By Ian VerhappenONE OF THE REMAINING “hurdles” to the adoption of fieldbus technologies in the automation and control realm is that a significant number of the engineering procurement construction (EPC) firms that design and install facilities are not including fieldbus as an alternative in their proposals.Part of the reason for the reluctance to make this change is just that, it is a change with all the apprehension and “baggage” associated with those types of events. Change also comes with a number of expenses for such things as:Procedures – Systems in place defining how something is to be done will now have as a minimum be modified to reflect the addition of this new technology or technologies depending on the number of fieldbus types being considered. In many cases, if fieldbus technology is selected for a project no one fieldbus is capable of meeting all the I/O needs and therefore multiple buses, plus traditional analog or discrete signals will be combined in one system. New ways of keeping track of which type of signal is doing what need to be developed. This leads to the related change in -Work Processes – The amount and type of interaction between the engineering discipline design teams is different in fieldbus, especially if you want to be able to support field based control. This means that the process engineers need to sit with the automation engineers to confirm the interactions between field devices while the electrical engineers need to be there to discuss the physical location of the equipment to minimize the cable runs and installed cost, and the instrument engineers to specify the actual devices. Fortunately, the automation and instrumentation folks are frequently the same person.The team also needs to determine who on the team is doing what? With the field devices and associated field termination equipment now part of the control system network, should the design of the cable and I/O be done by the electrical staff or instrumentation staff?Design Tools – New design tools are required to calculate the limitations and layout of these new networks.Calculations –Traditional point-to-point systems were only concerned with having enough energy for a single device, now designers not only have to consider the energy at multiple devices, there are also a number of other rules and limitations on such things as total cable length, cable terminations, Communication Resources and network cycle times to be considered for which the necessary data must be collected.Fortunately, a selection of free tools is available from a number of suppliers that help in this regard, though each of them has their limitations.Training – New skills require training of people so that they can learn, then apply them. Unless a large project is willing to include training as part of the “cost of using new technology” this requires and investment in unbillable time, reducing the profitability by increasing overhead.Add to this that once the skills are learned, experience has shown that designing fieldbus systems requires fewer hours than traditional point-to-point analog controls which results in lower invoice and revenue, the problem becomes bigger.Compounding the difficulty, is that despite what we who have “seen the light” like to think, instrumentation and control is NOT a core component of most EPC’s but rather a necessary support service needed to be able to sell the “bread and butter” of process and mechanical engineering. Of course the Automation Suppliers, for whom this is a core competency, are filling this void by becoming not only host system suppliers but complete automation suppliers responsible for everything from the field device, through the control system to the final control element.Fortunately, not all is bad news. The good news is that some End Users are forcing the EPC’s to include fieldbus as a deliverable and as a result some companies are learning these new skills. In addition, some EPC’s are viewing having fieldbus capable staff as a competitive advantage to not only bidding on projects but also in recruiting and retaining their staff and are investing in bringing these skills into their organization through training or subcontracting arrangements with specialists.Fortunately, a number of institutions around the globe are also offering fieldbus training so that interested organizations can obtain vendor neutral introductions to the technology.After this design “hurdle” has been crossed, the next and close to last one remaining is the installation contractors. That however is another column and one we will discuss in the near future.Next column we will talk about “industrial Ethernet” and what the term really means. As always, your comments and suggestions on the above as well as for potential future topics of discussion are encouraged. Please contact me at the information below.
Ian Verhappen is an ISA Fellow and Director at ICE-Pros Inc., an independent Instrument and Control Engineering consulting firm specializing in fieldbus, oil sands automation, and process analyzer systems. Ian can be reached at[email protected]or through his web site www.ICE-Pros.com.
About the Author |
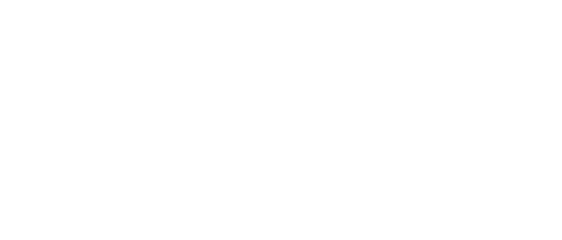
Leaders relevant to this article: