By Jim Montague
Now, don't get distracted. There's a lot more to simulation than pretty pictures. Likewise, simulation has a much longer and more varied history than those colorful CAD/CAM images, and its future is likely be even more diverse than its past.
Of course, process simulation first grew out of the natural and longstanding desire to speculate and project what was most likely to happen next in many applications in an effort to improve them and avoid potential problems and accidents. Now, as more sophisticated and faster information and data processing became available, simulations have evolved from static recommendations to increasingly dynamic operational aids.
Taking Care of Turbines
For instance, Tucson Electric Power Co.'s (TEP, www.tucsonelectric.com) Springerville Station recently needed new controls for its two 380-megawatt, coal-fired, net-combustion engineering drum boilers with an ABB steam turbine. The station also needed an upgrade to include overfire air, low-NOx burners and new hydraulic actuators for the turbine stop/control valves. TEP is the principal subsidiary of UniSource Energy and serves more than 375,000 customers in southern Arizona.
To help avoid possible errors that might delay start-up and service or potentially cause damage, TEP's engineers included detailed control checkout functions on a high-fidelity simulator for the station's new control system, and then also used it for operator training. As a result, they selected Invensys Operations Management's (www.invensys.com) Foxboro I/A Series distributed control system (DCS), which was a major shift from its former, bench-mounted analog controls.
Invensys reports that it has pioneered a virtual simulation approach by modeling control systems using its FSIM Plus simulation of the I/A Series DCS. This method uses actual I/A Series controller algorithms and HMI and DCS configuration tools to provide the most accurate representation of the control system. For example, TEP's staff now has the capability to move the controls and graphics back and forth between the simulator and control room, making the simulator a complete I&C device.
In addition, for TEP's new Alstom turbine control valve actuators to be guaranteed, an Alstom turbine control system also had to be part of the configuration. This led to questions about interfacing to the I/A Series DCS, I/O, turbine protection and operator controls. So, using FSIM Plus, the project was modified to include a connection to GEIP's PLC 90-70 and 90-30 controllers, which ran the Alstom turbine control system programs.
Also, TEP's new simulator and DCS designs went through concurrent development with major DCS loops tested and pre-tuned in the simulator. Feedback from operators using the simulator was then used to fine-tune graphics and make control function changes based on TEP's operating procedures.
The simulator was on-site at the Springerville Station for six months of factory acceptance testing before the new DCS was installed in Unit 1, and it identified and allowed fixes of more than 350 errors before they reached the new controls and the plant.
"Most of these problems were minor, such as graphics configuration errors and simple point misconnections. However, without the simulator, these errors would have been found during critical testing on the live unit," says Chris Wallace, TEP's simulator project manager. "Even simple configuration errors take significant unplanned downtime to find and fix, especially in that high-pressure environment."
Another value of the simulator came when merging the I/A Series DCS and Alstom's control systems. Even though the running turbine and simulator were not connected, initiating the Alstom turbine using the simulator also prevented dozens of interfacing problems. "It saved at least one week of start-up time due to the operator's familiarity with the controls and advanced understanding of how they should interact with the unit," adds Rex Brown, TEP's project manager for the DCS retrofit project.
Mimicking Mining
Logically, one of the emerging truths about simulation is that if the data is specific, accurate and appropriate, then the resulting images of it have the best chance of being genuinely useful.
For instance, to help its mining clients in and around Brisbane, Australia, engineering consultant Meteng Pty. Ltd. (www.meteng.com.au) develops process models and simulations, and recently used Invensys' Wonderware software to create a virtual, interactive environment where its users can design applications, practice scenarios and learn by doing. Meteng calls its solution the Walk-Through Interactive Simulated Environment (WISE). It uses Wonderware's software to process dynamic mathematical data models, display on high-resolution screens in a 3D "cave," and simulate an actual processing plant, including a prototype SCADA and control system (Figure 1).
Though WISE also integrates Apple and Microsoft technologies on its displays, Wonderware's software serves as the main control center and opens the 3D models, loads dynamic processes and initiates or saves training scenarios. Specifically, Wonderware's InTouch Human Machine Interface (HMI) adds a GUI for the WISE SCADA system, while Wonderware's InControl software provides expandable control and scripting that supports the system's interlocks and logic control.
Jim Groutsch, Meteng's managing director, reports these software tools help Meteng apply its process engineering skills when analyzing workflow and developing efficient processes, and also provides standardization and repeatability.
"Once a module is designed, it's easy to rapidly spin off other versions, and tailor them to specific operator and plant requirements. It helps us to be smart and efficient, plus we can do it at a fraction of the cost," explains Groutsch.
For example, he adds that changes and rework to control systems and graphics are also facilitated smoothly, and this enables Meteng to respond quickly to client comments and requests for revisions. Also, when clients are participating in continuous development of their plant, they're actually seeing Wonderware's software at work in their individual environment.
Picture Perfect Power
Ironically, while most simulations build models of existing applications, sometimes old simulators themselves need to be renovated and reproduced in a spiffy new guise.
For instance, Intermountain Power Service Corp. (IPSC, www.intermountainpower.com) near Delta, Utah, generates 13 million megawatt hours (MWH) per year for consumers in Utah and southern California, but the utility was built in the early 1980s with a hard-panel simulator that became obsolete as its model predictions grew different from actual plant responses and its software became outdated.
So, IPSC decided to replace the simulator during a recent DCS upgrade project, and picked Invensys and SimSci-Esscor's DynSim-Power simulation software, which includes the DynSim simulator in the Sim4ME environment (Figure 2). DynSim-Power is a dynamic process simulation program that applies first-principle techniques and thermodynamic data, and features standard engineering analysis and operator training capabilities.
Figure 2: Intermountain Power Service uses Invensys' SimSci-Esscor DynSim software architecture to support acceptance of repeated control system configuration downloads without requiring repeated compilation and linking steps.
Working at IPSC's facility, DynSim enabled rapid tie-in to a third-party DCS simulator, and brought the process models, DCS controls and its GUI together for a complete system.
In addition, IPSC's staff specified using the new simulator where actual DCS software runs in emulated DCS controllers, so hardware costs are reduced, and the simulator can still use the actual DCS' control software. Also, IPSC started simulator development well before DCS installation to allow time for DCS logic testing and operator training.
"Following a four-week planned outage, we initiated the unit start-up and everything went great. This was due to the checkout of the controls and pre-tuning on the simulator prior to startup. This was a great benefit. The simulator paid for itself as a result of the DCS checkout alone," says Bill Morgan, IPSC's DCS project manager.
However, DynSim's benefits didn't end when the upgrade was complete. Though the new simulator is mainly used for training, it also helps address and tests plant issues that arise on the unit. "The operators are on the simulator communicating and showing each other how things work, which has been helpful in terms of training newer operators and ensuring they are all comfortable controlling the unit," explains Fred Tasker, IPSC's simulator instructor.
Jim Montague is Control's executive editor
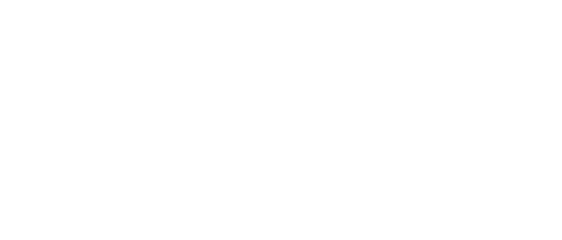
Leaders relevant to this article: