"We got together and talked about how projects are run, and realized we're doing it the same way today as we did 35 years ago," said Mark Murphy, director, control systems, Fluor, in his session, "Engineering Outside the Box" at this week's Emerson Global Users Exchange 2015 in Denver. "Back then, we wrote the instrument specifications on forms with pencils and did the drawings with pen and ink. Now we use computers, but we take the same approach. We look at the last project and use the same specifications. We're force-fitting the new tools to do engineering the old way."
Murphy's group decided to look for ways to gain efficiencies by adopting modern technologies. "We took a recent grass-roots project and reviewed it to see how it could have been done better," he said. The group evaluated each step, each task, and found seven areas where they could save a lot of time and money:
- Use small I/O junction boxes with non-incendive wiring;
- Use wireless instrumentation to eliminate wiring;
- Reduce footprint of remote instrument enclosures;
- Eliminate loop diagrams;
- Buy transmitters in bulk;
- Configure transmitters in bulk; and,
- Leverage a plant-wide wireless network for startup/commissioning
CHARM down wiring costs
"Using all seven methods adds up to considerable savings—the project cost went from $180 million to $48 million for a savings of $133 million." Fluor's Mark Murphy on the efficiencies to be gained by using new tools and technologies in the design and execution of capital projects.
Total installed cost includes both materials and labor. "Labor is expensive in southern California, so it can make sense to spend a little more on materials," said Adrian Lee, director, control systems, Fluor.
To minimize cross-wiring and marshalling, use fiber. "Remote I/O radically reduces wiring connections and the costs that go with them," Lee said. For example, wiring 12,500 I/O the conventional way, with 350,000 terminations and 201,000 wire markers at 15 minutes apiece takes 1.4 million man-hours. Using remote I/O such as CHARMs reduces terminations to 65,000 and markers to 27,000, or about one-sixth the time. This not only saves money, it can shorten the whole project schedule.
It pays to optimize the size and number of junction boxes. Using a larger number of smaller boxes, placing them closer to the instruments, and connecting them with fiber minimizes the lengths of wiring runs. For the 12,500 I/O example, using 48-CHARM boxes instead of 96-CHARM boxes adds about $785,000 or about 10% to that part of the DeltaV hardware cost, but by reducing average wire runs to 100 ft. from 150 ft., saves more than $16 million in wiring labor and materials.
In North America, Division 2 wiring is most common, which requires conduit and safety permits for field work. Intrinsic safety (IS) is common in Europe; it uses no conduit but requires expensive IS barriers. Non-incendive requires no conduit, no barriers, and no permits for field work, so it has the lowest overall installed cost. On this project, Division 2 wiring would cost $114 million, while non-incendive would cost $42 million.
"The smaller junction box with non-incendive wiring is the clear winner for this project," Lee said.
Maximize wireless, minimize RIEs
"Use wireless wherever it makes sense," said Murphy, in the DCS but not the SIS, for monitoring, where redundancy is not required. "Equipment modules are a great place to use wireless. You can build them remotely, then fit them in without having to run conduit or trays."
If the example project used wireless on 22% of its 7,900 analog inputs, requiring 35 gateways in 13 areas, it would cost $3.5 million, "But it would save more, for a net savings of $1.8 million," Murphy said.
Remote instrument enclosures (RIEs) cost about $600 per square foot. Taking advantage of modern hardware ruggedness, client requirements and the mild southern California climate, Murphy's group eliminated five RIEs and added 12 three-sided shelters for a net savings of $4.2 million.
The group found they could eliminate loop drawings by letting the connection drawings become the loop drawings, and simplify the connection drawings using CHARMs for a net savings of 22,000 engineering hours at $100 per hour, a total of $2.2 million.
Buy and configure transmitters in bulk
"Instead of writing a data sheet for every tag and handing 7,000 pieces of paper to Rosemount, we can define standard specifications that cover multiple transmitters," Murphy said. For example define high pressure, medium pressure, low pressure, and temperature "boxes" and simply order the number of each type of transmitter needed to do the project, unconfigured and untagged. "Using one common data sheet for each box of transmitters saves 25% on engineering and 50% on warehousing," said Murphy, and it prevents the problem where the wrong transmitter is issued and later has to be replaced with a rush order.
When it's time to configure, "Today, the state of the art is 1.0, and autoconfiguration 2.0 is still a ways off," said Larry Lammers, proposal lead/SME, project and automation services, Caltrol. "So to use generic, untagged transmitters, we need to coordinate and synchronize three tag locations." Here's how it can be done.
First, use DeltaV Bulk Import to assign the tags to the channels. Then use AMS v13, with bulk configuration capability, to set the user configuration for each type—each "box"—of generic transmitter. "Use one data sheet for all," Lammers said. Identify the parameters to write to the device, standardizing on a few very specific configurations. "Take advantage of the high accuracy of today's transmitters to use a broad specification, for example, 0-500 psi, and minimize the number of user configurations." Fluor found they could do the entire project with a few hundred templates.
Next, create a simple table in Excel to map the device tags to the user configurations, and import the file to DeltaV. Then use AMS v13 Bulk Transfer tool to map user configurations to the transmitters based on their assigned tag name. The mapping of configurations to tagnames becomes active. Some are live, some are virtual—awaiting connection of the transmitter.
Connect the generic field device to the CHARM, and reconcile the device in DeltaV Explorer, which will auto-sense the HART device and push the tag name previously bulk imported. When a connected device has a tagname that matches an active Bulk Transfer mapping table, AMS automatically transfers the device configuration.
"Emerson estimates 80% time savings on transmitter configuration alone, using this approach," Lammers said. "We estimate more than that."
Commission with style and grace
Now it's time to use a plant-wide wireless network to streamline commissioning. By equipping technicians with mobile devices supporting AMS Device Manager Client SC and a view-only DeltaV display, they can perform loop checks quickly and independently, without a board operator.
The project proposes a Cisco mobile worker network with 14 access points and an equipment cost of $211,000. It saves $155,000 in mobile worker labor and earns $3.3 million by accelerating start-up.
"Using all seven methods adds up to considerable savings," Murphy said, with the largest component in the wiring. "The project cost went from $180 million to $48 million for a savings of $133 million."
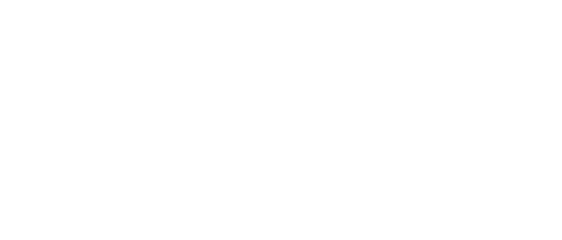
Leaders relevant to this article: