Chris Stearns, senior product manager at Honeywell Process Solutions, says, "We're still in the early adopter phase, but there's momentum here, and it's not going to slow down."
Mobility Drivers
The fact is, says Paul Brooks, business development manager for the networking business at Rockwell Automation (www.rockwellautomation.com), during a phone interview conducted, by the way, on a VoIP connection between Chicago and Brussels, "We are all mobile workers—both the CEO and the technician. You can't constrain where individual workers are going to want information and what information they want to get. And the most important thing is that they want information where they are rather than move to where the information is."
It's not just the perennial attraction to the new and shiny pushing these tools into the process automation workspace. The usual suspects are all there: the drive to do more with fewer workers; the aging workforce and the correlative need to transfer its years of hard-won knowledge to less experienced workers and get them up to speed quickly; globalization that spreads facilities around the world; vital assets and operations in remote locations; and, above all, the demand for greater efficiency and productivity.
The technology to secure your mobile network is there, but it is critical to tailor it to fit your operation's particular needs. Begin by asking some basic questions.
- Why are you enabling mobility plans at your facility? What are your business goals? The answer to that question will determine the rest of your plan.
- How will you define "mobile worker?" Do you mean those working in remote areas of your facilities, or do you mean those at other facilities, contract workers, traveling employees or all of these?
- Who needs mobile access to plant information and what specific information do they need? Security experts recommend asking tough questions about who really needs access and what kind of information and access they need at the start of the project. It is best to start conservatively with strict limits, and then relax them on a case-by-case basis over time
- Is your system configured for secure logons, authorization and authentication? Do users have to prove they are who they say they are and that they are entitled to the data they are asking for?
- Is some of your data best presented in "read-only" format?
- Have you considered encrypting sensitive data?
- Are you going to mandate what mobile equipment employees are to use? Issuing company-mandated phones or computers or allowing employees to use their personal favorite device each presents its own set of management, cost and security challenges.
- How are you going to manage individual devices? How are you going to roll out upgrades? How are you going to disable a device, or at least wipe out its data, if it is lost or stolen or if an employee leaves the company? If employees are using their personal devices, do you have a way of segregating your company data from a user's personal information?
- Do your needs require access to the Internet? Not every industrial mobile application does. A robust corporate intranet may be a much better option.
- If employees are going to have Internet access, do you have a clear acceptable-use policy regarding it? Do your employees know what it is? How are you going to enforce it?
"One thing companies need is improved visibility for edge customers—those out in the process plants," says Kevin Davenport, global solutions manager for industrial automation at Cisco. "Improved decision-making in those places and improved efficiency for field workers [is crucial]."
Charlie Mohrmann, Director of Product Marketing and Strategy, Invensys Operations Management, (www.global.wonderware.com) adds, "Good technology does one or both of these things: Improve a process or sustain it. The two uses with the best ROI are building a high-reliability organization and process improvement. Mobility tools can have a very high payback. Some of these can get payback in six months."
Early Experiments
Already the early adopters are out there trying things out in the field. (See Dan Hebert's "Wireless Workers Unchained," Control, April 2010). Vendors large and small are lining up with large-scale solutions and simple apps to access everything from KPIs to simulations via a cell phone or tablet. Others are offering complex arrays of collaboration enablers, including audio, video, phone and Internet conferencing, all predicated on the notion that no meeting requires all the participants to be in the same room—or even on the same continent—at the same time. Hardware vendors are also stepping up with everything from ruggedized phones and laptops to Internet-enabled video cameras.
Some companies are experimenting, not just with mobile apps in general, but with the iPad in particular. Jeff Sibley, a control engineer at the Dow Chemical Co. in Freeport, Texas, and a member of the Siemens Users Advisory Board, is part of a group at Dow researching the feasibility of using of iPads in Dow's research and development unit.
"We have put all manuals and project documents on them. We also tried hooking them up to a wireless router strictly for commissioning." Sibley says.
Dow's researchers are also experimenting with instructing the control system remotely through the iPad. "Say you have one guy at the operator station telling the guy at the valve to move it. What we're hoping to do is have that one guy move the valve remotely," he says. "We're very much still in the research phase. The software is still wonky."
He also adds that, at Dow, the iPads may be limited to the R& D department. "Project notes and commissioning documents, etc. will be the first use. Also PDFs and spreadsheets. [You can put] lots and lots of information in a very portable form, and they're more convenient than a netbook."
Sibley adds the advantage of the iPad or other tablet over the smart phone is its size. "The problem with the iPhone is that it's small. Things are easier to read on a tablet," he says.
There's an App for That
Aurora Industrial Automation, (www.aurora-ia.com) a system integrator in Portland, Ore., has developed Aurora Mobile Apps, an Apple iPad/iPhone application that gives users real-time access to plant-floor data through Rockwell Automation's FactoryTalk View, ViewPoint and VantagePoint software. Using Mobile Apps, FactoryTalk VantagePoint users can see pertinent KPIs wherever they are. Plant-floor workers working off an iPad can see the same information they would see via the FactoryTalk View application on their PC or inline HMIs.
Even vendors that don't specialize in mobile solutions are making at least pieces of their solutions accessible to "consumerized" tools. Below are some available applications. Just because you don't see your favorite vendor listed here, doesn't mean it doesn't "have an app for that." New ones are being released almost every day.
- HMI/Scada application for supervising variables (tags) and memory of PLCs and RTUs. http://itunes.apple.com/us/app/scadamobile/id324515280?mt=8
- Counterpoint Intuition Mobile provides real-time remote access to production data and KPI information directly on your iPhone. http://itunes.apple.com/gb/app/intuition-mobile/id418126639?mt=8
- Canary Labs' Canary Mobile for smartphones uses graphical web page applications specifically designed for viewing on smartphones, including the iPhone, BlackBerry and Droid. http://tinyurl.com/4kyuvrr.
- Emerson Process Management delivers data from DeltaV Mobile Platform v10/3/1 and Syncade Suite, which can be accessed from smartphones and other mobile devices. www2.emersonprocess.com.
- ExperTune's PlantTriage real-time process variable trending data is accessible on mobile phones. http://www.expertune.com/plantTriage.html
- Honeywell's Mobile Station is at http://tinyurl.com/4dlrmab and Intelatrac PKS is at http://tinyurl.com/4qt63eq
- Invensys Operations Management has mobile applications for its IntelaTrac (http://tinyurl.com/4vcdt2y) and its EyeSim simulation software (http://tinyurl.com/4la66xd).
Rockwell Automation and Meriduim will jointly release a tablet app for Rockwell's Plant Baseline parts management system in May. - Siemens offers a WinCC/AddOn for its Alarm Control Center for fast and reliable alarms in the event of faults. http://tinyurl.com/4ovcy3y
- Transpara's Visual KPI for mobile phones including Apple iPhone and iPod Touch, Palm Pre, Android phones, Blackberry and any mobile device with a modern browser. www.transpara.com.
Not So Fast
Having said all that, bringing smart phones, laptops and tablets on to the factory floor also brings a load of problems that have to be addressed before they will live up to their potential. The Big Three are security, safety and ruggedness.
Security is arguably of the most concern. As Sibley puts it, "Security needs to be much better. You can live with [a mobile device] not being ruggedized, but not with lack of security."
You can, of course, simply refuse to play the game says Honeywell's Stearns. This is the easiest, simplest way to handle the issue, and many companies do just that. No wireless. No Internet connection. No mobile devices. Period.
But that attitude may also be a last-century artifact. "Security by obscurity is a myth," says Cisco's Miller. "What most smart folks have figured out is that what we can do today costs less and is more secure than what we were doing previously."
The good news is that while securing these mobile systems is not necessarily simple, it is also doable, and many of the best proven techniques are already out there.
Ian Nimmo, president of User Centered Design Services (http://mycontrolroom.com) adds, "We've already fought the security battle. If companies have appropriate security in place for other things, it will also work for cell phones, netbooks, etc."
Neil Peterson, senior manager, wireless marketing at Emerson Process Management (www.emersonprocess.com), says, "You can be as secure as you want to be. Security is highly configurable. [The question is] how much effort do you want to put into this."
One problem is that no one solution fits all. "Every company is so far different because there are so many ways to skin the cat," says Michael Saucier, CEO of Transpara, maker of the Visual KPI application (www.transpara.com). Deciding your preferred method of cat-skinning can take a lot of time and effort.
The other stumbling block for process operations is safety. As cool as they are, smart phones and tablets are not explosion-proof or non-incendive. This fact will limit—at least for now—the use of smart phones and tablets in the plant.
But that limitation may be temporary. Mobile software will offer a way around some of these problems. "One of the things driving this is the common operating systems and the applications written for them," says Cisco's Miller. "It's going to be easy for developers to put them in a form factor that can be used." In other words, it's only a matter of time before somebody builds a mobile device useable in explosion-proof, non-incendive and corrosive environments.
Even now there are workarounds. Bossard says that while there are places he wouldn't take an iPad, "We have a few options even in wash-down areas. It's not the most attractive option, but you could use a zipped plastic storage bag. You can also get very hard neoprene exterior skins with the inner part made of a softer rubber." And ultimately, he adds, "As long as the device isn't going to interfere with safety it should be OK in about 75% of applications."
And there are always the ruggedized laptops. Panasonic has been selling its Toughbooks (www.panasonic.com/business/toughbook/laptop-computers.asp) for years. At least one model, the 29s, is Class 1, Div 2-certified.
Stone Energy of Lafayette, La., equipped its offshore oil rig workers with Model 29s Toughbooks to give them real-time access to sensor information near the drill bit.
Dave Kennedy, Stone's director of information technology, says, "Having the Toughbook connected wirelessly to information systems behind the drill bit facilitates real-time decision making. That information can translate to the accelerated completion of operations and huge cost savings."
Courtesy Cisco Systems. Copyright 2010, Cisco Systems
And not every plant-floor situation will require these ruggedized or specially certified units. "The consumer market is far bigger than the industrial market," observes Rockwell's Brooks. "There's a huge cost benefit in using consumer devices because of the size of the market. If you have a $300 netbook with a virtual desktop accessing information off a server, and you drop it, you lose a $300 netbook. Compare that to the price of a Toughbook. There's going to be enormous pressure to use the consumer model. That doesn't override the safety issues, but it does create a pressure and a dynamic."
Taming the Beast
Integrating smart phones and tablets into your operation is in many respects no different than any other project. Begin by having a clear idea of what it is you want to accomplish, adds Brooks. "Focus on the objectives. You can't afford to deploy it just because it's cool technology. You do it because there's a real business advantage."
Invensys's Mohrmann adds, "First decide what process improvement you want to make. See what others have done. Then get a scope to the project. Go about it in a step-by-step way."
Then focus on the risks. Bob Huba, DeltaV product manager and cybersecurity expert at Emerson, says, "Make sure that people understand the dangers. They need to understand how [mobile access] can create problems."
Emerson's Peterson adds, "Map the solution out. Lay out the architectures. Configure everything and roll out the solution in a methodical fashion. Then check it out after it's done. You can absolutely do a secure system. It's really a matter of coordinating a good plan and then executing it."
You will also need a holistic view of your wireless operation, says Brooks. "Spectrum is a finite resource. It's a shared medium, and you need strong policies and procedures to control access. That may be the single biggest challenge. You have to have an integrated wireless network, because isolated ones don't work."
Which brings us to the knotty problem of the relationship between your operations and IT departments. You can't successfully bring these mobility tools on to the plant floor without some input from IT. "There's going to be some resistance on the part of IT," says Honeywell's Stearns. "The IT group has to be the enabler. The control system might look at everything below Level 2. IT might not even care about that."
"You need to get the decision-maker on the operations side," recommends Transpara's Saucier. "IT often wags the dog and doesn't want to do the security to make these tools available. In companies that have embraced the idea that IT is a support function, there is no push-back."
Consider starting small. Take a page from Dow's playbook and try out a pilot project in one area. "Try to roll it out in part of the plant. See if it meets your objectives. Then roll it out elsewhere," recommends Cisco's Miller.
Or look for an easy win. Western Power, an Australian electricity provider, gave Blackberries equipped with Transpara's mobile application to 1100 technicians in trucks all over Western Australia so they could better monitor their substations. The entire rollout went from prototype to use in one week, according to Saucier.
If Not Now, When?
So, you're not ready to wrap your head around iPads on the factory floor and Android phones for all your engineers? Well, you can hold out, of course, but you may have to cave eventually.
"This is looking like a when, not an if. There's going to be a plethora of innovations," says Brooks. "In manufacturing, we are going to have to have solutions that allow things to be displayed on iPhones and Blackberries because their usefulness has been proven. We can't stop these commercial devices coming into the manufacturing zone. People will find ways of using them if they make their jobs easier. It's better to work with disruptive technologies rather than block them. People will accept ‘yes, but,' but typically, they won't accept 'no.' "
Nancy Bartels is Control's Managing Editor.
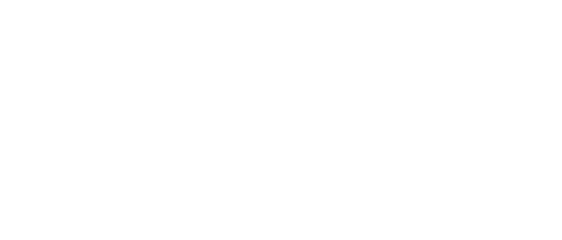
Leaders relevant to this article: