This year, those camps finally seem to have merged into one. Researching this article, we have seldom seen such complete convergence of opinion among users, systems integrators, and vendors. The entire control system community seems to agree that the time has come for controllers to be based on commercial off-the-shelf (COTS) hardware.
This unanimity of opinion is a great sign for the future of COTS because it indicates vendors are on the same page as users. This will help vendors to develop COTS control products that truly serve process industry needs.
Examples of this united front abound. "Rather than expend the costs of developing specialized hardware and proprietary operating systems, vendors [that use COTS] can devote more resources to developing control applications and solutions," says Glenn Richter, a project engineer with Milwaukee-based We Energies.
"COTS allows us to focus our resources on the value-added applications required by our targeted markets--the power generation and water/wastewater treatment industries," reports Steve Schilling, the vice president of product development for the power & water solutions division of Emerson Process Management www.emersonprocess.com).
All agree that COTS has a better price/performance ratio and much lower development costs than proprietary solutions. "Costs are lower and there is a much faster evolution of the hardware and software platforms," according to Richard McCormick, a process control engineer with Ultramer Ltd., Levis, Quebec.
"COTS offers faster implementation, faster enhancements, volume benefits in quality, more interfaces, and less custom engineering for hardware and software," observes Jeff Brown, a product marketer for Beckhoff Automation (www.beckhoffautomation.com). "This reduces our need to amortize those costs over longer life cycles or charge higher costs to customers."
Even with respect to reliability, the last redoubt of proprietary solutions, COTS is winning the war. "COTS systems are more reliable than purpose-built systems because COTS products are used in control solutions worldwide and have been for years," says Chris Ward, a senior design engineer with systems integrator ROV Network Ltd., Aberdeen, Scotland (www.rov.co.uk). "If they have a bug, someone will find it. Handcrafted systems cannot be proved reliable until they have been properly punished for a few years."
Vendors agree that COTS is up to meeting reliability requirements. "COTS technology continues to get better and better in terms of cost-to-performance and, in many instances, now matches purpose-built components in terms of reliability," reports Roland Gendreau, product marketing manager, Foxboro Automation Systems (www.invensys.com).
Another sign of acceptance is a recent press release from the Open Modular Architecture Controls (OMAC) users group (www.omac.org). According to the release, OMAC has been traditionally associated with open architecture controls for CNC applications. The users group reports that OMAC has now evolved to an epicenter of activities applicable to process and hybrid manufacturers in addition to its original discrete manufacturing constituency.
End users and systems integrators usually have unique and interesting takes on vendor spiels, but not in the case of COTS controllers. To a striking degree, both parties agree COTS controllers are an unstoppable force that will eventually engulf the entire real-time process control market.
Given this agreement, it was perhaps inevitable that the last line of proprietary control is falling to COTS. The mighty DCS, long the mainstay of large process control applications and certainly the most formidable bastion of proprietary hardware and software, is rapidly crumbling in the face of the COTS onslaught.
What Happened to My DCS?
All of the major DCS vendors have switched to COTS to some extent, some to a striking degree. Westinghouse (now a part of Emerson) has deployed its WDPF system for decades in traditional large-scale DCS applications such as power plants and water/wastewater plants. The company's newest-generation DCS relies totally on COTS for control.
Ovation customers agree. "There is certainly an advantage to manufacturing in COTS quantities as far as spreading out development costs," adds Richter of We Energies. "This has had a tremendous impact on control systems where, for example, we used to deploy proprietary operator consoles sparingly. Now workstations are inexpensive to the point they can be added at will."
Foxboro was one of the first vendors to jump on the COTS bandwagon. Its I/A series employs COTS components such as Microsoft Windows-based workstations and servers from Dell, standard Intel and AMD microprocessors, VRTX real-time operating systems, and Ethernet. Gendreau says, "Not only do COTS components cost less, the automation vendor can often source them from multiple vendors with rapid lead times to support modern just-in-time manufacturing practices."
Honeywell was the preeminent firm in the early days of the DCS. Its proprietary TDC systems did much to advance process control for large-scale applications. According to Paul Gerhart, Honeywell Industry Solutions engineering fellow, the company's controllers now use COTS components such as Motorola and Intel processors, CompactPCI backplanes, and operating systems from Wind River and Microsoft.
Although no one is using the term DCS anymore, the process automation systems sold by traditional DCS vendors all now employ COTS technology. They judiciously mix COTS and proprietary hardware and software to create control systems optimized for the process industries.
All of these vendors realize the value of COTS and adapt these technologies wherever feasible. "When COTS components meet the performance, functionality, and reliability requirements of industrial applications, they often represent a better value than purpose-built components," says Gendreau of Foxboro. "COTS also makes it easier and more cost-effective for vendors to keep their automation systems current."
Traditional DCS vendors are rapidly integrating COTS into their control systems, and PLC vendors are a step ahead. These vendors are designing new controllers exclusively using COTS components. "PACSystems, our latest controller platform, is 100% COTS configured with Intel Pentium and Celeron processors, PCI and VME backplanes, and the VxWorks operating system software," according to Connie Chick, controller and I/O manager, GE Fanuc Automation (www.gefanuc.com). "Cost is an issue, but time-to-market and performance are the main benefits of COTS technology. Although more processor-type components may be required to reach the performance needed, the cost is still usually less than the development of a purpose-built solution based on medium-quantity suppliers."
How Good Is Cheap?
COTS components are less expensive than purpose-built solutions, but there are many other reasons for using controllers based on them. In fact, most users agree cost should not be the primary factor driving the COTS vs. proprietary decision.
Even best-of-breed COTS components cannot overcome insufficient investment in critical areas of control system design and implementation, says Kevin Totherow, president, Sylution Consulting. "When COTS is selected primarily to lower initial costs, the entire control system is often designed cheap, installed cheap, and maintained cheap with little training or documentation."
Totherow says proprietary systems are often perceived as more reliable because users are forced to install systems per well-defined standards and have to attend special schools to learn to install, operate, and maintain the systems. "Proprietary systems keep foolish people from doing foolish things," he says. "However, great systems can be built using COTS if the correct equipment is selected for the application, and if this equipment is installed and maintained correctly."
COTS control systems require some training, but familiarity with standard technologies can reduce the learning curve. "We use Ethernet technology that is commonly available, widely understood, and commonly used," observes Len Averyt, an electrical engineer with Texloc, Fort Worth, Texas.
Although Averyt has limited IT experience, he reports few problems using Ethernet for networking. When problems did arise, his IT department was able to help with his IP addressing scheme because they understood Ethernet and IP, even though they had no knowledge of PLCs and automation. He says, "No special connections or special equipment are needed."
Integrators Like COTS
Internal IT resources know COTs, and so do most process control industry personnel. This is a key selling point for many systems integrators. "We need to teach operators not only to use the system, but also how to modify it to add additional lockouts and visual interfaces," says Ward of ROV Network. "All our control systems use COTS components and are open-source, and this greatly facilitates training."
The open-source nature of COTS technology can be crucial when a systems integrator is trying to get a client to accept a control system. "If operators don't like your system, it's the kiss of death," adds Ward. "Open-source software and hardware lets our clients change the interface to suit their needs, and it very quickly becomes their control system."
Process control systems are customized based on specific user circumstances, and this is especially true when they are linked to upper-level plant computing systems. COTS components excel in this area, especially when compared to proprietary control systems. "COTS products define and enforce standards that bring a level of flexibility and interoperability to control systems," says Richter. "Conformance to standards provides for easier data connectivity between systems and reduces or eliminates the need for special gateways or bridges."
Many users customize their control systems by adding advanced control algorithms, often from third-party suppliers. It is often difficult to integrate these solutions into proprietary systems, but COTS provides standard interfaces and links to these solutions. "Hybrid process control systems can easily apply applications from a wide variety of sources because most hybrids operate on widely used operating systems and on standard hardware configurations," observes Matt Bothe, a senior automation engineer with CRB Consulting Engineers, Plymouth Meeting, Pa. "COTS simplifies development of custom algorithms and increases the availability of third-party applications, providing users with a plethora of choices."
Wait, It's Not All Good
Although vendors and users alike agree that COTS is the wave of the future, users have a better handle on the inevitable implementation problems. Most caution that COTS should be selected for performance reasons rather than questionable and often ephemeral cost savings.
One of the main COTS "gotchas" (Table II) is the incompatibility of supposedly standard hardware. Many vendors tout their use of COTS, but restrict the user to certain components. "One of our control system vendors touted the use of a COTS component, but we didn't find out until it was too late that there was a restrictive list of exactly which components could be used," reports James Loar, engineering group leader, Ciba Specialty Chemicals, Newport, Del. These incompatibilities can be especially problematic if your company already has an agreed-upon supplier, Loar says. "We already had a price-discount contract with a sole-source supplier of the COTS component, but we could not use it."
Environmental constraints are another area of concern. "COTS equipment is not as rugged [as purpose-built industrial equipment] since the broadest market is office applications rather than industrial control," says Dale Evely, PE, I&C consulting engineer, The Southern Co., Birmingham, Ala. Users must carefully check the operating specifications of COTS components and are often forced to provide controlled environments. This can negate apparent initial cost savings.
Another area where COTS often suffers compared to industrial components is testing prior to sale. Although the commercial market quickly reports bugs, COTS is closer to the bleeding edge of technology than typical industrial hardware.
These and other limitations have forced some users to restrict their use. "COTS technologies are not appropriate for controllers because of frequent required upgrades," says Pierre Tremblay, P.Eng., a control systems engineer with Syncrude Canada, Fort McMurray, Alberta. "COTS controllers must often be upgraded because of obsolescence even when the platform can still do the job."
Security Is a Relative Term
Security is becoming a more important issue for control systems, and the very openness that makes COTS so attractive can be a drawback when it comes to preventing unwanted intrusion. Hackers know Ethernet and TCP/IP but are much less conversant with proprietary industrial control networks.
Widespread commercial use of web server technologies and Ethernet has made it possible to equip even inexpensive control components with Internet communication capabilities. Many process plants are taking advantage of these capabilities to web-enable their control systems. This can lead to security issues.
"Security is becoming a larger issue," reports Dan Perrier, PE, president, Automated Control Systems (www.automation-software.com). "As an example, we found out about a company that had placed PLCs on its Internet-accessible LAN. They thought their PLCs were safe from intrusion until we showed them how we could gain remote access from any browser. We ended up working with them to place their PLCs behind a firewall."
Proprietary systems usually have some measure of security built into the price. COTS hardware often does not, and purchasers are expected to invest additional sums to ensure security. "Security is an area that users rarely had to deal with a few years ago and vendors would prefer to ignore," says Richter of We Energies. "Locking down a system to prevent hacking or the introduction of foreign software or viruses can become a full-time job--one that many users don't consider when purchasing a system."
COTS systems can be made just as secure as proprietary systems, but in most cases this will require additional time and money after the initial purchase and installation. Users often must rely on other resources such as their IT departments or outside systems integrators to accomplish this specialized task.
COTS for All?
Use of commercial technologies in industrial control system hardware and software components is sure to increase, and this should benefit both vendors and users. Despite some caveats, COTS will prevail because of price/performance advantages, openness, and greater user familiarity as compared to proprietary systems.
"COTS' advantages are substantial: lower costs, reduced inventory, state-of-the-art technology, and availability of a knowledgeable support base," says David Decker, PE, president of Instrumentation Technology (www.itinc.us).
Decker believes the use of COTS technologies will continue to grow, but he does offer some caveats. "Changing technology makes it a challenge to support a variety of software releases. And COTS components tend to be designed around standard application sizes that are not applicable to all projects."
Bear in mind that COTS technology usually is not as inexpensive as it might appear, because off-the-shelf components usually must be tweaked for industrial use. Despite these limitations, COTS components cannot be ignored as a viable part of modern control systems. "Most COTS problems can be eliminated if control technology experts are brought into the project at an early enough point," concludes Decker. "Properly chosen COTS components will address most security or safety issues."
Continue Reading
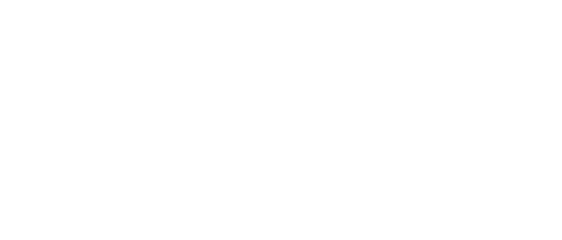
Leaders relevant to this article: