Cardinal Ethanol - Plant Sustainability With a Plant-Wide Optimization Control System
By Jeremey Herlyn, Plant Manager, Cardinal Ethanol
Cardinal Ethanol, LLC, is a 100-million-gallon-per-year ethanol production plant located in east central Indiana near Union City. The plant commenced production in November 2008 and processes 36 million bushels of locally grown corn, produces approximately 100 million gallons of ethanol and 320,000 tons of distillers dry grain with solubles (DDGS) and corn oil, while capturing 53,000 tons of food-grade CO2 per year. Its staff of forty-nine work in a state-of-the-art facility built with the latest advances in equipment and control automation technology for fuel ethanol production.
Management at the plant understands its volatile industry with regards to commodity price swings on feed stock, corn and the final product, ethanol. The company's goal is to consistently achieve the highest levels of process efficiencies to compete successfully in the industry.
Cardinal Ethanol focuses on four key mission objectives:
- To maximize yield (gallons per bushel) through efficient plant operations;
- To improve productivity through the use of best-in-class technologies;
- To optimize production margins by reducing energy consumed;
- To fuel America's economic development.
Six months into production, which coincided with the 2008 financial crisis, ethanol production facilities were severely impacted as the demand for goods decreased. Biofuel producers risked insolvency. However, Cardinal Ethanol management forged ahead and ramped up production with a sharp focus on running the plant as efficiently as possible. The corn/ethanol crush spreads hovered between razor-thin- to-negative margins, and the plant continued to focus on increasing its production margins with the knowledge that the plant could always perform better. Cardinal's management, with the help of its financiers, maintained the position of investing in "sure technology" to achieve "sure margin gains."
Rockwell Automation suggested that Cardinal Ethanol consider implementing a plant-wide model predictive control (MPC) optimization technology to help the company achieve its goals. After careful consideration, the company chose the Rockwell Software Pavilion8 MPC solution primarily due to the industry leadership and experience Rockwell Automation holds in multi-unit, plant-wide optimization. In addition, Rockwell Automation has a project execution track record that is well-known and unparalleled in the ethanol industry.
Why Was MPC Implemented?
Consider a simple production process with feedstock, process reagent stream, steam energy and final product. This simple process is represented in the diagram above. It has two key variables to control, product quality (A) and the production rate (Fx). However, the facility has the ability to adjust and manipulate the feedstock rate (F), process reagent rate (F) and the energy to the facility (Q). There are three adjustable variables designed to control two outcomes. The question is what is the best combination of variables for process control of final product quality and flow?
There are significant process interactions between the feedstock, process reagent, energy due to chemistry and thermodynamics of the process. For example, feedstock and reagent streams have energy and will interact with the heat provided by the steam heat source (Q). The presence of these interactions within the plant process streams makes it difficult to control the plant, especially in multi-stream and multi-unit processes. While this issue was likely considered in the original construction of the equipment and control systems, the traditional method of reducing the complexity of controls is to decouple and select a single control loop (e.g., steam flow) that controls product steam temperature. Feed or process reagents are not used for temperature control, but in reality they can be, and for some constraints in the operation, it may be the better set of variables to control the plant. The complexity of these control interactions is why successful operations prefer experienced operators who, over time, learn how to control and respond to the interactions. Simplified controls remove the interaction complexity, but at the cost of losing degrees of freedom. That is why many plants have significant potential that is not realized until a MPC system is implemented.
The Rockwell Software Pavilion8 MPC technology accounts for all these interactions and unifies them in the control design with real-time controls. This technology takes into account the multivariable interactions and considers the dynamic behavior of the process. With precision models of the system, the MPC technology can use the capacity, energy and process reagents more effectively, resulting in a savings of 5% to 15% in operating margins, energy or production costs. Rising costs of agricultural commodities and the increasing cost of energy have made these savings crucial to all plants and independent of the economic climate.
Cardinal Ethanol asked two questions of the Rockwell Automation team. Is it possible to optimize the production rate of our ethanol facility, given there is a trade-off between high production rates and maximizing the conversion of corn to ethanol at the cost of higher residence times in the batch fermentation process? And, is it possible to maximize the level of on-specification ethanol and distiller's dried grains with solubles (DDGS) while minimizing the cost of energy per gallon of production? Cardinal recognized that it needed good model predictive solutions to these two operational challenges.
Because the ethanol process is several times more complicated than the simple one product/single step process system, the process has several stages of unit operations. Cardinal implemented MPC to address these complex challenges, such as numerous equipment/process stream constraints, ethanol and DDGS specification constraints and a 65-hour process time from grind of corn to the final products, alcohol and DDGS.
All the variables and their dynamic responses to changes in feed flow, energy and qualities were built in from plant data collected during testing and historical data from the Cardinal Ethanol facility. It took three months of testing and nine months to commission all components. Once the system was online, it stabilized the plant by reducing variation in the process, enabling transitions to happen smoothly and unifying the plant operating facility between operating teams and the day/night shift. This significantly reduced fluctuations in the facility.
The Pavilion8 MPC technology was installed in three stages: plant testing, modeling and commissioning/optimization. The project required a server networked to the distributed control system (DCS), but did not require the purchase of additional hardware. The MPC system unified the plant controls from grain (grind) to the 200-proof production.
The system stabilized the drop glucose levels in the fermenters and then drove it to a minimum level through precision control of fermentation feed, temperatures and enzymes (plus enzymes addition timing). This increased conversion of starch to ethanol on a consistent basis, essentially yielding more ethanol for the same amount of corn, and added to the bottom line of the plant, thus increasing the facility's sustainability.
The MPC made improvements that originally seemed difficult to obtain at the start of the project, since all operations were striving for efficiency improvements through hourly and daily best practices. However, the Rockwell Software Pavilion8 MPC solution improved plant stability and reduced variability on all key process variables, especially the batch fermentation operations. As a result, the following benefits have demonstrated a successful project:
- Ethanol yield increase - 2.2%
- Ethanol production increase – 10%
- Energy/gallon reduction - 8.2%
- Great operator acceptance
- Payback in under 12 months
In summary, the project met and exceeded the expectations of Cardinal Ethanol and the plant learned some key lessons through the implementation of this project:
- MPC projects help a plant uncover process factors that may be restricting higher production, yield or energy efficiency.
- Good control instruments are an integral part of an MPC project.
- The MPC system significantly reduced the carbon footprint of ethanol production, therefore increasing the sustainability index of the biofuel.
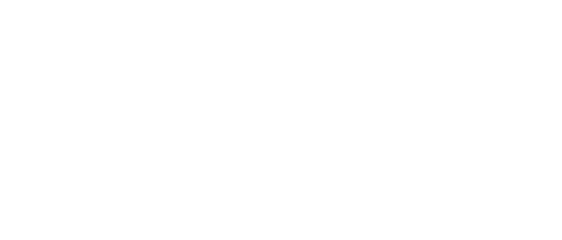
Leaders relevant to this article: