H |
ardware and software advances are allowing inexpensive yet effective implementations of asset management systems for rotating and reciprocating equipment. It is no longer necessary to purchase and install large, complex and expensive systems to realize substantial reductions in maintenance expenses and increases in uptime through asset management.
Asset management of rotating and reciprocating equipment involves condition monitoring, diagnostics and predictive maintenance. Key advances that work together to ease asset management implementation are wireless communications, digital buses, and distributed control. Let’s look at an example asset to show how these technology advances are reducing the cost of asset management.
Let’s say there is an item of rotating or reciprocating equipment in your plant that experiences frequent downtime. In the past, asset management of this equipment would have required you to install scores of vibration, temperature and pressure sensors to monitor the device. Each of these sensors would then have to be individually wired back to a central host distributed control system (DCS) or a dedicated equipment monitoring system. In either case, complex and expensive asset management software would have to be purchased, installed and configured at the host.
Linking this asset management system to other plant control and information systems would have been another expensive and arduous task.
To accomplish the same task today, you might purchase an inexpensive local condition monitor. Local condition monitors can be connected to multiple machine sensors via a single sensor bus cable. Data from such monitors can also be transmitted back to a host via wireless or wired Ethernet. Asset management data is also accessable through any web browser. Local condition monitors allow end users to approach asset management at their own pace, and to address the highest payback items first.
“When compared to traditional centralized systems, today’s distributed systems can be implemented in less time, at lower cost, and with far less complexity,” reports Rick Schiltz, director at the center for integrated condition monitoring. “Hardware can be locally installed at the machine, significantly reducing wiring cost and intricacy of installation. Instead of proprietary communications protocols, manufacturers can use open standard protocols.”
GE Energy, formerly known as , has just introduced a local monitoring system to fit these parameters. “New in 2005 is a monitoring system positioned between a conventional rack-mounted series of modules and simple vibration transmitters,” says Jeff Rudd, product line manager for condition monitoring at GE Energy. “This small, multi-channel monitor has up to four temperature and four vibration inputs, and a detachable display.”
GE Energy and others also make condition monitoring modules that plug directly into industry standard bus systems and interface directly to name brand PLCs and DCSs. This is another path to inexpensive and incremental implementation of asset management.
Another asset management technology advancement is a rugged pressure sensor that can monitor the pressure-volume conditions found inside reciprocating machinery. “We just introduced a new pressure sensor that can continuously measure in-cylinder conditions,” adds Rudd. “A comprehensive suite of monitoring technologies for reciprocating machinery now exists including pressure-volume monitoring, piston rider band wear, valve condition, wrist pin wear, impacting, bearing condition, and oil condition.”
Basic machinery protection through sensors equipped with high and low alarms is giving way to more sophisticated condition monitoring. “15 years ago, only 10% of the machinery protection systems supplied were connected to online condition monitoring software,” according to Rudd. ”Today, that number is approaching 50%.”
Vendors recognize end-user demand for condition monitoring, and most now supply asset management software and hardware as an option with their control systems.
Larger vendors are providing very sophisticated model-based software to make sense of the reams of data generated by asset management systems. “Process data allows the use of models to determine equipment operating performance,” says Kevin Fitzgerald, senior program director for asset performance at .
Models can be first principles or inferentially derived. First principles models use algebraic heat and mass balance equations, supported by thermo-fluid equations. Inferential models, often derived from neural net techniques, can also be used to determine asset set or equipment performance.
The heart of this approach is to develop a model of performance tuned to the actual equipment or asset set. In addition to vibration measurements, the models also make use of temperature, pressure, flow and other information from the equipment or its surrounding ancillary components.
Once an adequate model is developed, the residual or difference can be calculated between model performance and actual observed performance. Depending on its magnitude, this residual may then be used to drive a warning or maintenance trigger.
The heart of this approach is to develop a model of performance tuned to the actual equipment or asset set. In addition to vibration measurements, the models also make use of temperature, pressure, flow and other information from the equipment or its surrounding ancillary components.
Once an adequate model is developed, the residual or difference can be calculated between model performance and actual observed performance. Depending on its magnitude, this residual may then be used to drive a warning or maintenance trigger.
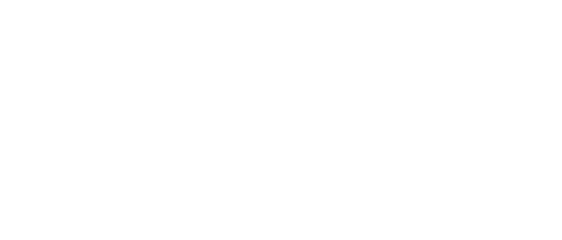
Leaders relevant to this article: