By John Rezabek
Our sister publication, Chemical Processing, sent me an alert the other day about a new feature for Micro Motion Coriolis transmitters from Emerson Process Management. Its latest offering now natively supports DeviceNet and Profibus DP, and already had supported HART 4-20 mA, Modbus and wireless.
If the mythical Tower of Babel had implemented an industrial network, I think 21st-century controls professionals could have provided the design and troubleshooting. Thats because it appears that our supplier community is gearing up for a diverse spectrum of interconnection options, instead of the global standard once envisioned for IEC 61158.
In the late 1980s and early 1990s, end users were eager to connect dissimilar systemsDEC Vax-based historians, tank-gauging systems, analyzer networks or minicomputers running model predictive controlsto their DCSs. Anyone remember the ISA show with the dinosaurs wearing CRT glasses? Microprocessor-based instruments, or smart transmitters and valve positioners, were introduced at the same time. Modbus was the de facto standard, as well as the path by which DCS vendors proclaimed their systems to be open. We were already imagining what could be gained by connecting the microprocessors in field devices directly to the DCS, when Honeywell delivered DE. End users and Honeywells competitors agreed that a proprietary solution for a digital field network was not in anyones best interest, and work on a digital replacement for 4-20 mA began.
Twenty-five years after the first digitally integrated transmitters were introduced, theres still debate as to whether any clear standard ever emerged. The Fieldbus Foundation (FF) says it has the standard. Meanwhile, the Profibus Trade Organization (PTO, us.profibus.com) says it won the Fieldbus Wars, citing staggering numbers of installed nodes. And some say the smart money is on Ethernet because its ubiquity may overtake all the rest.
Laggards, Late Adopters and Installed-Base Inertia
WirelessHART and ISA100.11a appear to continue their non-interoperable competition for the wireless standard. It appears the vendors havent learned this lesson from their previous wars and need to learn it again, says Bill Hodson of Hodson Consulting LLC in Philadelphia, who is working on a Foundation fieldbus high-speed ethernet (HSE) gateway for Wireless HART. User enthusiasm for fieldbus in the 1990s was similar to what were experiencing with wireless today. And like today, deep divisions, split loyalties and competitors refusing to concede any ground to one another, delayed any standard for years.
Ten years after the first pioneers installed early incarnations of fieldbus on the North Slope of Alaska and elsewhere, the main playersFoundation fieldbus, Profibus and HART (implemented as a device digital integration strategy)are still in the minority. How is it that a technology that was so pined for in the 1990s isnt a no-brainer today?
We Dont Need No Stinkin Diagnostics
Fortunately, while the Fieldbus Wars were raging, users didnt hold still. A significant number continued with DCS and field instrument upgrades when the capital was available, using the technology of the day4-20 mA and proprietary protocols like Honeywells DE. Unfortunately, the systems installed werent well-equipped for integrating the upcoming fieldbus options, including HART.
In many sophisticated plants, the value of control systems had visibility well into the executive ranks. These plants staffed up and maintained organizations needed to keep the plant running optimally. Advanced control and optimization strategies rely on measurements being timely and valid, and control valves going to the requested position.
When management understands the value of its control system, resources tend to flow as needed. The other day at our International Specialty Products plant, we had a chromatograph service tech whose friend just landed a great-paying job in a Gulf Coast refinery. The plant manager there had decreed, Analyzers will have 98% or better reliability, and they hired the people they needed to get it done with the kit they had on the ground. Once in place, an experienced staff will excel with what it hasand for many sophisticated users it isnt fieldbus.
Before any of us had a digitally integrated smart valve, we had some great diagnostics generated by the organization itself. Experienced board operators possess lot of good diagnostics embodied in the phrase, I dont believe this transmitter. And, in less-dysfunctional organizations, they communicate as much to the instrument department. When you add to this a staff of advanced control and optimization professionals whose duties include daily scrutiny of the effectiveness of their applications, your ability to detect and even predict deficiencies in the measurement and control infrastructure becomes fairly comprehensive.
Weve also had at our disposal diagnostic tools in the form of tuners and historian analysis tools. ExperTunes Plant Triage and ControlSoft's Intune+ can analyze standard analog 4-20 mA signals from old-school DCSs and identify many issues with measurements, positioners and controller tuning. Gensym-based expert systems like Nexus Solutions can offer even more standardized and customized diagnostics based entirely on olde-tyme analog signals. Rudimentary rules such as, If this pump is running FT-101, should show no flow, or If the valve is 30% open, the flow should be can be implemented without enormous effort.If Its a Clone, Leave it Alone
This is a saying I learned from a friend at a major engineering procurement contractor in Kansas City. With pressure from our project managers and the finance community that bankrolls them to keep costs down and accelerate the schedule, the desire to innovate with digitally-integrated field devices is sometimes deferred. I just received an estimate from a specialty valve manufacturer to retrofit a fieldbus-capable positioner to its product for more than three times what the same product costs me. That skid suppliers discourage their clients from deviating from the cookie-cutter product they like to sell is nothing new. Shell Oil overcame this for its Malampaya deep-water gas platform and pipeline, but many of us dont have the kind of leverage Shell can bring to the table. Faced with these increased costs and delays, we often relent and take the default, usually bottom-of-the-line instruments.
There was a time when speed of execution for oil and gas production projects valued speed over innovation, but theres evidence this is no longer the case. However when backlogs at the suppliers are high, and youre told that will add two weeks to the delivery, you might be compelled to take the conventional alternative. No one gets fired for specifying 4-20 mA, at least not yet.
And when youre the subcontractor trying to win the lube-oil skid job on another third-party suppliers compressor, the diversity of bus technologies such as 4-20 mA and the lack of any global standard make it difficult to propose more than the rudimentary instruments you put on the last one.
We Cant Maintain What We Have
On the other end of the spectrum from the 1st-quartile refinery are those whose staffs have been cut to the bone or those where attrition continues unabated with few new hires to fill the ranks. Weary baby boomers in their 50s and 60s arent anxious to add complexity to the alligator-filled swamp they pull into at 7 a.m. each business day. And, since adding fieldbus or native HART capability to your DCS means ripping out what you installed only 10 or 15 years ago, the cost and disruption to plant operations can be prohibitive.
As one end user reports, One of the institutional roadblocks is having to install a new DCS, and if your DCS has lots of life left, then its very difficult to justify Foundation fieldbus.
The pilots of our process plantsour operatorsoften arent anxious to learn any new tricks either. Finally, our host suppliers have at times been slow to adapt their products to support fieldbus and native HART. Even today, you cant easily paste a new DCS that supports fieldbus or native HART to what you have on the ground. Anyone doing an expansion is faced with either installing the soon-to-be obsolete technology of the 1990s or essentially switching to a completely new DCS.
Another end user, now in the throes of appending his DCS vendors new system to the old, says that, If youre planning to upgrade your DCS, dont assume your current vendor is the best choice just because you have a good track record with them. Open systems are destructive technology, and its not surprising that some vendors have a hard time adapting. Staying loyal to the supplier of your legacy installed base may be as painful as a new DCS.
Profibus Serves Breakfast, Lunch and Dinner
Before the fieldbus wars, German automation leaders asked for a standard digital bus for discrete settings such as automobile manufacturing. Profibus was created as an upgrade from Modbus and a proprietary protocol for integrating discrete devices. Lots of purple hose was installed, and North American users of Texas Instruments legacy 505 and 545 PLCs found many uses for the gaily colored cable as well.
When real fieldbus solutions for the process industries, like WorldFIP and ISP, began to gel, Siemens and other European PLC makers that supported what we now call Profibus DP already had a large installed base. When it became apparent that Foundation fieldbus would likely mean drastic changes for their DP users, suppliers like Siemens went their own way and introduced Profibus PA.
PA integrates with Profibus DP, and PTO spokesman Carl Henning adds it isnt that different from DP. In fact, the protocols are identical, and only the physical layers are different. It shares the same physical layer and baud rate as Foundation Fieldbus H1, but doesnt provide control in the field.
As my friend at Siemens likes to say, Profibus offers breakfast, lunch and dinner, or solutions for discrete devices (DP), process I/O (PA) and Ethernet (Profinet). This is unlike Foundation fieldbus, which offers two (H1 and HSE). Also, HSEs implementation by the supplier community has been limited to Smar and ABB. Curiously, these are the same two suppliers that offer native support for Profibus DP and PA.
In terms of applications, the Profibus end-user community is largely defined by the host systems that support it. Besides suppliers to discrete parts makers such as Siemens and Schneider Electric, only ABB, Invensys and Smar and its clones offer native support for PA. The user base is shaped along the lines of hybrid process plant PLC applications, including breweries, pipelines, batch chemical, pharmaceutical and ethanol plants.
So, if you ask someone in Fluors or Bechtels offices in Houston how much Profibus PA is going into their clients projects, the proportion is smaller than Foundation fieldbus. In fact, speakers representing Bechtel at a recent conference in Antwerp estimated that roughly 50% of new projects are installing Foundation fieldbus, while the remainder is mostly conventional and/or HART. Until DCS suppliers such as Honeywell, Emerson and Yokogawa have proven applications using PA, interest in Profibus by the large process industries may be limited to DP, mainly for motor control center integration. But, globally, the protocols are on par, adds Henning. While Profinet was positioned to integrate other protocols, including Foundation fieldbus, many large suppliers are content to provide their own, proprietary system-level networks (Figure 1).
Coordination by Profinet
Figure 1. As the Ethernet-based version of Profibus, Profinet is one of several industrial networking methods that can help coordinate communications between several fieldbus protocols.
A Strong Foundation
Meanwhile, Foundation fieldbus is a popular choice, even in Europe. At its meeting in Antwerp this year, FF touted its process industry products. However, most Foundation fieldbus applications are limited to H1, its two-wire network with the same physical layer as Profibus PA. While high-speed Ethernet has been part of FFs specifications for years, commercial implementations of HSE are still relatively few.
What was originally H2 (hunk two) back in the days of SP50 hasnt caught on, mainly because most DCS suppliers that dominate the large process industriesHoneywell, Invensys, Yokogawa, Emersonchose to implement a proprietary network, with all current offerings based on Ethernet. And end users voted with their dollars, reinforcing impressions that delivering H1 is sufficient. HSE capability hasnt been the differentiator that H1 has been. Asked if support for HSE would ever be a differentiator for system choice, one user says, For internal DCS communications, neither pro nor con. HSE seems to be a dead letter. If they pushed everything to OPC, then I might get excited, assuming they had tools to keep servers and clients synchronized.
This choice of system architecture harkens back to the heritage of these systems. Unlike PLCs, a DCS was traditionally sold as a system. Unlike the users who primarily used PLCs for control, the industries that wanted a DCS were shopping for a solution, even when this slogan wasnt part of the marketing vernacular.
Walt Driedger of Colt Engineering in Calgary, Alberta, Canada, says that, When you buy a PLC, youre buying the engine, and so you may be on your own to provide operator interface, historian, etc. When you buy a DCS, youre buying the whole vehicle. While many PLC vendors raked together some standard operator interface, historian, alarming and reporting packages that allow them to be called a DCS, they are rarely found on the bid list for a large process plant project. Yokogawa likes to say, We have reliability in our DNA. Users in the large process industries have a senseor a prejudiceabout who has reliability in their DNA, and are very reluctant to step out unless a system has been vetted by their peers.
These heritage DCS suppliers have always controlled the system-level network, and still see it as a critical to their offer. Charlie Piper, Invensys senior development program manager, says, The system network for the process automation system is a vital part of our supply scope. It needs to be extremely robust. Protection against single points of failure isnt enough. I/A Series mesh network can tolerate multiple faults in different locations, while still communicating among all network equipment, and it contains patented technology unavailable commercially to do so. The system network must tie together, not only DCS controllers, but also safety and supervisory controllers. Its performance and peer-to-peer capabilities must be flawless. The system network also needs scalability. We have facilities that connect 50,000 or more instruments and field devices.
And as Microsoft Windows security patches, bug fixes, and hardware changes are released, classic DCS vendors are expected to do exhaustive tests to ensure their installed base doesnt have a hiccup.
Some people grouse that proprietary networks are maintained to lock in customers, and with respect to safety systems, they may have a point. The effort and expense to connect a foreign SIL-capable logic solver may compel many to default to the DCS suppliers standard, and nearly all of the aforementioned vendors have bonafide SIL-3 logic solvers. However, large system users may think twice before connecting a SIL-capable system to any open-protocol control network, especially with growing cybersecurity worries.
Dawn of the One Network?
As you read this issue of Control, youll no doubt notice many ads offering Ethernet TCP/IP connectivity for many flavors of I/O. Whether you use Modbus TCP/IP, industrial Ethernet, Profinet or EtherNet/IP, you can buy inexpensive I/O to ride on it, along with converters for RS-232, RS-485, Modbus, AS-i or wireless.
However, this doesnt mean you can hook a Cat-6 cable to a spare RG45 jack on your host systems network switch and start reading and writing to the I/O. Maybe youre brave enough if your system is small and lightly loaded, but how many of us would risk unknown network traffic from a device that wasnt explicitly approved by our host vendor? Early wireless pioneers sent measurements to the World Wide Web, and read them down into their historians because no DCS engineer at these beta sites trusted their proposed system interconnection. Hodson adds, Interconnecting via TCP/IP over Ethernet assures arrivals of messages, but this doesnt mean theyre understood by the communicating parties. As long as there are different application layers and application object models for Foundation fieldbus, Profibus, DeviceNet/ControlNet, HART and the others, there wont be meaningful interconnections.
Now, Profibus, Foundation fieldbus and HART have been playing well together for a few years and cooperating via electronic device description languge (EDDL) and on the new Wireless HART interfacethe backbone that brings data into the host. PTO and FF also are offering to work on the same service for the ISA-100 wireless standard, if it emerges.
However, systems using HSE as the PCN backbone are few (ABB and Smar), and systems using Profinet as the PCN backbone arent a dominant fraction of bonafide, large-process applications. This means many users will bring in Wireless HART through gateways, which have limits. Hodson adds, Gateways may offer connectability, but they almost always have functional sacrifices and need some application configuration.
Large-process users all support open standards. One senior process control consultant from a major oil and gas firm, who is on the team that qualifies suppliers for their bid list, says that, With all things equal, the preference would be for an open PCN standard. However, the equals on the bid list dont show a strong leaning toward an open standard for their PCN, and this doesnt seem to affect any suppliers ability to win jobs. Whether large-system users will ever vote with their dollars remains to be seen. Until then, its reasonable to expect proprietary implementations of Ethernet, gateways, and OPC interconnection to remain the status quo.
For those of us in smaller I/O count facilities, where traditional PLC or hybrid architectures are the norm, the current environment may indeed look like its being taken over by Ethernet. Choices abound, and even intrinsically safe and out-of-the-box redundant Ethernet solutions are available. That numerous protocols and application layers exist doesnt seem to be slowing anyone down. As long as your business allows more diluted accountability for system troubles, end users or their system integrators may feel free to choose. But when an enterprise agonizes about lost production and call-outs at 3 a.m. on a holiday weekend, even network-savvy system integrators may be compelled to choose single-source accountability.
Perhaps todays increased network speeds and processing power will allow open protocols like OPC UA to make dissimilar connections appear seamless, but uptake by conservative users still may be slow. Proven-in-use would help, but it would probably end with the system having to be re-qualified [for its bid list] adds a long-time user at an oil and gas firm. Another fieldbus end user adds, To me, open standards are only useful when you want to have different vendors products talk. Its becoming more important, and we are dragging the vendors kicking and screaming along with us.
With many engineers working increasingly far from nitty-gritty process control networks, reliance on system integrators and vendors will remain the norm or increase. Our present mish-mash of networks and protocols will likely persist too. So it seems our suppliers are wise to claim to be all things to all people, like Micro Motion supporting every protocol it can afford.
The One Network may be a real possibility, but constraints on end users, their business and operations clients, and suppliers interests means every-bus, anybus, OPC and Modbus will be in our plants for years to come.
John Rezabek is a Control contributing editor
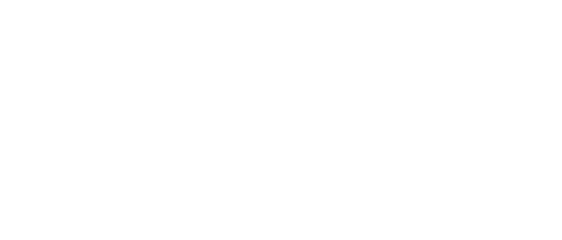
Leaders relevant to this article: