By Paul Miller, Contributing Editor
The Veterans Memorial Pool Park In the town of South Windsor, Conn., is a much-loved summer hotspot for children and adults. Once merely a pond, the local swimmin hole evolved into a full-fledged aquatics center over the years. The modernization of the current complex was completed in the spring of 2002. It houses three separate outdoor swimming pools: a training pool for children; a lap pool; and the main pool. The pools stay open from the first weekend in June until the last weekend in August, attracting an average of 600-800 visitors per day during the hottest months.
The high cost of keeping the pool water clean
While the pools themselves are a relaxing escape for members of the community, keeping the more than one million gallons of water used in the three pools clean is a demanding, round-the-clock task. This falls upon the shoulders of the same busy Public Works Department staff that also operates the towns municipal wastewater treatment plant. The water in all three pools must be continuously circulated through a system of purification filters. High-powered pumps maintain a continuous flow through the elaborate system of water purification filters. These pumps pull water from the bottom of the pool through a series of gutter systems and into surge tanks―one tank per pool. The water is then pumped from the surge tanks through a series of chemical-purification filters before being returned to the pool.
Actual KW readings taken after installation of the Variable Frequency Drives
The high flow demands require some real horsepower: the 152,000-gallon lap pool draws water through the system using one 10-hp, 200-V, three-phase pump; the 156,000-gallon training pool uses a 20-hp, 200-V, three-phase pump; and the 755,000-gallon main pool uses two 30-hp, 200-V, three-phase pumps.
The electricity required to run these four pumps on a 24/7 basis is by far the pools largest operational expense, and tens of thousands of dollars are budgeted for utility costs each season. As a result, Tim Friend, plant supervisor, is constantly looking for ways to improve efficiency and reduce costs, while still maintaining water purity.
ABB drives added to accommodate varying pumping requirements of pools at Windsor, Conn.
We wanted to lower our power bills, says Friend, We knew we were wasting energy by always running the pumps at full power―especially after hours. There are fewer impurities in the water when nobody is swimming, so by slowing the flow at night, we knew we could still maintain adequate filtration in the pool and maintain the same levels of water quality.Friend and his team tried implementing several different strategies with limited success. The first strategy was to completely shut off the pumps each night for a specified period of time. This made it so difficult to maintain water quality that they had to abandon the tactic altogether. They then tried throttling the valves to achieve the proper flow rate through the pumps, but since the pumps ran on single-speed motors, doing so also drove up the motor amps, back-flushing the equipment.
Variable-frequency drives help reduce energy costs
Friend then drew on his experience operating water treatment and purification plants, where variable-frequency drives (VFDs) are often used to allow pump motors to be safely operated at reduced speeds. To find the best solution for the pools, he consulted with Brian Robinson, a sales engineer at FlowTech, a local sales and service representative for ABB VFDs. Friend and Robinson had previously worked together on a number of projects.
Brian turned me on to VFDs a long time ago, said Friend. We saw how great they worked in similar applications on several previous projects. By installing VFDs at the pool, we determined that we could reduce the motor speed, but still run our system with the valves completely open―all the while, achieving the full-flow rate we need to run the filtration systems.
Charlie Albert, Dave Geng, and Bruce Lundie (left to right) handled the installation of the VFD drives, operating the filtration pumps for the three pools in South Windsor, Conn.
On FlowTechs recommendation, Friend and his crew selected appropriate ABB VFDs for all four motors. FlowTech also provided bypass panels for the pumps so that the pool engineers could bypass the VFDs if the need ever arose. FlowTech delivered the drives and bypass panels and Friends maintenance staff―Charles Albert, David Geng and Bruce Lundie―handled the installation, beginning with the smallest pump first.The lap pool was our guinea pig, says Friend. Our goal was to demo the existing flow system, install the bypass and VFD and get it back up and running the same day. Since it was the smallest pump, we had the most physical space in which to work, and we were successful in accomplishing our goal.
Friends crew then completed installation on the 20-hp pump in a day and spent another day on both 30-hp motors. We were thrilled at how quickly and smoothly the installation process went. Although we spread it out over a couple of weeks, it was basically only three days worth of work.
After installation, the pump speeds were set back using the on-board time clocks that initiate pre-programmed, pre-set speeds in the VFDs. The crew programmed the pumps to run at 90% power during open-pool hours, and to ramp down to 60% for 12 hours each night after the pool closed. These reduced settings were expected to reduce energy consumption by 65,000 kWh per season, a savings of more than $7,000 in operational cost annually.
According to Robinson, With the centrifugal pumps used at the pool complex, the relationship between reduced pumps speeds and reduced power consumption is based on the nonlinear affinity laws. For example, if you halve the speed of the motors, theoretically at least, youre using roughly one-quarter the power, so the energy-saving value of any speed reduction is magnified.
VFDs eliminate hard starts and stops
Since the drives were installed, the pool recognized not only a dramatic reduction in energy costs, but also, the pumps produce far less noise. Now we can actually stand in the pump house and hear each other talk, whereas before we were never able to do that, says Friend.
South Windsor, Conn., opens three pools to the public; water now is filtered according to the cycles of actual use to save energy.
Another important benefit is that the drives enable the pool engineers to eliminate hard stops and starts. When the strainers need to be cleaned, or other maintenance needs to be done, the engineers can now ramp the motors down, shut them off, perform the necessary tasks and then ramp the speed back up―all without the high-demand and across-the-line surges from hard stops and starts. The VFDs also serve to protect the pumps and the motors from over-current and under-current, shutting down the system if problems occur, instead of allowing the motors to spin themselves into the ground.A major problem occurs when our pumps lose prime, explains Bruce Lundie, facilities mechanic. We are stepping the speed down at night to save power, so if the strainer baskets become clogged with leaves or debris, we could essentially not draw enough vacuum from the pump. This happened to us before. Once we lost prime during the night. We came in the next morning to find the pumps red-hot and steam boiling out of the strainer baskets, because we had nothing in place to protect the motor or shut down the pump.
With the drives in place, an ABB tech was able to develop user load curves using the ABB DriveWindow Light performance calculation program. He first determined the amperage draw when the pumps lost prime using the trend data in the program, padded the number a little and programmed the drives to trip on a fault whenever that low amperage limit is reached. This prevents damage to the pumps from losing prime, especially during the overnight hours when no one is around.
Two-year payback anticipated
With the energy savings the pools complex now is experiencing, Friend anticipates recouping the entire project budget, the cost of the VFDs and their installation, in two seasons.
We dont have the final numbers back from this season yet, but between the energy we are saving and State of Connecticut energy grants, were thinking the retrofit will have paid for itself by the end of next year. This is by far the best decision we could have made.
Based on this success, Friend already is evaluating ways to incorporate VFDs into other motor-control applications in the future. Working with FlowTech, he has begun designing plans for upcoming projects, including a large water treatment plant renovation. Im so pleased with ABB VFDs that Im specifying the rest of the treatment plan upgrades around incorporating them, says Friend. Weve had nothing but top-notch results from the drives in every experience, and we are extremely confident using them in future projects.
Continue Reading
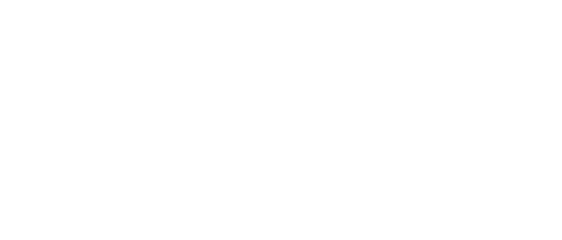
Leaders relevant to this article: