wonderware points out that segregating control systems is nothing new. āIf we look back to the invention of the DCS by companies like Honeywell, the original architects designed two basic layers to the system: a regulatory control layer and a supervisory layer,ā he points out. āIt would have been easier to design a single layer so I can only assume that they had a good reason for it.āPerhaps they envisioned, 30 years ago, the ability to truly distribute a system as low and as far out as possible. Today, microprocessor technology makes it possible to put monitoring, diagnostics and control logic all the way down to the sensor level. āAs sensors go digital--and the transmitters that house them contain microprocessors--information, diagnostics and computational abilities become available at the device level,ā says Bruce Jensen, manager of systems marketing at Yokogawa."Continuing the trend that began more than a decade ago, microprocessor-based intelligence is becoming increasingly more distributed throughout refineries, petrochemical plants, power plants, pulp and paper mills and other continuous process plants,ā says Alex Johnson, system architect, Invensys Process Systems. āThis has had, and will continue to have, a major impact on the way these process plants are engineered, operated and maintained. Intelligence will clearly keep moving into the field.āāWith todayās semiconductor capabilities, extreme miniaturization, and exponentially increasing processing power, the ability to embed intelligence or decision-making capabilities into smaller and smaller devices is not only an option, but a requirement,ā adds Gricha Raether, industrial control and distributed I/O product manager at National Instruments. āThere are currently hundreds of smart sensors on the market that feature built-in microprocessors. These sensors acquire the signal, convert it to a digital signal, then transmit it to a controller or central monitoring system through a fieldbus or industrial protocol.āāIn the case of fieldbus, distributed intelligence is really the name of the game,ā says John Yingst, Experion product manager at Honeywell. āWe presently have fieldbus devices that can do calibration, diagnostics, control, and then alarm when there is a process control or a device problem. Device warnings range from telling us they will soon need maintenance, to loss of an air supply, to overheating, and all the way to letting us know of complete sensor or actuator failure. Control algorithms complete with alarming running in fieldbus devices is commonly know in the fieldbus world as ācontrol on the wire.ā Control functions include PID, totalization, signal characterization, signal splitting, input selection, and general-purpose math.āTerry Krouth, vice president of PlantWeb Technology at Emerson Process Management, adds that fieldbus is designed to be inherently redundant, and to operate independent of a host. "With a Backup Link Active Scheduler (BLAS) in one of the devices on each segment, a fieldbus system can operate without connections to the main system," he explains. A Link Active Scheduler (LAS) controls all the communications in a segment, ensuring deterministic response within the segment and the system. "If the main LAS fails, the designated BLAS takes over."Krouth agrees with Yingst that fieldbus is perfectly capable of running process loops. "In many cases, PID control in the field can operate without needing a host of any kind."Smart devices put paid to all the traditional methods weāve been using to configure control systems. Traditionally, weāve wired field I/O to a termination rack, connected it to signal conditioners, fed it to multiplexers, and transmitted the collected data via a āhome runā network to a central or local control system, which logged all the data, stored it in a process historian or database, ran it through assorted software processing routines, and put it up on an HMIās display for operators to see.
This Beckhoff Bus Terminal at Shanghai Drainage, Shanghai, China, acquires eight channels of data in the field and sends it to the control system via DeviceNet, eliminating all the usual I/O cabling, terminations and enclosures. Source: Shanghai Drainage
Distributed fieldbus I/O and controls, such as Wagoās PFC (programmable fieldbus controller), installed in a pharmaceutical plant, start at about $405. Source: Wago
The Transneft oil pipeline spans 30,000 miles, has 350 pumping stations and 850 holding tanks supplying 35 refineries. It is controlled by 2,500 PLCs and 500 networked PCs running Iconics software, all linked by satellite data links, microwave, and land telephone lines. Source: Iconics
Watching over the Controls
Building a server-based control system requires that the real-time process control portion be extremely reliable and able to carry on without supervision when the link to servers goes down. Or, as Stauffer puts it, āThis approach is only feasible if the DCS equipment has a high level of built-in diagnostics and intelligence that allows it to report faults or potential problems to the operations team.ā
āWith the advent of intelligent devices, information and diagnostics can be used to predict maintenance behavior,ā adds Jensen. āPredictive diagnostics, for example, let a valve tell maintenance personnel that it should have maintenance in the next number of days. The application of the diagnostic engine and the algorithms and methods of prediction are just being developed. This is in its infancy.ā
Or maybe you should step up and handle things. "I think it's time the process control department took back fieldbus from the instrument shop,ā says Rezabek. āThere are many instances where distributed intelligence, control and single loop integrity contribute more to process availability than diagnostics alone."
You may need to fix some problems remotely, says Pat Kennedy, president of OSIsoft. āTo be truly remoted, we need remote maintenance of these systems, which means secure access to the configuration information and tools for maintaining the configurations,ā he says. āWe also need exchange of not just data but also structures, graphics, configurations, and many other kinds of information. For example, if a control system does not share which entities comprise a loop, graphic, advanced control or report, then trying to remotely use the embedded information is not possible.ā
āRunning software remotely is not a problem nor is viewing it provided that you have a good network and the software is designed either for remote operation or supports tools like Remote Desktop Connection [RDC],ā adds Kennedy. āHowever, to maintain that software you have to have good knowledge of its current state, security issues, potential problems, and configuration changes, plus the ability to fix issues without traveling to the site. It will be a long time -- if ever -- before this is multi-vendor, so look for products that are designed to run remotely with appropriate attention to back up operation, redundancy, fault avoidance for network problems, configuration management, and so on.ā
Finally, field equipment with smart diagnostics might overwhelm an operator, points out Lane Desborough, marketing manager at Honeywell. āConsider that today an analog point in a control system can have on the order of ten configured alarms, such as high, low, rate of change, etc.,ā he explains. "Abnormal Situation Management consortium research shows that operators are overwhelmed with the volume of alarms which happen during an abnormal situation. Now picture a plant where each device has two hundred alarmable parameters and events. Imagine the amount of additional load this is going to place on an already overtaxed operator. Impending signs of catastrophic events are going to be buried in a sea of spurious alerts from NAGs - nuisance alarm generators.ā
Desborough continues, āIf the distribution of control actions, alarms and events to thousands of āsmartā field devices results in the operator becoming the first line focal point for coordinating activities among these thousands of smart devices, then the operator is going to be a very busy person. Likewise, if the smart devices are automatically sending work orders to the maintenance system, where is the maintenance planner getting the process knowledge and business insight to prioritize these actions for maximum business benefit?ā
There is no doubt that remote, unattended control systems pose maintenance problems far different than those in a staffed plant. However, modern software makes it possible to run all device and system alarms through alarm management programs that sift out the spurious from the critical. Also, one feature of a server-based remote control system is that maintenance and operations can be staffed around the clock by experienced engineers and technicians at a central location who can bring vast knowledge and resources to bear on a problem.
As Jensen says, diagnostics of remote systems is in its infancy, and managing the maintenance of unmanned sites may be the biggest problem of all. Ā As we note in this monthās Control Report, maintaining a modern distributed control system, with its myriad embedded processors, can be a nightmare.
The Importance of Being Open
While weāve concentrated on describing remote, unattended systems, very few control systems operate in true standalone mode. Almost all need to be supervised, monitored, analyzed and fine tuned. As Desborough puts it, āWhat happens if the business objective suddenly changes from āmaximize throughputā to āminimize energy consumptionā and, as a result, all the control loops have a sudden change in performance and each take independent action to notify the operator or maintenance guy? How is the business context, the goal, communicated down to the individual controllers in order to suppress alerts?ā
Enterprise-level software makes it possible to analyze the workings of a plant and coordinate supervisory changes when a situation like Desborough posed occurs. Such software includes loop analysis, maintenance management, asset management, MES, ERP, SCADA, historians, and a host of specialty software for various industries.
This works best if the hardware and software are not proprietary to a vendor or, as Stauffer puts it, āBeing open is absolutely critical. Openness allows users to realize the benefits of distributed intelligence. If intelligent field devices from different vendors cannot coexist and effectively communicate their full set of data, then the potential benefit of distributed intelligence is lost.ā
Kennedy and others say that OPC ā although far from perfect ā is a good answer: āOPC as it stands has fueled a geometric increase in the amount of information that is available in real time ā nearly 50% of the interfaces we sell today are OPC,ā says Kennedy.
Raether agrees: āEngineers and technicians in charge of choosing and integrating products from hundreds of vendors providing hardware and software are challenged with making sure that they all and play nice and talk to each other. There have been multiple efforts in the industry to make equipment from different vendors compatible with each other. One such very successful standard is OPC.ā
And then there is fieldbus. "Foundation fieldbus is a vendor-neutral DCS,ā says Rezabek. āFunction blocks are not as extensive as what may be available on the DCS or PLC level, but that's mainly because too few of us are making extensive use of it. Once users catch on, I think suppliers are likely to respond to the demand for more āblockwareā."
Distributed vs Standalone
Weāve concentrated on distributed systems here, but standalone control systems still have a place in the sun. Some engineers stand by their traditional standalone control systems. āFor our relatively simple process control needs, we have discouraged distributed control, believing that it is better to have a central PLC-based master control that can be monitored and modified as needed,ā says Doug Rhodes, manager, electrical power & automation group at Dayton & Knight, North Vancouver, B.C. D&N is a consulting engineering firm that specializes in water and wastewater.
āWe want to maintain control of the control system,ā continues Rhodes. āSince a loss of communication with the PLC can usually be tolerated for a short period, distributed systems are not deemed necessary.ā
Standalone systems can take advantage of all the modern hardware that makes distributed control possible. They can operate unattended as easily as a distributed system can, communicate to far-away enterprise servers, and take advantage of device diagnostics, wireless networking, web servers and redundant architectures. An unattended remote distributed system is a standalone system when communications fail, so the distinction between standalone and distributed is getting blurred.
What is clear, however, is that the face of control is changing. There are many challenges remaining ā getting systems from various vendors to talk to each other, making sense out of equipment diagnostics, and managing alarms ā but true remote control is becoming more practical every day.
Latest from Industrial Networks
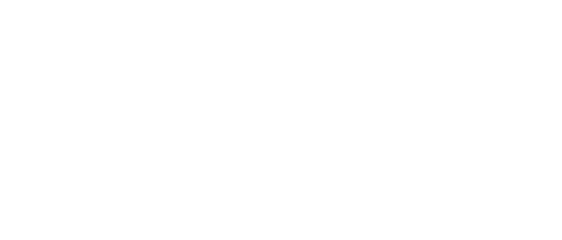
Leaders relevant to this article: