Mix, match hazardous, non-hazardous signals
LB/FB also allow barriers to be more easily installed in Division 2 and Zone 1 hazardous areas, and feature reduced wiring, fewer DCS control cards, fewer terminations, no need for marshalling panels, reduced control cabinet space needs, and faster commissioning. They're also designed for general-purpose and intrinsically safe (IS) applications, and are rated for Division 2 mounting with inputs, and/or outputs mounted in a Division 1/Zone 0 area. FB systems are designed for IS or increased safety applications, and are rated for Zone 1 mounting with inputs, and/or outputs mounted in a Zone 0 area.
With LB systems, IS and general-purpose modules can be mixed and matched on the same backplane. LB systems include a backplane, communication interface, power supply, and I/O modules. They can be DIN rail mounted for easy integration, or pre-mounted by the supplier in an enclosure specified by the user.
With FB systems, IS and increased safety modules can be mixed and matched on the same backplane. FB systems include a backplane/enclosure, communication interface, power supply, and I/O modules. The system comes installed in the user’s choice of enclosure with GRP, fiberglass and stainless steel as standard options. FB systems are available with optional accessories that can be mounted in the enclosure to extend its functionality, including terminal blocks, fuses and disconnect switches.
Side-entry, push-in connections
Phoenix Contact
800-322-3225
Compact system with 132 I/O slices
Omron Automation
800-556-6766
Compact, push-in for power signals
Dinkle
832-539-4703
Wireless, IoT Ethernet I/O module
Newark
800-463-9275
Single-pole, spring-type blocks
Metz Connect USA Inc.
888-722-5625
Dry-contact, temperature, mixed-voltage
GRV-IDCSW-12 with discrete input, 12 channels and DC contact switch status, which monitors the open/closed status of dry contact switches, and provides the necessary excitation voltage to power the circuit. It's ideal for monitoring distributed IT equipment, benchtop analyzers, motor run/stop relays, or any device that offers only a dry contact for status. Because there’s no need to install separate power supplies to drive these dry contacts—since wetting and monitoring are both provided—this module can save time, money, space and installation labor.
GRV-IVI-12 with analog voltage input, 12 isolated channels, ±1.25 to ±160 V, and channel-to-channel isolation. With each channel configurable to one of eight ranges from ±1.25 to ±160 V, this module eliminates the need to segregate I/O signals over multiple modules, providing cost and space reduction for mixed-voltage applications. GRV-IVI-12 has 20-bit resolution and is accurate to 0.1% of the configured range. It includes options for scaling, filtering, averaging and more, speeding development time and distributing computation functions down to the I/O module.
GRV-IRTD-8 with analog input, eight channels, temperature/RTD or resistor, which increases options for accuracy and I/O density in temperature applications. It provides eight channels for two- and three-wire RTD inputs, with a maximum range of -200 °C to 850 °C. Users can take advantage of multiple, fixed ranges or one of two auto-ranging methods to simplify configuration. GRV-IRTD-8 can also be used for high-resolution resistance measurements, with accuracy ranging from 4.2 Ohms at the 8K Ohm input range to 0.058 Ohms at the 10 Ohm range for 3-wire RTDs.
PAC Project 10.2003 or the Opto 22 Library Package for CODESYS v1.0.2.0 are required for full support of these modules. The three new modules also feature:
• Two-position, hinged LED module cover that indicates module status and covers field terminations;
• Touch-sensitive pad to trigger module information display on the groov EPIC processor;
• Removable top-mounted connector with single, captive retention screw;
• Spring-clamp field wiring terminals;
• Hot-swappability for installation and removal without turning off or stopping the system;
• UL Hazardous Locations approval and ATEX compliance;
• Wide operating temperature range of -20 to 70 °C;
• Individually calibrated and factory tested twice—with no statistical testing; and
• Lifetime guarantee.
Opto 22
800-321-OPTO (6786)
Safety I/O simplify controls
Single-channel I/O for speed, savings
It's networked via an Ethernet fieldbus communication interface (FCI) with embedded redundant switches, and uses individual signal conditioning modules (SCMs) for process and safety I/O. Select I/O is also field-ready with a -40 °C to 70 °C temperature interface. It also has galvanic isolation per channel, while each SCM is current-limited with a unique ‘field disconnect’ mode for added protection and flexibility. Line monitoring DIs, SOE and high current options are also available to reduce the need for ancillary, third-party equipment, which aids in I/O cabinet standardization.
Select I/O's redundant Ethernet FCI makes it even more flexible. Beyond working with Select I/O, the FCI can accept System 800xA's multi-channel S800 I/O, allowing users to select the I/O solution that best fits their application.
Remote for mixed-valve terminals
CPX-AP-I enables valve terminals to be moved closer to pneumatic cylinders, which reduces pressurization time and increases equipment performance. Process data in and out of each bus module is as much as two kilobytes. Scan cycles for a mix of both valve terminals and I/O are below one millisecond, and are expected to approach microseconds. Latency is virtually nonexistent.
Communication and voltage supply are via two separate, galvanically isolated connecting cables, eliminating the potential for stray currents. Two separate wires enable the creation of voltage zones that provide reliable control for many processes.
CPX-AP-I comes standard with a pre-integrated IO-Link Master and IO-Link device tool for fast, effective application of IO-Link enabled devices. CPX-AP-I ensures each application can be individually optimized. Cross-communication between modules enables applications requiring high speed and rapid control.
CPX-AP-I remote I/O has the capacity of up to 80 I/O modules, which can be a mix of digital I/O, analog I/O, I/O-Link, and valve terminals. Furthermore, distances between modules is up to 49 feet (15 meters). CPX-AP-I has a theoretical upper limit of 500 I/O modules and 164 feet (50 meters) distance between modules.
Festo Corp.
800-993-3786
I/O scanner cuts DCS migration costs
TDC 3000 I/O Interface for ControlLogix allows reduced-risk migration for legacy Honeywell systems; 28 IOPs per PMIO scanner; redundant I/O Link (Channel A and B); support for integrating redundant PMIO Scanners into Logix with dedicated add-on-profile (AOP); diagnostics available in Logix; easy configuration with Slate Configuration Utility; and custom-length I/O Link cables sold separately.
[javascriptSnippet]
Precision measurement I/O extends modules
The economy line is available in two, four, six and eight-channel versions. High-precision measurements with an accuracy of 100 ppm are possible over a 10-40 °C temperature range. Each channel can be set to current or voltage measurements with a sampling rate of up to 1 ksps per channel. Analog signals in ranges from ±1.25 to ±10 V, 0 to 10 V, ±20 mA or 0/4 to 20 mA can be processed. ELM314x offers reduced channel costs, but provides the same functions as the ELM3x0x line, including freely adjustable, two-stage filters, over-sampling, distributed clocks, true RMS and scaler functions, as well as diagnostic features for unattended, long-term use.
Beckhoff Automation LLC
877-TwinCAT (877-894-6228)
Dual-channel transmitters cut costs, save space
DT series signal conditioners also have high-resolution A/D converters to perform high accuracy measurements with repeatability and stability. High-voltage isolation separates each input, output and power circuit from each other. Free configuration software helps users quickly select I/O ranges and precisely scale input/output limits. Each model supports several input ranges, and can output a proportional 0/4-20mA, 0-10V, or ±10 VDC signal. Removable, front-facing terminal blocks facilitate wiring. A rail power bus option can supply multiple units from a single connection or establish redundant power.
Acromag
248-295-0866
Gateway connects HART to IIoT
Moore Industries-International Inc.
818-894-7111
Integrates CoDeSys and IIoT
Weintek USA Inc.
425-488-1100
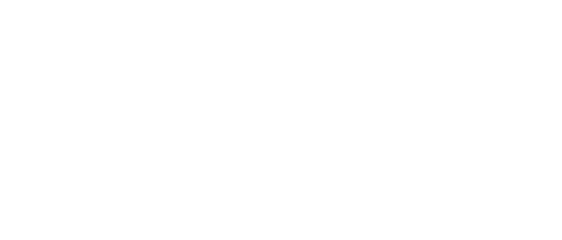
Leaders relevant to this article: