“Ask the Experts,” on ControlGlobal.com, is moderated by noted process control authority Béla Lipták. Béla and his cadre of leading experts in process automation, recruited from among the co-authors of the Instrument Engineer’s Handbook 4th Edition, are “in the box” all month answering process control questions from all comers. The best will be published here.
Q: Fox TV had a news program titled “Water Power,” which suggested that you can gain power from water and the emission of this process also will be water. That sounded like what the “Liptak cell” does. Is this correct?
Herbert Gross
Hollywood, CA
A: No, it's not. This is the typical Fox or CNN reliability of reporting. They left out essential information, such as in order to run the hydroxygen (HHO) process, fossil-generated electricity (not water power!) is used, and when you make that electricity, you use fossil fuel supplies and emit greenhouse gases. They also forgot to note that the efficiency of fossil electricity generation is about 35%, and the efficiency of converting that electricity into the chemical energy of hydrogen in an electrolyzer is 50% to 60%. On top of that, they have to heat the gases to the “self-ignition temperature” of hydrogen (570 °C), which also takes energy.
The HHO process has little to do with water power, but it is good for applications where you need high flame temperature, because the self-ignition of a stochiometric mixture of hydrogen and oxygen will produce a flame temperature of 2,800 °C. This flame temperature is some 700 °C higher than the flame temperature from burning hydrogen in air. Therefore, HHO is good for welding or other processes where the melting of metals is involved.
In contrast, my cell is cool, and it runs on free, inexhaustible and nonpolluting solar (or wind) energy. See last month’s issue of Control (Fuel Cell of the Future) or refer to my book to be published in September, Post-Oil Energy Technology: The World’s First Solar-Hydrogen Demonstration Power Plant.
Béla Lipták
Q: Please give me a brief or provide me with a reference on practical methods for measuring/analyzing natural gas BTU value. This is for a gas plant that uses delivered gas BTU to account for its sales. What current methods (online/offline) are used? Are there any reference standards on the subject?
Ahmed Khalaf, SIE
AC&EE Dept - Engineering Division, Adgas
A: The heat flow rate of a fuel gas can be measured by detecting its mass flow rate and multiplying it by its heating value. These days, gas chromatographs are used to measure the heating value of the gas, and ultrasonic flow meters instead of orifice plates are used to measure the gas flow.
In the past, specific gravity measurements were used as an indirect means of estimating the heating value. Today, continuous and explosion-proof calorimeters are available. These can measure the heating value of any fuel gas, and compensate the combustion controls for variations in both specific gravity and in heating value.
The heat flow rate (Q) of a gaseous fuel is the product of its volumetric flow rate at standard conditions (V0) and of its calorific value (CV) or composition.
In the past, orifice plates were used to detect flow, and the Wobbe Index (WI) was calculated as the ratio between the net calorific value (CV) and the square root of specific gravity (SG):
The advantage of detecting the Wobbe Index was that it eliminated the need for separately measuring the specific gravity, because the product of the Wobbe Index and the orifice pressure drop resulted in a value (KQ) that is directly related to the heat flow rate (Q), without necessitating a separate measurement of SG:
In older installations, one can still run into such Wobbe Index measurement systems or calorimeters (please refer to Chapter 8.7 of the 4th edition of Volume 1 of my Instrument Engineers Handbook for more information), but the newer installations use chromatographs.
Béla Lipták
A: BTU can be determined by GC also, but I don’t know how widespread is the industrial application of GC as a continuous online BTU analyzer.
Ray Annino
[email protected]
A: For Wobbe Index—there are several in use—particularly as it actually has units of energy/volume, there are US and SI versions. To add insult, the standard definition uses HHV (including the heat of condensation of the water produced in combustion), but I have met gas turbine manufacturers who use LHV (not unreasonably, no one condenses water from turbine exhaust).
When I first entered the gas industry 50 years ago, the tool was a continuous recording calorimeter plus a continuous Wobbe recorder (from Kent Instruments)—devices identical except for the burner gasflow control. We did have an experimental home-made GC as well.
Most folks these days use a gas chromatograph rather than a continuous calorimeter or a Wobbe meter—I suspect from familiarity with process GC technology. (How things have changed in the past half century!) The overwhelming trend is to ultrasonic flowmeters, rather than orifice meters, and this gives a further analytical possibility. There is a good correlation between speed of sound and calorific value of hydrocarbon gases, provided you can correct for CO2 and N2 content. There are some recent papers in Google from folk at Emerson/Daniel.
Ian H. Gibson
Engineering Consultant
Process, Control and Safety Systems
Q: Could you please explain the basis on which to select PID output (between on-off PID with pulse-width modulation and continuous analog output) for operating a control loop?
K V Ratnakar
Hyderabad, India
A: The type of final actuator determines whether the controller output needs to be continuous, on-off, or three-state. A PID controller can be used to drive any of these, with the proper interface such as pulse-duration module. For information on how to drive on-off actuators from a PID controller, see my book, Process Control Systems, 4th ed., pp. 167-174.
F. G. Shinskey
A: The output of your control algorithm is dictated by your final control element actuator (valve, drive, stepping motor, power electronic device, relay, etc.). It’s up to the equipment supplier to choose it; then you choose what control law is suitable for your process.
Sigifredo Nino
Senior Process Control Consultant
Invensys Systems Canada Inc.
A: My experience has been the choice is mostly a matter of cost and convenience, in regard to the device driven by the controller. Both output types will work for most applications. But it's usually easier (less costly) to control things like motorized valves and heating elements with on/off operation than in a continuous (non-discrete) manner. As the pulse-width resolution approaches that of the controlled device’s operational range, there's simply not much practical difference between the two anyway.
Al Pawlowski, PE
Almont Engineering
Baton Rouge, La.
Q: I am looking at some software that will run OPC with my Honeywell Experion that will give me some type of “health,” if you will, on the loop. I know there are several companies out there that sell this type of software. Can you give me any advice on this?
Tim Lee
E&I Reliability /Planner
Graphic Packaging International
A: We work regularly with Experion and use
- OPC from Honeywell
- OPC from Matrikon
We have installed Control Performance Monitor from Matrikon many times with great success.
Michel Ruel PE
President
TOP Control Inc.
A: You can extract a fair bit of health information directly from OPC on Honeywell. I generally have shapes that provide that general status information native to Experion, so the operators can see what's going on. Are you wanting to display information to operators or use for troubleshooting as an engineer?
Bridget A. Fitzpatrick
Senior Principal Technical Consultant
Mustang Engineering
Continue Reading
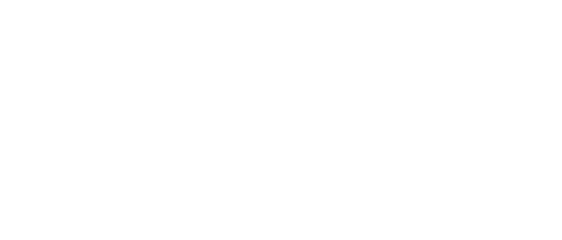
Leaders relevant to this article: