One of the best ways to reduce energy use and conserve natural resources is through recycling. Two out of every three pounds of steel is produced from previously used steel, making it the most recycled material in North America, says Dave Brandt, melt-shop engineer at Nucor. Recycling steel consumes between 60% and 74% less energy than producing new steel from raw materials.
Rapidly rising prices for commodities, such as iron ore and copper, are raising concerns that the world will run out of these materials. A much more likely outcome is increased recycling of most materials. Process automation professionals have a significant role to play, as producing new products from recycled raw materials is often quite challenging.
Such was the case for Nucor at its Marion, Ohio, facility. The plant manufactures a full line of rebar, sign supports, delineators and cable barrier systems using recycled steel. During steel recycling, scrap metal is heated in an electric arc furnace (EAF). Depending on the type of steel being produced, a combination of elements is added to the viscous steel to create the appropriate steel alloy.
This process requires large amounts of energy, varying significantly depending on the amount of scrap placed in the furnace. When we purchased the Marion facility, operators relied on estimates to determine the amount of steel placed in the furnace. This often caused the metal to be overheated, in which case it had to be recycled again, explains Brandt.
To control the EAFs temperature and reduce the number of reheats, Nucor developed a low-cost scale and weighing control system using National Instruments (NI) LabVIEW human-machine interface software and Compact FieldPoint controllers. The control system accurately calculates the amount of steel in each burn. Knowing the exact amount of scrap metal placed in the furnace allows us to precisely calculate the amount of electricity required to heat the furnace, recounts Brandt.
Before implementing this scale system, our steel measuring was hit or miss. We didnt track reheats prior to deploying the new control system in 2007, but with the new system we only needed 10 reheats out of more than 6,000 batches, far fewer than in 2006, adds Brandt.
The new system also saves energy because Nucor now uses only the electricity needed for the EAF. However, an EAF by its nature still draws large amounts of power.
Were assessed monetary penalties for using too much electricity, so we developed an online reactor system in series with the furnace to control power use, comments Brandt.
Nucor installed a 13.8kV reactor with an online tap changer in series with the EAF transformer that can vary inductive reactance. IT limits current spikes and controls the power factor to the furnace electrodes. An NI FPGA controller regulates the tap changer based on power factor, flicker and energy consumption.
Three electrodes melt the scrap steel. Current spikes are caused when melting and heating steel. Breaking the arc and short-circuiting the electrodes with scrap causes power to vary greatly and can result in higher electrical utility demand charges.
On current reversal of an AC electric arc furnace, we want to control the power factor at about 0.85 to 0.9 lagging, so the voltage leads the current. This causes current to flow sooner than if power factor were 1 or leading, and uses power more efficiently, explains Brandt.
Implementing complex control schemes often requires more than just basic ladder logic. By programming with LabVIEW and PACs, we have seen a tenfold increase in efficiency, and drastically reduced the costs of facility automation, says Brandt.
Its easy to understand the current rung of PLC logic, but its hard to follow the overall layout and logic. LabVIEW PAC programming is graphical, so it is easy to follow the code and figure out the overall program, concludes Brandt.
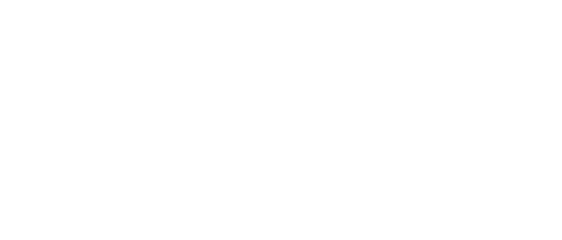
Leaders relevant to this article: