If end users determine the technology delivers promised benefits and required rates of return with acceptable risk, and if suppliers agree on standards and interoperability, then the technology is widely adopted.
However, this process can take years or even decades.
Remote access has traversed this path successfully in the process industries, proceeding from supplier promotion to widespread end-user adoption in less than 10 years. How do we know? Because a host of end users and systems integrators are eager to share remote access success stories. But, before we get to these successes, read on to see the advantages that remote access provides to process industry end users.
Competitive Advantage
Remote access has no standards-making organization touting its capabilities. It's not proprietary, and there isn't widespread agreement on how to accomplish it, yet it's growing at a breakneck pace. When something comes along that is truly useful and beneficial, end users jump on it.
By using remote access and other automation, McCall Farms, a manufacturer of Southern-style foods in Effingham, S.C., has tripled in size over the past five years, rising from 75+ million pounds to over 250+ million pounds of produce per year.
Jeff Crisp, maintenance manager at McCall Farms, uses a wide range of PC-based remote access technologies that enable him to access process equipment remotely from different plant buildings, from his phone and from home, if there's an urgent need to do so. "I can securely and easily dial into plant systems from my house in order to troubleshoot," says Crisp.
"Using our Beckhoff Automation PC-based control systems, I can watch any process in the plant run from my office," adds Crisp. Access from his home is via a VNC server. "If something must be fixed in the middle of the night, this is a very attractive option."
There is no overwhelmingly popular method for remote access—process automation professionals are using software technologies such as phone dialing systems, cell phone messaging systems, virtual private networks (VPN), virtual network computing (VNC) and various PC-based software programs that allow remote users to view and even control PCs at the local site.
Control equipment vendors are also joining the party, allowing remote access via cell phones apps, providing software for remote access to their equipment and systems, and making money by requiring site licenses for remote access.
The cost of getting remote access to your control system varies from AutomationDirect's $4.95 cell phone app to access its C-More HMIs up to much more expensive and complex systems with gateways, servers, VPNs, security appliances, terminal servers, site licenses and so on.
Figure 1. McCall Farms remotely monitors processing equipment in its food plant using various PC-based technologies.
Remote Access Fuels Success
Based on the responses we got for this article, it seems like everybody in the process industry is using remote access in one way or another, for a variety of purposes ranging from equipment diagnosis to optimizing control systems.
At AOC Resins in Collierville, Tenn., remote access allows AOC to keep all its engineering experts in one central location, where they can tend to the needs of seven processing plants spread across the country. (See "Optimizing Process Operations From Afar," which shows how AOC can tune batch reactors at any of its sites from its home base in Tennessee.)
Likewise, Nor Cal Controls, a systems integrator in Placerville, Calif., used remote access to solve a similar problem with some unfamiliar software. "Recently, we were in the process of providing balance-of-plant tuning for AEP at one of its new power plants," says Bob Lopez, control engineer at Nor Cal. "We purchased ControlSoft's InTune PID tuning software, but because of our unfamiliarity with the software and the GE ICS PID controllers, our process models were generating tuning values that were completely off in magnitude."
Lopez contacted ControlSoft and was connected with a process engineer, who assisted them remotely using TeamViewer software. "He was able to access the control system remotely and participate in the bump tests and process model evaluations," explains Lopez. "This allowed him to identify and correct our PID scaling factors, which had been the cause of our initial invalid numbers."
Saving time and travel expenses is a major benefit of remote access. For Nor Cal Controls, it meant the company didn't have to wait for an InTune expert from ControlSoft to travel to the site. For AOC Resins, it means in-house experts don't have to travel to process plants. It can be safer, too.
Glenn Givens, principal at Givens Control Engineering, a systems integrator in Burlington, Ontario, Canada, says he used remote access to avoid traveling to "a location where my personal safety could not be guaranteed," as he puts it. "Using a VNC connection, we quickly discovered a major roadblock that halted the project for months. Had I traveled there, I would have found out after one day that there was no point in staying, and the travel costs would have been extremely wasteful."
When something goes wrong at a plant, a systems integrator is often called. "The control system is typically considered the first culprit when things go wrong," says Phil Murray, principal at FeedForward, a systems integrator in Marietta, Ga. "Remote access allows a first-hand, real-time view of the control system that greatly improves our ability to diagnose and solve problems and provide a rational explanation of events and possible solutions."
And when there is a problem with the control system, remote access allows the vendor to help out. "At another customer site, we called the DCS vendor for assistance, and they logged in via VNC to find and correct the problem," says Givens. "The person with whom we communicated logs in to customer sites all day, full-time in his technical support role."
Global systems integrator, Maverick Technologies also leverages remote access to service its clients and ease its internal work. "In addition to the more mature areas like wireless tank gauging, SCADA and other remote concepts, we've made heavy use of the PC's remote access capabilities on the newer control systems," says Chad Harper, Maverick's director of technology. "Internally, we utilize remote access to our internal development PLCs and DCSs, which allows for expanded capabilities in training and project support. We have several clients where we perform project and maintenance work directly in their control system through dedicated PC-to-PC connections. We also provide network monitoring services for clients who have too many remote facilities to support adequately in person."
As noted above, equipment vendors are supplying remote access capability, and OEMs use it for their customers. Process Engineering Resources Inc. (PERI) in Salt Lake City makes X-ray fluorescence (XRF) analyzers for the mining/mineral processing industry. The analyzers are used to perform elemental analysis of slurries in ore concentrator operations.
Dave Taylor, system engineer at PERI, says, "We use remote access to the XRF analyzers to assist plant personnel in troubleshooting issues, analyzer calibration, updating software or adding site-specific features. Since mining operations are often in remote areas that are difficult and time-consuming to reach, remote access is crucial for providing timely support." PERI's analyzers are based on an Opto 22 PAC, and Taylor gets his remote access via an Opto 22 iPAC app on his iPhone.
There are many ways to skin the remote access cat. Here's another method, this one used by Sukup Manufacturing. Sukup, based in Sheffield, Iowa, makes grain-handling equipment such as bins, dryers and conveying equipment. Matt Koch, electrical engineer at Sukup, says the company redesigned the control system on its QuadraTouch continuous-flow dryers using a PLC from Phoenix Contact with Ethernet communications.
"We offer optional global system for mobile communications (GSM) functionality, so that our customers can keep an eye on dryer operations from any cell phone," says Koch. "The GSM modem from Phoenix Contact provides this add-on functionality. The PLC is already set up to connect to the modem, so all we have to do is simply plug the modem into the serial port of the PLC and activate service onto a SIM card to realize instant GSM functionality."
Figure 2. Sukup Manufacturing lets customers monitor operations of their grain dryers via remote access over a cell phone.
Some remote access systems do more than just diagnose problems and monitor operations. Dart Oil and Gas uses it to provide data to field engineers. And, unlike typical systems that use browsers and cell phones to view conventional HMI displays, Dart's displays were designed from the beginning to be web pages. (For more on how Dart uses remote access, see "Distributing Production Data").
Meanwhile, Malisko Engineering, a systems integrator in St. Louis, Mo., has been using remote access for 10 years, so it's in a good position to summarize the advantage of remote access. Dan Malyszko, senior systems engineer, sums it up: "Remote access to industrial automation systems has proven to be an extremely cost effective component of a plant's support system. Remote access provides plant personnel, OEMs and integrators with timely, interactive troubleshooting when issues arise.
"Getting a process line back up and running in minutes rather than hours by giving technical support resources via remote access can help a plant avoid thousands of dollars of downtime. Another benefit is reduced costs when making control system programming changes. Depending on the nature of the programming change request, travel costs can be eliminated entirely when performing the work via remote access."
Challenges Can Thwart Remote Access
Two major and related challenges face engineers who want to employ remote access: security concerns and their own IT department.
Hackers are getting so good these days, they can penetrate a control system through any port—including even the maintenance port of a UPS. Space does not permit an analysis of all the cybersecurity problems facing industry today, but suffice it to say that users need to be very careful.
That's where the IT department comes in, for better or worse. "Due to NERC/CIP requirements, we're seeing some of our customers moving us to a secure VPN, only allowing access to PCs a layer removed from the control network," says Lopez of Nor Cal Controls. "While still extremely helpful, it's less functional than being directly connected to the control system."
In some cases, bypassing the corporate IT system is the best option. "In one operation where we could not access the analyzers from the corporate network due to IT policy, we installed a phone line and a modem directly in the analyzer cabinet for dial-up access," says PERI's Taylor. "We have also used satellite-based Internet connections for remote sites."
Or you can have your systems integrator or control system vendor take care of it. "Our primary remote access technology is via a secured VPN connection using a Cisco ASA 5500 Series adaptive security appliance or similar hardware," says Malyszko of Malisko Engineering. "Oftentimes, we procure, install and configure VPN hardware for our clients as an option to the base cost of a project."
James Burnand, director of the Mid-Atlantic region for Grantek Systems Integration, uses remote access technology from Rockwell Automation and others, and he advises limiting remote access to just the control system. "To maintain strict control of remote access, it's best to keep automation and control protocols at home in the manufacturing zone. Limiting the protocols to this zone helps ensure that the automation and control devices are communicating with known devices and applications, with user authentication and role-based authorization."
Hardware and software vendors offer tools to help uses address some security issues. Ken Eldridge, president of Open Automation Software, explains, "All of our components and services support Windows Communications Foundation. We work with Homeland Security closely to make sure all of our products are not vulnerable to security threats. All of this is done by just utilizing the .NET Framework in the Windows operating system."
Apart from security issues, other disadvantages of remote access include slow display updates over wireless connections, loss of communications at critical times and the need to use a PC or PAC that supports Windows-based software and Ethernet connections.
In spite of these disadvantages, end users are climbing aboard the remote access bandwagon faster than they've adopted any other technology we can remember. Today, any company that doesn't offer remote access to its automation systems is behind the times.
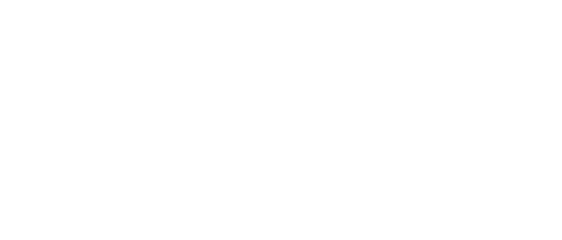
Leaders relevant to this article: