[sidebar id =1]A joint venture of BP and China Petroleum and Chemical Co., the SECCO plant in Shanghai produces 1.2 million tonnes per year of ethylene. At its construction stage in 2003, SECCO awarded Honeywell an integrated advanced process control (APC) and operator training simulator (OTS) project. The APC scope covered ethylene, butadiene extraction, olefin conversion, aromatics and styrene units.
APC offline design was finished by the end of 2004, before the plant startup, and APC implementation was completed in 2006. In 2009, SECCO carried out a major process revamp and capacity expansion project, so APC was upgraded and updated, and real-time optimization (RTO) with Honeywell Profit Optimizer (using distributed quadratic programming, or DQP) was added. During a turnaround in 2014, some APC models were re-tuned, and the DQP was revamped. Since then, SECCO has seen sustained quantitative benefit from naptha feed optimization.
“Performance has been improved constantly by updating, upgrading and revamping over the past 10 years,” said Julia Wang, APC engineer, SECCO, in her presentation at the Honeywell Users Group Americas event this week in San Antonio. “It’s still not perfect,” she said, but thanks to APC control of draft pressure, bottom air damper position, feed rate against constraints, and coil outlet temperature (COT) to control conversion, “We have high uptime and stable oxygen control, with feed maximization and very good performance.”
Profits optimized in real time
Now, the plant is starting to measure the effects of its revamped Profit Optimizer. “The underlying Profit Controller models and performance are the key and foundation for executing Profit Optimizer, which uses the same dynamic models,” Wang said. “No effort is required to develop steady-state models, and no extra model maintenance is required.”
[sidebar id =2]Cycle execution can be as short as once per minute. Honeywell UniSim and Technip SPYRO models can be easily integrated through Profit Bridge, and correct dynamic response from upstream to downstream sections are guaranteed. SECCO also found it easy to implement additional overall mass balance models and a few Profit Bridge models on top of Profit Controllers.
The new additions coincided with correcting some existing problems. In the 2010 implementation, the Profit Optimizer scheme involved optimization with every feed rate change. “But there are 11 furnaces, and the operators had to change each of their feed rates,” Wang said. When a constraint, such as high third-stage stage discharge pressure from the cracked gas compressor (CGC), became active, the operators had to adjust each furnace feed rate down, one by one, and quickly. When the constraint ended, production had to remind the operators to increase all the furnace feeds.
Now, an updated scheme automatically performs these tasks on every feed change. “The original scheme caused us to miss our objectives, but now we have success,” Wang said. In addition, they learned there’s no need to include Profit Controllers that have no potential constraints for optimization into the overall Profit Optimizer – the Profit Optimizer dominates Profit Controllers, and Profit Controllers that are not in the Profit Optimizer can execute their local optimization solutions.
How it works
Now, operators have three tools to carry out optimization operations. First, a “dummy” bridge controller allows controller status to be turned off. It is used to initially set the optimization controller and optimization variables, and is not required in normal situations. Second, the Profit Optimizer is normally on, and is used to monitor how the Profit Optimizer moves. Third, operators can set the individual furnace Profit Controllers to allow the feed rate to be moved by the Optimizer, or not.
SECCO has dedicated professional APC engineers, each responsible for three process units, and each plant has a process engineer as the APC contact. Operators’ experience trumps APC: if they see any trouble, they turn it off. “We encourage operators to comment on APC and give suggestions for improvements,” Wang said.
APC engineers review and check key variables no less than three times a week, many of them every day, including on/off status, optimization status (on or off, and for room for further optimization), controller performance and model quality. If something is wrong, they perform a deep dive to find the root cause from a valve, instrument or APC, and take immediate action to log, track and correct the issue. They deliver weekly and monthly reports to summarize uptime rate and other process key performance indicators (KPIs).
The implementation has allowed the plant to optimize flue oxygen at an average of 1.8%, minimizing fuel gas consumption. It’s also increased naptha feed by 1.27%, said Wang, which is “a very big benefit.”
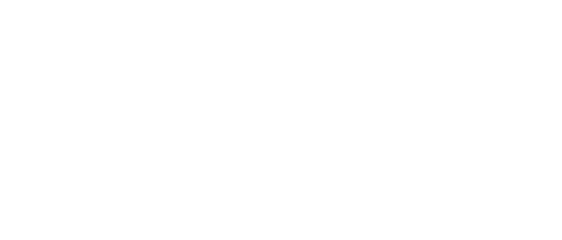
Leaders relevant to this article: