By Walt Boyes, Editor in Chief
"The increasing power and miniaturization of chips coupled with mass production and low cost means everyone's iPhone will soon have an 'app' for PID control or ladder logic," says Control columnist and super end user, John Rezabek. It is already happening in the suddenly burgeoning home automation industry.
Everywhere you look, the embedded controller is with us. It lives in your washing machine, your refrigerator, your slow cooker and your toaster. It lives in your heating and air conditioning system, and it lives in PLCs, PACs and in the controllers that are part of your DCS.
More likely than not, embedded controllers will soon be arriving at your water meter, gas meter and electric meter. The "smart grid" is essentially a grid made up of networked embedded controllers that can control the flow of electricity using a mechanism called demand-response.
This convergence is an essential part of the Internet of Things—an Internet in which these embedded controllers, whether they are in a PLC or a PAC or a DCS controller, or your washing machine, share information with each other instantaneously on a 24/7 basis. Embedded controllers are becoming smaller, faster and more powerful because of Moore's Law, which states that data density doubles approximately every 18 months. The network itself is becoming as important as the devices, as Ming-Chin Wu, president of Advantech's Industrial Automation Group (www.advantech.com), noted at the Advantech World Partner Conference in October of 2011.
Tom Edwards, senior technical advisor at Opto 22 (www.opto22.com) agrees. "PACs offered the bonus of having PC-based and embedded control features built in. One such feature is native communications capability to business systems."
Edwards goes on to say, "As part of their core functionality, PACs natively speak a host of popular application level industrial protocols, such as Modbus, Modbus/TCP, Profibus and EtherNet/IP. PACs have traditionally had PC-like connectivity to the enterprise, and are capable of communicating using standard network interfaces and protocols, such as wired Ethernet, WiFi, TCP/IP, OPC, FTP and SMTP."
The Convergence of Controllers Isn't New Either.
"Convergence of devices," says ARC Advisory Group's (www.arcweb.com) Craig Resnick, "led ARC to introduce the programmable automation controller (PAC) concept in 2002, driven by the integration of multiple control disciplines, such as process, logic, motion, etc., onto a single common platform, as well as the need for PC functionality to run on a reliable, rugged, durable PLC-style form factor."
Since Resnick coined the term in 2001, the number of PACs in the manufacturing industries has exploded. The design of most PLCs, for that matter, has come to resemble that of a PAC, with a real-time kernel and conventional PLC-type programming, as well as the use of function blocks and C++ programming capability. It has gotten to the point where, unless you really look at the hardware architecture, it is difficult to determine whether you are using a PLC in the traditional sense, a PAC or an embedded PC running control software. It is easier to tell by the form factor what a controller is supposed to be. If it is a DIN-rail-mounted device, with modular I/O and networking, it is a programmable controller, whether it is designed to be a PLC or a PAC. If it is part of the backplane of an industrial-grade HMI display, it is an "industrial computer." The actual circuitry and hardware may be identical, but it's just presented in a different form factor.
Resnick goes on to say, "Technology will lead PAC platforms to different footprints and architectures in the future, which will consist of smaller, less expensive and more standardized hardware that will homogenize the controller type."
One of the other trends driving this convergence is the flattening of the Purdue manufacturing model from seven layers to three or four (Figure 3). There is the field device level, the controller/control system layer and the operations/enterprise layer.
Figure 3. The flattening of the Purdue model from seven layers to three or four has made it easier for the embedded controllers on the plant floor to communicate with the rest of the enterprise.
As Tom Edwards noted, the innate ability of embedded controllers, PACs and even some high-end PLCs to speak those standard enterprise protocols, such as Modbus and EthernetIP, has made it much easier to get data from the plant floor to the enterprise, and vice versa. As Invensys' Dr. Peter Martin (www.iom.invensys.com) and Iconics' Russ Agrusa (www.iconics.com) have been saying for years, this means that it may be possible to control a manufacturing company based on business rules and not just on process rules.
"Future PACs," ARC's Resnick says, "will have control intelligence along with production management software embedded into the platform or device, with data and information processed and stored at the platform or device level. PACs will communicate this data and information to other PACs, platforms, devices, HMIs and 'private clouds' for backup, as well as to the enterprise via a combination of wired and wireless networking technologies."
Convergence of these devices is interesting, but what can you do with it? Opto22's Edwards says, "We've also seen convergence in terms of the types of applications in which PACs, PLCs and embedded control are used. From their beginnings, PACs were designed to perform a variety of functions, whereas the PLC's ancestry is closely rooted in discrete control."
So it isn't just ladder logic anymore. But the convergence has pulled the PLC along too. Edwards notes, "Among other features, the faster, smarter processors found in modern PLCs make them suitable for the added domains in which PACs and embedded computers operate. These include process control, motion control and data acquisition. So, although PACs' more organic origins for use in multiple domains make them an extremely efficient, well-designed, multi-disciplinary controller, the much broader range of inputs now accepted by modern PLCs help make them just as well-suited for process and other applications as they are for discrete control."
Edwards continues, "In addition to expanded communications capabilities and a wider cross section of potential applications, the latest generation of PLCs and PACs now boast several other features previously associated more with PC-based or embedded control. These include the use of Intel-based processors, onboard flash memory, removable memory in the form of microSD cards and an easier-to-understand file system."
Most PLCs, PACs and embedded controllers are equipped with native USB communications capability as well, making it possible to use USB memory sticks to program or take data from the device. (Of course, this has a dark side, as we saw in 2010 with the Stuxnet virus, which used a "candy drop" USB stick to get inside the security perimeter of an Iranian nuclear facility.)
As a significant indicator of what this convergence means, ISA recently established a Building Automation Division. Similar devices are being used in both process and building controls as energy management becomes an integral part of process control. For several years now, ABB, Siemens and Schneider Electric have been discussing the convergence of power control and process control in manufacturing plants, which can only occur because the devices used in each application area are, or can be, the same.
Resnick says that this will have a significant effect on the way control solutions are specified and rated. "Solution performance competitive differentiation will be based on the functional software capabilities and IP, as well as the wired/wireless network's speed, security, accessibility and adherence to open standards, rather than the hardware that is processing the software and networking technology.
How soon will we be using the same controllers to run our plants and turn our lights on and off? The capability exists now and is becoming greater all the time.
But Rezabek points out, "fitness for purpose still wins the day. Maybe my iPhone-based PLC is great for flushing the toilets in the truckstop, or even Christmas light animations on my front lawn (It can play iTunes at the same time!), but the large process industries put extraordinary demands on process controls."
Rezabek goes on, "Even in our preferred suppliers' DCS systems, unforeseen 'features' crop up, especially in the portion that's running under common PC operating systems. It can literally take years to run all the bugs into a corner and squash them. The stakes are high—my operations manager says he can justify a $10,000 ultrasonic flowmeter just to improve his odds of choosing the optimum pump to shut down for maintenance.
"It's not just the computing power to invert matrices or solve complex logic and display it all in gorgeous graphics," Rezabek concluded, "It's knowing that it won't do what we don't want it to do, ever, over the course of months and years of 24/7/365 production."
So while convergence of devices, networks and protocols is clearly the way the future shapes up, it will, as usual, take longer to penetrate the process industries.
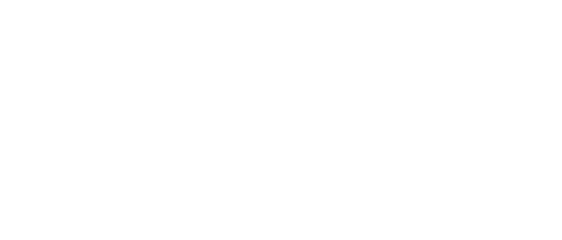
Leaders relevant to this article: