By Nigel James
Control system migration projects go better with best practices. This is not a place you want to be flying by the seat of your pants. The following is a guideline for consistent and accurate planning and execution of control system migration projects. Adopting these practices will reduce project costs, shorten the project schedule, and reduce risk. These practices will also improve plant operation after the migration, particularly in the area of operator efficiency.
Selecting the New System
Once the decision is made that a new control system is needed, the next challenge is to determine the best one. The first rule of thumb is to not allow the selection process to become an emotional debate. Fortunately, there is a specific process that can reduce the subjectivity of the selection by prioritizing needed control system functions and features.
The first step is to build a list of selection criteria. These can range from vendor technical support to HMI features. The designated decision makers should then prioritize these criteria. Assign a weight or use a multiplier to determine prioritization. A matrix of these criteria with weighting factors should then be used to populate the vertical axis of a decision matrix. On the horizontal axis, the various control systems being considered should be listed.
An example is shown in Table 1. A weight of three indicates highest importance, while a weight of one indicates lowest importance. Each vendor is ranked against each criterion on a scale of one to three, with three indicating best performance and one indicating worst performance. Each criterion weight is then multiplied by each vendor’s ranking, and these subtotals are added to determine a total score with higher numbers indicating better performance.
Gathering information to rank each control system can be challenging. Corporate engineering groups, engineering firms or independent system integrators are a good choice for assimilating this information because many times facility end users do not have detailed technical information on a variety of vendors. The vendors themselves are not unbiased, and tend to only provide the upside of their products.
Once this data is gathered, populating the remainder of the matrix with scores is the next step. After this is completed, a quantitative score is achieved, and the highest quantitative scores represent the control systems that will best satisfy end-user priorities. While this process is subjective in terms of prioritization of criteria and applying rankings to control systems, it generally reduces debate, documents the decision-making process, and helps a facility or company determine priorities.
Front-End Project Definition
A requirement for successful migration projects is a thorough up-front engineering study to define the detailed work scope, and estimate the overall cost of migration. It’s not enough to take an educated guess at the requirements and costs of a migration project, hope for the best, and immediately move to the full engineering phase.
Migration projects are often much more complex than they appear at first glance. If done correctly, a Front-End Loading Study (FELS) should identify any potential difficulties with a migration project, and should provide plans to mitigate risks.
Why Migration Projects Fail
|
The granularity of the FELS will determine if additional deliverables are needed, and to what level the estimate and scope of work are detailed. The goal of this effort is not to complete detailed engineering, but to verify and quantify all primary functions on a project.
Engineering/Procurement/Construction Checklists
One of the reasons that migration projects often fail to address key components during the engineering phase is that these projects typically occur at 10-15 year intervals. Because they are not common projects, there is less knowledge of some of the hidden gotchas, making it imperative to use comprehensive migration checklists.
Engineering and system integration companies that have these checklists available are often a good resource for the engineering services needed for a migration project. Checklists provide for consistent design and improve overall quality. The checklists serve as information gathering tools to assist in developing a comprehensive scope definition for a migration project.
Detailed Cutover Planning
An effective detailed cutover plan addresses the following questions:
- What methodology is going to be used for cutting individual I/O over to the new system?
- In what sequence is I/O going to be cutover?
- What adjustments will operations need to make during the cutover?
- What staff is required for the cutover?
- What is required from a checkout standpoint to call a point migrated?
The cutover portion of a project is typically the most visible aspect of project execution. The decision to perform a hot cutover or use a window of outage time is always the primary decision that determines the details of the cutover plan. Regardless of plan is used, the cutover plan should at a minimum include:
- To/from wiring termination schedules
- Daily cutover plans
- Third-party device considerations
- Loop check spreadsheets or folders
- Written cutover methodology.
The consideration of the sequence of cutovers is most critical when systems must stay in operation. In this scenario, there are typically intermediate operator consoles for parallel operation. Planning must include consideration of temporary power requirements and temporary locations for panels and/or consoles.
An area not commonly addressed to an adequate level in cutover planning is third-party device communications. The details involved in migrating serial communications can often be very complex. Whether the communication is a serial RS-232 connection to a weigh scale or a redundant Modbus communication to a triple-redundant shutdown system, the impact of migration to a new control system must be researched in great detail in advance of actual cutover.
Keys to Success
|
Good migration cutover plans include individual third-party device cutover plans. Quantification of points, types of communications protocols, specific driver compatibility issues, data mapping requirements and operating system version compatibility should all be defined.
Detailing all aspects of a cutover early in a project will pay great dividends in streamlining cutover time, cutting costs and reducing overall risks.
Intermediate Operability and Training Plans
A common challenge for migration projects is establishing parallel operation of the old and the new control system as this is often the operators’ first exposure to the new system. There are a few items that must be addressed.
First is consideration of how to physically layout the new control system without interruption to the existing operating environment. This is challenging as most often control room space is limited. As parallel operation begins to occur during the cutover process, consoles must be in close relative proximity and/or additional operating staff must be used to supplemental plant operations on a short term basis.
A second consideration closely integrated into the cutover efforts is determining the sequence of units, processes and/or systems to group and cutover. For example, if a reactor is going to be cutover to the new system, then it is essential to plan the conversion such that the operator is only required to utilize two systems to operate the reactor for a minimum amount of time.
Another consideration is the overall operator training plan. One of the questions is when to start the operator training. If the training is done well in advance of cutover, then it often proves less effective. However, training during the cutover also doesn’t work well due to distractions.
A better method is to train a core group of operators and make them part of the cutover team. The training for the general population of operators then takes place after the cutover and involves additional training by the core operator team.
The type of operator training is often a source of discussion as well. Formal operator training may not provide technicians with adequate hands-on application specific training. The type of operator training selected comes down to personal preference of the company, but one suggestion is to establish a combination two-level operator training plan. The first level is basic skills, navigation, and system familiarity training - similar to formal vendor training. The second level is application specific training that utilizes actual plant processes, graphics and alarms.
Migration projects are challenging, but can deliver great value to end users. The process used to arrive at migration timing and scope has considerable influence on whether that value is actually achieved. The most critical consideration is detailed up-front planning because it lowers risks in the execution phase of a project.
It is generally not the obvious portions of the scope such as configuration of the new system that creates issues for migration projects. Instead, less obvious areas such as infrastructure, HVAC capacity, power limitations and third party device integration cause unforeseen problems. When approaching control system migration, consider the application of these best practices to lay the groundwork for a successful project.
Nigel James is president of the Gulf Coast division of Mangan Inc., a system integrator in Lake Jackson, Tex.
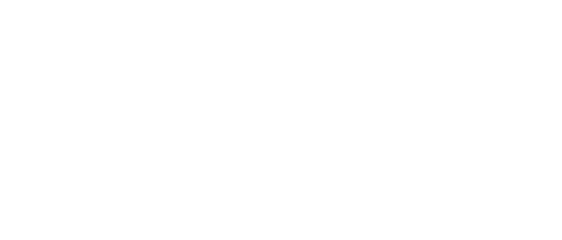
Leaders relevant to this article: