Global warming may one day turn Milwaukee into a tropical hotspot. But for now, most of its downtown area by Lake Michigan will keep needing the steam heat it gets from We Energy's Valley Power Plant. This huge plant is the largest utility-owned co-generation facility in the U.S. It includes two 280 MW units, and its four coal-fired boilers produce 1.25 million pounds per hour (MLb/hr) of steam.
In the decade of its continuing mission to provide and improve its service, Valley Power has steadily transitioned from using stand-alone laptop PCs and multiplexers, and moved "piece by piece" to using Emerson Process Management's online AMS Device Manager and its Ovation interface. This journey was described in "A Power Plant's 10-Year AMS Saga" presented by Todd Gordon, We Energy's instrument technician leader at Valley Power, this week at the 2010 Emerson Global Users Conference in San Antonio, Texas.
"Now, we all have to love technology, but we know that it also can create an overload unless training and implementation are coordinated, and it can be underutilized for the same reasons," Gordon said. "We've also learned that technology such as AMS can't solve every problem. Field devices still have potential for mechanical issues. If your hardware and mechanics aren't set up properly, then your overall system isn't going to work. Technology is only as good as the people that maintain and use it and interpret the data, and so it also takes a commitment of time for training, proper setup and implementation."
Built in the 1960s, Valley Power initially used local, pneumatic controllers for pressure, temperature and level. Gordon reported that the plant's journey to AMS really began when it installed its first "smart," non-HART transmitter in 1988, which had a proprietary communications protocol. Also, the plant ordered its first 268 HART communicator in 1992.
In 1993-94, DCS controls were installed at Valley Power. Likewise, in 1993, the plant gained its first "smart," non-HART positioner, and it too had a proprietary communications, as well as a DOS-based, menu-driven software that ultimately required the plant to retain a Windows 98 laptop. More smart positioners were installed in 1999, and the plant also added Rosemount 3095 multi-variable flow transmitters and Fisher DVC 6010 positioners. "The main question along the way is, Can the newer smart instrument do its primary function better than the older technology? And we've usually found that the answer is yes," Gordon said.
Then, in 1994, the plant added documenting calibrators for more consistent calibrations and paperless reporting, which improved record-keeping for insurance and regulatory audits. "We also used the HART communicator to adjust the smart transmitters, and we got better accuracy," Gordon said. The plant has grown through several earlier versions, and now uses the 475 HART communicator.
To fight initial misperceptions that Fisher's DVC valve positioners might not be as accurate as Fisher's pneumatic valve positioners, Gordon compared the two side by side. He reported that the pneumatic positioner has ±2% accuracy, a maximum output at 20 psi of 165 standard cubic feet per hour (scfh), and a maximum supply pressure of 50 psi. Meanwhile, the DVC had ±0.25% accuracy, maximum output at 20 psi of 375 scfh, maximum supply pressure of 145 psi, and an automation travel calibration feature for stroking valves. "Fisher DVC positioners also provided an input to DCS for valve position from the HART signal. These were on our two most critical valves," Gordon said. "So when the positioners told us the valves were getting sticky, we decided to replace them, and this saved us from tripping out units three times."
'All of this has been a journey, not a destination.' We Energy's Todd Gordon described his company's ongoing evolution in asset management capabilities at the 2010 Emerson Global Users Conference.
As the years passed, Valley Power also began to use its newer technology prowess for maintenance adjustments. For example, packing nuts in slide steam valves need to be tightened to pre-loaded tension levels, and the DVC tools allow Gordon and his staff to monitor—both online and offline—the friction in the valve stems through those packing nuts, and even perform valve bench-setting. "This was helpful because sometimes guys would tighten the nuts to triple the required friction, but we could then check online, and make the right adjustment," Gordon said.In 2004, Valley Power added Base Station with Multiplexers (MUX), which enabled online continuous monitoring when hardwired to HART devices. Also, multiplexers can be daisy-chained together at 32 points per MUX. In this case, non-hardwired HART devices in the database were connected with the handheld HART communicators, and data was then uploaded to Base Station. The plant staff also used mini-grabbers, banana jacks and other methods of connecting to their HART devices. "The base station communications from the handheld and laptops have been very useful, but sometimes we still like to go out and see the valves move," Gordon added. "There are still some things you can only see when you're there."
More recently, Valley Power implemented Batch Runner software, which allows multiple tests to be run automatically, and also ensures more consistent results. Likewise, the software's Online Device Manager allows the ability to set up multiple valves and find problematic equipment. For example, Gordon reported these tools, such as air mass flow tests, have allowed him and his colleagues to identify bad diaphragms in soot blower regulating valves that were running at more than 300 scfh because they'd stiffened and cracked over time, and so were losing a lot of air. They were replaced with new diaphragms that run as less than 3 scfh.
In 2005, the plant added newer documenting calibrators with HART communications, so it no longer needed separate HART communicators for calibrating its smart transmitters. "We also now have online links to maintenance procedures and manuals, online maintenance history, and can generate pro-programmed reports in Microsoft Word," Gordon said.
In addition, due to a 2008 outage, Gordon connected smart pistons and positioners to remote-mounted DVCs to replace four old damper drives. As a result, unacceptable triple-digit friction levels dropped back to acceptable double-digit levels.
Most recently, the plant replaced its multiplexers with Emerson's Ovation interface, and spent part of this year working on a new DCS controls upgrade, in which the base station will be integrated into the DCS controls. In fact, We Energy has built two new power plants that use AMS for their valves, DVCs and other equipment.
"In general, our performance monitoring had given us better tuning of controls, improved heat rates for reduced fuel consumption, faster ramp rates for changing load demands, centralized performance monitoring, and predictive maintenance," Gordon said. He said that business results achieved at Valley Power over the past 10 years include:
- Better field signal inputs and final drive control
- Valve position feedback using the HART signal, which is very cost-effective compared with buying a separate valve position transmitter
- Enhanced maintenance capabilities
- Offline diagnostic testing capabilities
- Online diagnostic capabilities
- Ability to upgrade hardware, firmware and software
- Interfacing with all HART-compatible instrumentation
- Remote access to HART field devices
- Alert Monitor, which allows for continuous monitoring
- Batch Runner and Scheduler routines, which enable repetitive functions to be programmed and run consistently.
"Existing plants can upgrade equipment over time to take advantage of the features of smart field instruments. Computerized control systems need better field device inputs. Otherwise it's garbage-in-garbage-out," Gordon said. "All of this has been a journey, not a destination. As technology improves, you need a system that can grow with it. We found that online capabilities increase the effectiveness of smart instrumentation and supporting software. However, you can't maximize a plant's efficiency if you can't accurately control and effectively manage the final drive elements."
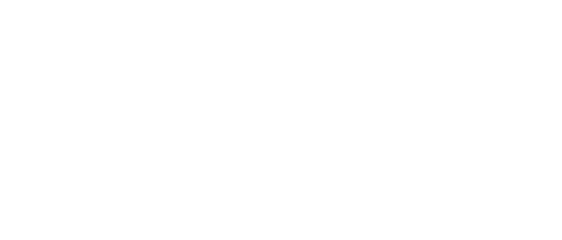
Leaders relevant to this article: