CAN TODAY'S simulation software systems design the product, the plant, and the control system? Maybe yes and maybe nodepending on the type of simulation. Armed with a good CAD package and mechanical design simulation software, one engineer can seemingly do it all: design a pipe, tank, or gear; define its structural and material aspects; set up a program to manufacture it, and design a plant around its manufacture. But is the story the same for process simulation?
When considering simulation, we often think of flight simulators because theyve been around for so long. And the question follows, if we can build flight simulators, why cant we build process simulators that can do as much as mechanical simulators, with extreme precision and 100% accuracy? While there have been major strides in process simulation software for chemical and petroleum applications, designing a process and control system for a plant is quite tricky given variables and measurement inaccuracies. Because of these challenges, the concept of a one-person design team is still a goal for the future.
Gilles Hameury, sales and marketing manager for France-based Prosim, says simulation has more than 50 years of history with time-proven models accepted by both scientific and industrial communities. These can be thermodynamic models or unit operation equations. Given the complexity of chemical processing, says Hameury, 100% accurate simulators are a fantasy. However, in some areas that have been extensively explored (alcohol production, for example), we can reach 95-98% accuracy, which would be used happily by any engineer. He notes that the remaining error is due to real-life issues (product impurity, temperature or experimental measures inaccuracy) and can be ignored, adding that the simulator can be adjusted with experimental data to get close to 100% accuracy.
The simulation packages to accomplish this degree of precision and accuracy are referred to as high-fidelity simulators (See Figure 1), and typically start at $100,000. According to Grant Stephenson, principle engineer, Honeywell Process Solutions, flight simulator software and simulation products for the nuclear power industries are perceived as absolutely necessary because the public is concerned about air safety and potential nuclear accidents. Thus, the aircraft and nuclear power industries invest in a high level of simulation fidelity. Stephenson suggests, for example, the recent Air France accident in Toronto could have been much worse if pilots hadnt trained rigorously on simulators.
Controls at BPs Saltend, UK, chemical production facility. Honeywells HYSYS and OTISS dynamic simulation software optimize process and train operators.
Since low-fidelity simulation software comes with most process control software packages, Dave Chappell, technology leader at Procter & Gamble, thinks control engineers would be foolish not to take advantage of it. This software, which is significantly less inexpensive than high-fidelity tools, lets control engineers verify that automation is programmed correctly. In many cases, these simulation packages are built into the control package as part of the platform. Chappell notes that P&G probably doesnt have any two process applications that are exactly alike. Therefore, its reasonable to assume that modeling all these applications with high-fidelity simulation products could take a lot of time.Todd Stauffer, PCS 7 marketing manager at Siemens, says more and more customers are considering simulation up front in their project lifecycle. In the past it was somewhat of an afterthought. Now manufacturers look to simulation as a means of reducing costs and increasing effectiveness of tasks, such as operator training, factory acceptance testing (FAT), installation and commissioning, and for testing configuration changes prior to incorporation into running processes.Real-World Applications
Stephenson contends that dynamic process simulators can model at a much higher fidelity than exists now. This capability, however, often isnt employed since the process industry is not governed or managed in the same way as the aircraft industry. However, there have been very serious incidents in the process industry, which might not have occurred if regulations mandating incident avoidance were stronger. BP Chemical Production
Besides modeling processes, simulation systems ensure operational competence, safety, and plant reliability. This is the key requisite in BPs Saltend facility (See Figure 2), located on the east coast of England, near the North Seas oil and gas fields. The company manufactures bulk chemicals, such as acetic acid, acetic anhydride, and acetone, at this site. Its experience with process simulation goes back to 1989. Presently, BP has three simulation systems, each equipped with Honeywells Icon operator consoles for use with more than 20 dynamic models, including HYSYS and OTISS, which are part of UniSim operations suite. Other goals for simulation include maintaining operational competence:
- With increased intervals between scheduled shutdowns, namely achieving two to three years of continuous operation;
- During increased use of advanced control that has resulted in reduced opportunities for operational hands-on;
- During periods of staff restructuring for greater flexibility, such as responsibility for unfamiliar plants; and
- During periods of demographic change to allow for staff retirements.
During oil processing, heavy products are broken down by high temperatures into lighter products in cokers. This cracking process strips off lighter liquid hydrocarbon products such as naphtha and gas oils, leaving the heavier coke behind. Dr. Peter Witt, a research scientist at CSIRO Minerals, reports, Our company is using simulation software to help Syncrude Canada Ltd. reduce the coke deposits that build up in its fluid coker stripper (Figure 3), while maintaining or improving hydrocarbon stripping. CSIRO is part of Australias Commonwealth Scientific and Industrial Research Organization. Syncrude is the worlds largest producer of crude oil from oil sands and the largest single-source producer in Canada.FIGURE 3: HIGH FIDELITY SIMULATOR
A long-time user of Ansys CFX simulation software, CSIRO collaborated with Clean Power from Lignite CRC to develop the fluidized bed model in CFX-4. Because of its multiphase capability and its ability to be extended into new application areas, CFX is used by CSIRO to perform complex computational fluid dynamics (CFD) modeling of multiphase, combustion and reacting processes in the mineral processing, chemical, and petrochemical industries. In the past, physical modeling was used to understand the flow of solids and gas in the stripper. This modeling is performed at ambient conditions, so scaling of the physical size and materials is required to approximate actual high temperature and pressure in the stripper. The scaling process can introduce some uncertainty in understanding the actual stripper operation.Using CFD modeling (Figure 4) to compliment the physical modeling programs allowed CSIRO to eliminate scaling and also use the facilitys actual dimensions and operating conditions. Also, CFX simulation provides much greater detail of the flows and forces in the stripper than can be obtained from physical models or from the plant. This is due to the difficulty of making measurements and visualizing the flow in complex multiphase systems.
Three dimensional fluidized model of the Syncrude fluid coker stripper. The model predicts the motion of bubbles (in purple) rising from injectors in the lower part of the bed and the complex flow behavior of coke particles. Flow simulations provide insights into the stripper operation, which are used to improve the design.
As the worlds largest privately held chemical company, Huntsman annually manufactures more than 30 billion pounds of highly integrated products for a variety of global industries, including chemicals, plastics, automotive, paints, coatings and packaging. Huntsmans polypropylene production capabilities encompass PP homopolymers, PP impact copolymers, PP random copolymers, and PP specialty grades. The companys plant in Longview, Tex., uses two Unipol polypropylene lines to produce about 260 KTA. The Longview facility specifically wanted an advanced process control solution that would maximize production of it impact copolymer line while minimizing off-specification product and related costs. Huntsman chose Pavilion Technologies to provide a modeling and simulation solution for its impact copolymer line. Specific project objectives included improving product quality and consistency, eliminating existing process control problems/reject upsets, reducing transition times, and improving reactor stability through controlling condensed and reactive propylene and bad weight. The project was completed in less than three months, which was two months ahead of schedule.The implementation included Pavilions Process Perfecter advanced process control solution, which combines proprietary nonlinear steady-state optimization and model predictive control to deliver a solution capable of controlling quality targets, performing automatic transitions, changing bad weight, and rejecting disturbances. Key benefits to this implementation included a 40% flexible production rate increase (without affecting resin properties), 25-70% reduction of product quality variance (depending on the product), reduced transition times, improved catalyst activity, and an annual polypropylene production value estimated in excess of $1 million annually.It is highly likely that with the rate of improvement of simulators, even in the chemical processing industry (see The Light at the End of the Tunnel is a Train, CONTROLs August cover story) that not only will one engineer be able to design an entire plant using simulation, but also be able to train operators, prototype changes, and operate the plant with one operator per shift.
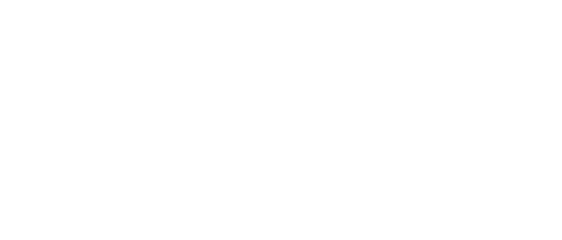
Leaders relevant to this article: