Ted Hill, Director, Global Business Development, Rockwell Automation.
This article proposes key drivers that make moving to the cloud a fundamental transition instead of an exotic undertaking. It also explores the characteristics that enable a manufacturer to deploy a cloud network for storing, accessing, sharing and leveraging data from Internet-connected devices.
- Exploiting the cloud is less intimidating from a resources perspective. Tapping into the benefits of cloud computing is significantly more manageable and routine than it was even a few years ago. Previously, only large-scale manufacturers could allocate and maintain investments in infrastructure, licensing, training, engineering and security necessary to implement and operate enterprise wide applications. Sustaining those applications in the face of constantly changing manufacturing environments was a continuous challenge.
Today the cloud is exciting and opportunity-rich because every organization can harness the technology to achieve more powerful automation, networking and "smart" production. - Boundary-dissolving technologies redefine what is possible. Boundary-eliminating wireless and broadband communication is ubiquitous. Until recently, a significant obstacle was access to the network. Connectivity anytime and anywhere – combined with the mobile processing power carried in smart phones and tablets – puts cloud-based solutions within closer and easier reach. Meanwhile, Industrial Internet Protocol (IP) networking structure and industrial, unmodified Ethernet are seamlessly connecting conventional automation equipment (I/O, drives) with IP-enabled digital devices adopted from other disciplines (video, security).
This harmonious coexistence and end-to-end connectivity among devices, processes, systems and people – combined with cost-efficient cloud computing muscle – is transforming industrial expectations. - Declining costs lower the threshold for justifying high-end capability. Utilizing a unified, IP-centric networking infrastructure to optimize interoperability lowers the cost of exponential increases in processing power, storage and bandwidth. Making it realistic for manufacturers (of any size) to affordably access multiple, aggregated sources of data stored in the cloud.
Remote monitoring and support, for example, have been deployed for more than a decade. Typically by larger operations facing a performance challenges extreme enough to justify the capital investments in hardware and dedicated hi-speed communication links. Cloud-based solutions drive hardware and software infrastructure costs towards zero, continually lowering the threshold to deploy advanced automation. - Concerns over security of data in the cloud are unwarranted. "We could never allow our manufacturing data to go into a public cloud." The perspective is prevalent. But security perceptions – as evidenced by the delicate nature of data routinely entrusted to public and provide clouds across a range of industries – differ from reality. In fact, it's not even necessary to contrast manufacturer reluctance with cloud-sophisticated industries like banking or healthcare. The production team may be reluctant to manufacturing related data in the cloud may not realize that other parts of the company are already utilizing a variety of cloud based applications.
'Remote Asset Monitoring' Makes the Case for Cloud Computing
The increasing sophistication of remote systems monitoring, asset management and engineering support demonstrates how cloud technology facilitates IP-enabled "intelligent enterprise" advances in plant-floor security, connectivity, performance and ease of integration. A mission-critical production asset like a medium-voltage drive illustrates the point. A non-functioning drive on an oil & gas drilling platform, for example, can result in a significant loss of revenue.
Given that risk, energy companies are well-established remote management and support services users. But traditional IT solutions consume capital and related technical resources at levels unique to large-enterprise operations. The cloud-based computing that is taking significant cost and complexity out of those equations enables manufacturing operations on virtually any scale to deploy 24/7 monitoring of valuable drive applications.
Moving remote access and support to the cloud allows a manufacturer to easily monitor performance even from drives located in isolated locations. Critical data about the drive can be easily made available to experts. Now, when a drive issues a warning or fault, the information is easily propagated to create a work ticket for a support engineer. Within minutes, a cloud-based asset monitoring application has an expert looking at the fault and making recommendations to the control room on the corrective actions to take to address the problem. Information only accessible to a technician, in the past, work directly on the drive can be made available to where it is needed.
The practical, cost efficient advances made possible by a cloud solution are byproducts of characteristics unique to this non-traditional IT platform. Here are four examples:
Cloud computing shifts risk from the user to service providers. Within a traditional manufacturing application, the manufacturer is accountable for everything. This includes the hardware, networking and storage, as well as installing and patching the operating system (OS), deploying and configuring the application, and detecting/eradicating viruses. The combination of cloud-based computing removes a significant portion of the exposure by converting the infrastructure, cloud platform and software to purchased (or subscription) services. At significantly lower risk, the manufacturer captures the value of cost-efficient cloud computing, plus the specialized, performance-enhancing domain expertise that a vendor-partner provides.
Cloud "elasticity" makes infinite processing power affordable. Cloud computing multi-tenancy is software architecture essential to cloud services cost-efficiency that can be passed on to cloud customers. It is the ability for a single instance of software, running in the cloud to serve multiple client organizations (tenants). Virtually partitioning data and configurations enables each customer to work with a customized version of the shared application at required levels of security, reliability and performance consistency.
The critical result is on-demand processing power and storage capacity elasticity replaces the ongoing project – and cost-prohibitive infrastructure – that would be required to architect, design and scale a solution that starts with the first piece of equipment and eventually accommodates hundreds or thousands. A cloud platform solution can scale and be cost effective from a few machines or devices to thousands.
Cloud solutions open the door to making better decisions with the support of non-manufacturing data assets. Leveraging the cloud allows access to a tremendous amount of outcome-relevant data that is external to traditional manufacturing sources. One example is energy-related information. Depending on the geographic market where production is based, options on how energy gets to the operating plant, along with per-unit costs and the impact of variable rates, are all tied to information that originates beyond the manufacturing process.
In a remote asset monitoring scenario, it might be important to consider weather as a variable. The rules for whether a piece of equipment is working optimally, and what corrective action needs to be taken, can vary depending on whether the equipment is deployed in Texas or Alaska. The operating environment may have a material impact to equipment performance.
Using a GPS coordinate, it is straightforward to determine the current and historic environmental conditions where a piece of equipment is operating.
Cloud spend hits the operations (not capital) budget. Often a "cap ex" vs. "op ex" tension in how things are paid for exists. The cloud is a positive force for turning a traditional capital expense into a line item easier to justify as part of an operations budget. Deploying an application to remotely monitor a critical asset for example, traditionally represents a substantial capital project to fund components like software licensing, hardware infrastructure outlays, and the application engineering involved to develop a solution.
A cloud solution, by comparison, enables a manufacturer to purchase everything as a service - the platform, software and support in the same way that a consumer pays a fixed amount per month for internet access or phone service.
If It's Not Already in the Cloud, It Will Be Soon
The term "cloud computing" may have nothing to do with the sky, but the metaphor accurately portrays the untapped, limitless processing power and data storage that will be as pervasive throughout industrial manufacturing as it is in daily living. In a recent survey, 54% of respondents said they hardly ever use the cloud, even though 95% routinely use cloud services like Facebook, Gmail, YouTube – along with applications that range from banking to healthcare.
The new "intelligent enterprise" – emerging in successively smarter versions – will be powered by a level of data aggregation, data analytics and integration never before possible. The main drivers are cloud computing and a unifying, Industrial IP-centric network infrastructure that provides an unprecedented ability to combine hardware and software over standard, open industrial Ethernet for ever-greater levels of production process quality, efficiency, security and safety performance.
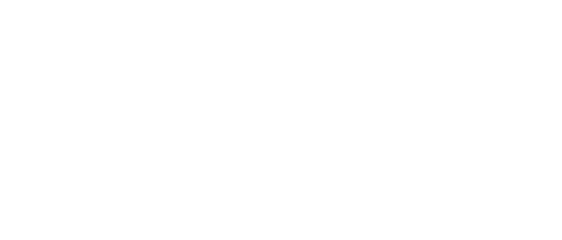
Leaders relevant to this article: