By Ed T. Ladd Jr., HCF
MYTH #4: HART offers little value for Plant Control Systems and Enterprise Level Networks.
FACT: Accessiong the data in HART devices on a "full-time" routine basis increases performance, integrity, and reliability of plant control and enterprise level systems. Retrieving digital data directly from the device can avoid potential filtering that may occur in acquiring this information through intermediate systems.
Traditionally, a HART enabled instrument’s analog signal transmitted the primary variable and additional variables and diagnostics were confined to the device. HART technology was used only for setup, calibration or as a maintenance tool.
The practice of intermittent communications with a device for startup and troubleshooting has provided exceptional value for users of the technology. However, using the technology in this manner limits the capabilities of a device within the real scope of a process plants operation. The continuous monitoring of the HART digital channel can open the door to improved performance.
Continuously monitoring a HART enabled instrument’s process variable via the digital channel can lessen the impact on the precision (not the accuracy) of the measurement by reducing the number of conversions the data must go through. Although slower than the analog channel, the digital channel provides high-resolution measurement values for up to four measurement variables including information on engineering units, data quality and the status of the device.
With a fully enabled HART system, devices can now provide the ability to take the intermittent diagnostic methodology to a new level. Whether a complete control system or a single loop interface, the integration of a continuously monitored HART digital channel will reduce downtime by using the onboard diagnostics and data provided in every HART- enabled device.
Today, there are many ways to integrate the valuable information provided by a HART-enabled device. The big question is “How do you get started with your existing system?”
To “See What You Can Do” with HART there is no reason to start big, it’s just important to start. First, find a control loop that needs to be monitored, add a single loop interface (an example is the HIM by Moore Industries), and begin monitoring the information provided by your HART-enabled device.
The single loop interface allows a user to access all of the additional variables provided by a HART-enabled device and transmit the values via one of the interfaces analog outputs. In addition to the analog outputs, single loop interfaces have the ability to provide contact closure alarm outputs. The contact closure alarms can be programmed to change status on either a process alarm or a change in the device’s status.
The HART field device status response, returned with every command contains information regarding the devices health including notifications listed in Table 1.
Table 1 - Field Device Status Response
Device Malfunction | The device detected a serious error or failure that compromises the device’s operation. |
Configuration Change | An operation was performed that changed the device’s configuration. |
Cold Start | A power failure or device reset has occurred. |
More Status Available | More status information is available using HART Command 48, Read Additional Status Information. |
Loop Current Fixed | The loop current is being held at a fixed value and is not responding to process variations. |
Loop Current Saturated | The loop current has reached its upper (or lower) endpoint limit and cannot increase (or decrease) any further. |
Non-Primary Variable Out of Limits | A device variable not mapped to the PV is beyond its operating limits. |
Primary Variable Out of Limits | The PV is beyond its operating limit. |
By configuring a single loop interface’s alarm output to trigger on one of the responses listed in table on or when a device’s status is changed the system will be notified of any potential situation occurring with the device. With this advanced warning, maintenance personnel can easily schedule additional troubleshooting using a handheld communicator or another HART communication program.
Finding a place to start integrating the data HART provides is the key to future improvements in process performance. Users will see immediate results when monitoring HART equipment in real-time, preventing an information gap between system and device.
Close the information gap and “See What You Can Do” when you use the “Power of HART”.
Upcoming HART Connection articles will provide information on applying HART technology, application notes to help you implement new HART strategies and what to expect from a HART-enabled device or host system. For more information, contact the HART Communication Foundation or visit the website at http://www.hartcomm.org.
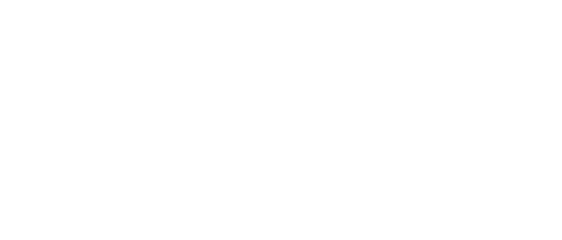
Leaders relevant to this article: