Certified fieldbus trainer David Lancaster of Angola, Indiana's Trine University posed the question the other day, "Does freedom-to-choose/power-to-integrate mean that you're more comfortable specifying "or equal" when procuring fieldbus devices?" Even in the days of 100% 4-20 mA devices, few end users were happy rolling the dice with an "or equal" statement in their project's procurement requisitions.
I've heard that emerging fieldbus standards once spurred fears that "differentiation" would cease, and that field devices would become near-commodities. So does the fieldbus "checkmark" confer some level of uniformity that minimizes the unique capabilities of one vendor's offering compared to another? Have fieldbus users entered an era where they can safely allow virtually any device vendor to compete for their business?
If this were the case, then one would expect the simpler devices would show evidence of this commoditization more readily than complex ones. Temperature transmitters perhaps?
There are over 20 temperature transmitters (not counting muxes) from 14 different manufacturers registered by the Fieldbus Foundation. Some are the head-mounted variety. At least three of these have dual-sensor capability, and some of those have "hot backup." Some of the larger versions that offer hot backup require an analog input (AI) function block for each sensor and a separate input-selector block to perform the hot backup. Others can do hot backup in a transducer block, minimizing its "macrocycle" schedule footprint—one function block instead of three.
And, the function blocks themselves aren't equal. One can execute its AI function block in 50 milliseconds; another can do it in half the time. One has a repertoire of function blocks—several AIs, PID, ARTHM (arithmetic), Signal Characterizer (SGCR); another only a couple AIs and a PID.
All these transmitters appear to be capable of handling the full array of thermocouples, RTDs, millivolt and resistance measurements. All carry a wide array of hazardous-area certifications. Some have local indicators.
Considering the substantial differences noted above, what's the chance your competing lube oil skid suppliers will end up choosing something familiar?
Toward the other end of the complexity and cost spectrum are valve positioners. I agreed to use a couple valves from a leading supplier that differed from our plant standard. The supplier has a fieldbus positioner offering that is in at least its fourth iteration, and is to all appearances a solidly built fieldbus product. These were self-contained regulator replacements, so I thought some fast cycle times would be beneficial. After cleaning up the macrocycle schedule (getting rid of several "publish" or compel data events that could become asynchronous), I was a little dismayed when the DD (device descriptor) revealed that function blocks (AO & PID) in the positioner would take over 215 milliseconds. This compares with about 35 to 45 milliseconds for our plant standard. I would have to settle for a 500-millisecond macrocycle.
The positioner vendor was nice enough to include methods (think "wizards") for setup and calibration. Since we had changed the fail position and action of both (fail open/closed), we were happy the procedure was similar to the positioners we had in abundance. But later, when the loops were put in service, we had a rough time getting the tuning to work. It wasn't until we changed our default setting of the AO (analog output) block—using actual valve position for PID feedback—and effectively turning off integral action that we started to see good performance.
All is well now, but ventures into the land of "or equal" may not be for the anxious novice or irritable veteran. Standardization and uniformity may cost the project more, but will pay some dividends when the heat is on to deliver the completed job.
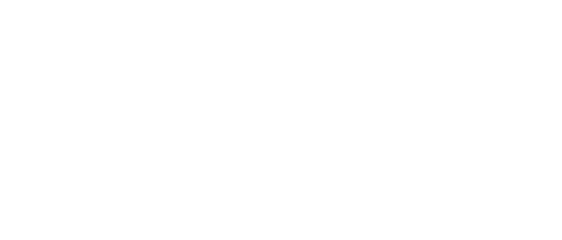
Leaders relevant to this article: