The same scenarios play out every day in control rooms around the world. From the start, little thought has been given to human factors in the design of the operator stations, and even less to the user interface design. Operators are well oriented to "normal," steady-state plant operations, but are untrained and ill-prepared to deal with abnormal situations when they arise. This even includes scheduled shutdowns and start-ups that today happen at increasingly infrequent intervals. And, all too often, the information operators need to make quick, intelligent decisions does not exist within the operations environment—requiring operators to juggle other system interfaces at the precise moment the process itself demands their undivided attention.
Is it any wonder that operators' inability to deal with abnormal situations is responsible for enormous losses of productivity, money, and even life and limb across industry? Indeed, research indicates that nearly 80% of production downtime is preventable. And half of this is due to operator error. The monetary costs of this failure in the petrochemical industry alone are estimated at $20 billion per year. And with the financial impact of an unplanned production outage averaging $250,000 per hour, the incentive to improve operator effectiveness is not to be ignored.
Four Pillars of Operator Effectiveness
Together with the design of more intuitive user interfaces and more ergonomic operator stations, the integration of disparate plant systems within the System 800xA Operations environment is central to ABB's approach to helping the process industries improve its operators' effectiveness. These three pillars—high performance human-machine interface (HMI), attention to human factors/ergonomics and plant system integration—are complemented by a fourth: the assurance of operator competency and confidence through training on integrated simulation environments.
The key deliverables of this integrated approach to operator effectiveness include:
- Increased asset utilization: Equipment utilization and overall equipment effectiveness (OEE) can be improved through efficient alarm management strategies, which can help to reduce nuisance alarms, rationalize existing alarms, handle alarms dynamically, design alarm sounds properly, and provide a means to monitor the alarm management strategy itself. An alarm management system designed with integrity allows operators to truly operate instead of just reacting.
- Improved performance: Control room ergonomics and design have a big impact on operator effectiveness. The planning of areas adjacent to the control room needs to take personnel movements and workflows in consideration. Also, with control loops tuned and running in a consistent, automatic mode, the process will perform better which increases output and quality.
- Improved safety: With more effective operations strategies in place—including alarm management, operator training and loops running in correct mode—the overall safety of plant personnel will improve.
- Improved collaboration: With systems seamlessly connected and transparent to operations, relevant information and data can be shared, encouraging a collaborative and productive environment.
Integration Is Fundamental
ABB's approach to integrated operations is founded on the inherent integration capabilities of the System 800xA, where the operator works in a seamless environment with vertical, horizontal as well as functional integration. Vertical integration gives the operator access to all information relevant to plant operation such as production orders, production reports and financial performance. Horizontal integration gives the operator detailed access to all types of devices and all types of control systems, independent of brand. Functional integration makes functions located in separate systems, normally not related to automation, available in the seamless operator environment. Examples include live video, maintenance management, laboratory systems and document management systems.
Swedish papermaker Södra Cell Mörrum is among those companies using ABB's object-oriented architecture to access mission-critical data while preserving their existing control system infrastructure investments.
From an operations perspective, the 800xA Operations applications extend the reach of ABB's Process Portal to provide a single, consistent and intuitive window into all the applications encompassed within the Extended Automation environment. It allows users of all disciplines that impact production to organize information and navigate throughout the system in the context of their job function. The system, by virtue of the ability to associate all aspects of information available from the various applications within the system to the appropriate process object, allows for quick and intuitive analysis. The Extended Automation system environment also streamlines work processes and communication among various functional disciplines.Personalized workplaces ensure that operators and other personnel are presented only with the information needed, in the proper context. The design of the environment provides intuitive and easy access to all integrated information through a simple right mouse-click on each object. Navigation is simple and independent of where the information is located. Information displays can mix-and-match any combination of data sources that are part of the 800xA environment. The operator can be presented with consolidated alarm and event lists, for example, without needing to know what application or controller supplied the information. Since it is all available in one place, troubleshooting becomes much easier.
Implementation of standards in the areas of display design (such as from the ASM Consortium, EEMUA and ISA), enable operators to perform effectively no matter what is happening in the plant. Workplace layouts are adjusted and optimized to users' preferences and needs with individualized menus, toolbar contents and display locations. Windows management functions such as safe areas and the pinning and stacking of priorities minimize operation errors by prioritizing the presentation of material.
Ergonomic Factors Boost Alertness
Instead of being designed with operator performance in mind, many control centers, control rooms and operator stations are designed without respect to human factors or simply to impress visitors. Incorrectly planned environments intended for 24x7 use often are depressing, unwelcoming and uncomfortable at best—and at worst create fatigue and boredom.
ABB's Extended Operator Workplace (EOW) is intended to create an ideal work environment for the operator, including the operator station functionality within the control system as well as the surrounding environment.
ABB has been focusing on human factors for many years, and works closely together with CGM, specialists in control room design and ergonomic work environments. Together, ABB and CGM have turned fatigue and distraction into operator alertness and pro-activity with an offering called the Extended Operator Workplace (EOW), which aims to create the best work environment for the operator, including the operator station functionality within the control system as well as the surrounding environment. Exclusive to ABB, the EOW provides a modern control room or control center that promotes more alert, less stressed, happier and much safer operators.The high-end EOW-x contains the latest flexible motorized console technology adjustable to individuals at the touch of a button. Included is the Advanced Operator Keyboard that includes hotkeys for easily switching between different System 800xA screens. In the motorized, large overview unit, a directional sound system as well as a high frequency dimmable lighting system is integrated. The console also has a live video camera system with speaker system for public announcement. "Micro ventilation" capabilities even allow each operator to personally adjust ambient temperature conditions.
A Competent Operator Is a Confident One
Finally, the assurance of operator competence through proper training also is affected by integration factors. A closely integrated training environment, for example, makes it possible to train operators on simulators that behave essentially identically to actual plant systems, instilling confidence that operators can respond correctly to abnormal situations when they arise. ABB provides custom simulator solutions to most types of plants using the System 800xA Simulator, a simulator version of the standard System 800xA.
For a new plant, use of an operator training simulator can contribute to shorter initial start-up, enhanced operator performance as well as trip and incidence avoidance. It also allows the testing of operational procedures and the tweaking of display and control strategies before initial start-up, when changes are less risky to make.
Operator training simulators also are important to the effective operation of existing plants. Many high-reliability plants are having difficulty maintaining performance during turnarounds because workers deal with these procedures only infrequently. And the ongoing retirement of experienced operators has only made this situation worse.
While the direct benefit of using a simulator is difficult to quantify, a recent survey by the Electric Power Research Institute (EPRI) indicated an average yearly saving of about $4,500 per megawatt of generating capacity. These savings are attributed to reduced training costs, improvements in plant availability, fewer environmental excursions and reduced damage to equipment. A little bit of math indicates a three-month payback for the typical power generation facility and begs the question: In what scenario would you not invest in a training simulator?
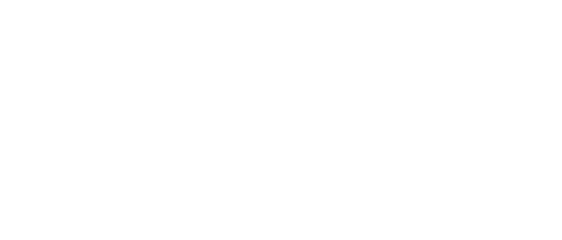
Leaders relevant to this article: