The planning and scheduling of resources in a refinery depend on the availability, allocation and use of hydrogen. That's why optimization of hydrogen treat-gas systems can offer so many benefits, said Marco Andrei of ExxonMobil Research & Engineering (EMRE) at the 2009 Invensys North America Client Conference in Houston.
Why is hydrogen important in refining operations?
"It needs to meet the desired molecular specifications and to meet increasingly tight product sulfur specs," said Andrei. "Product margin upgrades are driven by the availability of hydrogen. Supply and management of hydrogen is central to optimizing the refinery run plan. Resource planning and scheduling is dependent on hydrogen."
Once the treat gas is consumed, it finds its way to the fuel-gas system. "Often refineries are limited by the handling of the amount of gas," explained Andrei. "The cap limit often rides on the fuel-gas limit. The availability of hydrogen also affects your crude mix. We want to optimize the hydrogen supply and how it's distributed, and we want to prioritize which consumer in the process should get it."
Hydrogen treat-gas systems are very complex and subject to many disturbances. Hydrogen suppliers can be steam reformer hydrogen plants, catalytic reformers, chemical plants, hydrogen recovery membranes or third-party suppliers. "Producers are disturbances or opportunities," said Andrei. "They are things you have to live with."
Consumers of hydrogen include cat feed hydrotreaters, residual conversion units, hydro de-sulfurization units for fuels, lubes and solvents, and hydrocrackers. The disposition of treat gas can be cascaded to consumers over the hydrogen network through hydrogen recovery membranes, and ultimately it ends up in the refinery fuel gas system.
Andrei identifies six ways ExxonMobil developed to capture these opportunities to optimize—ROMeo process models, best-fit, on-line model-tuning strategy, real-time pricing updates, real-time, on-line implementation, regulatory controls and daily user/workflow processes.
"ROMeo process models rigorously track hydrogen purities across the entire treat-gas network," explained Andrei. The ROMeo Model Library includes models such as source, sink, mixer, splitter and flash. Also, in-house first-principles custom models can be used to predict treat-gas composition changes, product yield or composition and reversal of treat-gas flows.
"The best-fit, on-line model tuning strategy ensures predictions to keep up with the plant," said Andrei. "It relies on the measurement model to calculate offsets between plant and model values and minimizes deviations from plant values while weighing their accuracy. Weighted offsets can be used to drive the tuning strategy for flow rates, purity analyzers and temperatures."
Economic optimization also can be driven by real-time pricing updates to determine the next moves for increased profitability. "The profit objective function equals production realizations minus feed costs minus opportunity costs. The realizations are treat gas purged to the fuel-gas system, yield upgrade incentives at high-margin hydrotreaters and steam generation. Feed costs are third-party hydrogen-purchase feeds to a hydrogen plant. The operating costs are furnace-fuel gas, steam and electricity, for example, to drive major compressors."
A real-time system also automates on-line implementation, handles operating exceptions and presents an advisory option to operations and technical. The underlying regulatory controls work together with the hydrogen system real-time optimizer (RTO) to handle a large number of constraints. "User interfaces and work processes facilitate day-to-day cooperation of operators, process engineers, planners and controls engineers," added Andrei. "This system affects the whole refinery."
RTO carries out optimization and coordinated constraint control tasks. "It benefits mechanisms by keeping the hydrogen system feasible and optimized in response to ongoing disturbances, by balancing the purchase or production of hydrogen vs. additional purging to fuel gas, by optimizing compression costs, by ensuring hydrotreaters receive optimum hydrogen purity and by providing open-loop, off-line benefits," said Andrei.
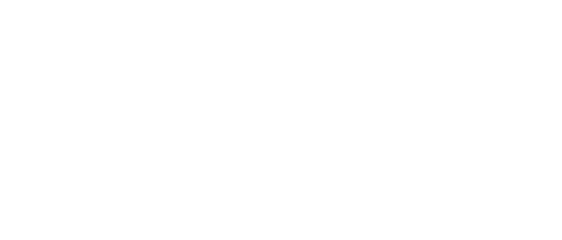
Leaders relevant to this article: